Surface treatment of road surfaces. TTK. Device for rough surface treatment of asphalt concrete pavement by single surface treatment
9.2.4.1 Surface treatment device technology includes:
– preparatory work;
– surface treatment device;
– care of the installed surface treatment;
– quality control of the formed surface treatment layers.
9.2.4.2 Before starting surface treatment work, you must:
– assign a surface treatment design and determine the required fraction of crushed stone and its consumption rate in accordance with Tables 9.1 and 9.2;
– establish the type, brand and consumption rate of organic binder for the main bottling in accordance with tables 9.2 and 9.3;
– carry out quality control of the materials used and preliminary control of the dosage and uniformity of distribution of materials;
– prescribe (if necessary) based on the results of laboratory tests the technology for introducing targeted additives;
– carry out repairs to the coating (if necessary) in order to eliminate existing damage and deformations (potholes, subsidence, sagging, cracks, etc.), eliminate unevenness of the coating by milling or laying a leveling layer. When performing pavement repair work using hot asphalt concrete mixtures according to STB 1033, surface treatment is carried out immediately after completion of the work; when using cold asphalt concrete mixtures - no earlier than 12 days. During the calendar year, repair work using bitumen-mineral hot cast mixtures in accordance with STB 1257 is not allowed before the surface treatment device.
9.2.4.3 If there is transverse unevenness in the coating in the form of ruts up to 20 mm deep, the ruts are repaired using surface treatment. The track repair technology includes the following operations:
– cleaning the repaired coating surface from dust and dirt;
– distribution of binder and crushed stone along the track;
– compaction of the laid layer;
– sweeping away loose rubble.
The size of the crushed stone fraction must correspond to the rut depth; material consumption rates are prescribed in accordance with tables 9.2 and 9.3. When using bitumen emulsion, rut repair is carried out using machines with synchronous distribution of materials.
Surface treatment of the entire surface is carried out no earlier than 24 hours after the completion of repair work to eliminate ruts.
9.2.4.4 Processing of crushed stone with binder is carried out in asphalt concrete mixers of cyclic or continuous action. The amount of binder is 0.5% by weight of crushed stone, the temperature of crushed stone and binder in the mixer is 140 o C. The duration of mixing crushed stone with binder is at least 120 seconds.
9.2.4.5 Processing of crushed stone with a binder can be carried out on specially prepared sites with hard surface, excluding dust formation and provided with drainage. The crushed stone laid in a roller is distributed with a motor grader in a layer 15 to 25 cm thick. Bitumen, liquefied to 200-250 degrees of penetration and heated to a temperature of 160 o C, is poured with a tar in two stages. After each pouring, the crushed stone is mixed with a motor grader (collected into a roller and leveled). In this case, the motor grader blade is installed at an angle of 30-40 o. The number of passes of the motor grader after the first filling is from 6 to 8; the total number of passes is from 25 to 30.
9.2.4.6 Crushed stone treated with binder should be stored in a stack in warehouses or under a shed. The storage period should not exceed 3 months. To prevent caking of crushed stone, it is sprayed with water before storage. Water consumption is from 0.5 to 1% by weight of processed crushed stone. The height of the crushed stone stack is no more than 2 m.
9.2.4.7 The surface of the coating is cleaned with mechanized brushes, moistening heavily contaminated areas in 2-3 passes along one track. When using bitumen as a binder, it is necessary to ensure that the coating is completely dry before applying the surface treatment device.
9.2.4.8 Subpriming is carried out on cement concrete pavements without surface treatment, and also in the presence of a network of cracks or peeling - on asphalt concrete pavements with a hardness degree of T or H.
9.2.4.9 Coatings are primed by pouring bitumen, liquefied to a viscosity of 200 to 250 degrees of penetration. For cement concrete pavements, it is recommended to add adhesive additives to the bitumen for priming. When used as a binder for surface treatment of bitumen emulsion, the primer is performed with a 30% emulsion. The filling rate of liquefied bitumen is from 0.3 to 0.5 l/m2; bitumen emulsion - from 0.5 to 0.6 l/m2. The priming is performed 2-3 days before the surface treatment device. At the same time, the speed of traffic on the site during the specified period should be limited to 40 km/h.
9.2.4.10 The surface treatment device is produced by a set of machines,
which includes machines for separate distribution of materials (asphalt distributor, mounted or trailed crushed stone distributor) or special machines for synchronous distribution of materials, as well as self-propelled rollers on pneumatic tires.
9.2.4.11 The list of machines and mechanisms recommended for the surface treatment device is given in Appendix D.
9.2.4.12 It is not allowed to use sand spreading equipment to distribute crushed stone.
9.2.4.13 The main pouring of organic binder and distribution of crushed stone is carried out along one traffic lane without gaps or breaks. The length of the gripper for crushed stone spreaders with separate distribution of materials is determined from the condition of ensuring continuous distribution of crushed stone and the movement of the crushed stone spreader behind the asphalt distributor with an interval of 10 to 15 m. The calculation of the gripper length and the operating speed of the asphalt spreader, which is not equipped with an automatic binder consumption control system, is given in Appendix E.
9.2.4.14 The length of the grip using special machines for the synchronous distribution of binder and crushed stone is determined depending on the capacity of the crushed stone distributor.
9.2.4.15 The filling temperature for bitumen grades BND and BD should be from 140 o C to 160 o C. The filling temperature of bitumen emulsion is from 60 o C to 85 o C. The maximum filling temperature is taken when the coating temperature is below 30 o C.
9.2.4.16 The filling temperature of modified cementitious materials should be taken in accordance with technical regulatory legal acts on them. For BMP brand bitumen, the filling temperature should be from 150 o C to 175 o C.
9.2.4.17 A dry coating at a temperature of more than 30 o C is moistened with water at a flow rate of 0.5 to 0.8 l/m 2 20-30 minutes before pouring the bitumen emulsion.
9.2.4.18 Scattering of crushed stone is carried out in a layer of one crushed stone following the pouring of the organic binder or synchronously with it. Areas with insufficient or no crushed stone after mechanical spreading prior to compaction must be filled by hand.
9.2.4.19 The second layer of double surface treatment is applied immediately after compaction of the first.
9.2.4.20 It is not allowed to overlap two adjacent strips of surface treatment in both the longitudinal and transverse directions.
9.2.4.21 To ensure the quality of the transverse joint, at the end of the previous grip, dense material (paper, roofing felt, etc.) with a width of at least 0.5 m is laid across the road surface to the full width of the distribution ramp of the asphalt distributor, sprinkled along the edges with crushed stone and removed after passing the crushed stone distributor.
9.2.4.22 In the area of the longitudinal joint, loose crushed stone must be removed before the binder is distributed over the adjacent strip. When constructing an adjacent strip, the binder is distributed overlapping, and the crushed stone is distributed end-to-end. To ensure the quality of the longitudinal joint device The distribution of the binder on the side of the joint is carried out wider than the distribution of crushed stone by closing the outer flap of the crushed stone distributor.
9.2.4.23 The construction of longitudinal joints along the run-up lanes of moving vehicles is not allowed. At the end of the working day, surface treatment should be carried out across the entire width of the carriageway (for two- and three-lane roads) or across the entire width of one direction of travel (for four-lane or more) and completed with a single transverse joint.
9.2.4.24 Compaction is carried out by two self-propelled rollers on pneumatic tires. The number of passes along one track is at least 5. The compaction speed for the first three passes is up to 3 km/h, for subsequent passes – up to 10 km/h.
When using bitumen emulsion, it is allowed to compact with one roller.
9.2.4.25 Compaction begins immediately after the passage of the crushed stone distributor. When using bitumen emulsion, compaction is completed after the emulsion breaks down, characterized by a change in color from brown to black and the release of water.
Double surface treatment is compacted layer by layer.
9.2.4.26 During the first 10 days of surface treatment formation, the following conditions must be ensured:
– limiting vehicle speed to 40 km/h;
– regulation of vehicle traffic along lanes (for multi-lane roads);
– sweeping loose crushed stone onto the side of the road with mechanized brushes (the first sweeping – no later than one day after the opening of traffic).
9.2.4.27 During the warranty period the following conditions must be met:
– timely repair of defective areas in accordance with STB 1291 (if necessary);
– at a coating temperature of more than 35 o C and the presence of exudation of the binder – distribution of a fraction of 2.5-5 mm over the surface treatment layer of crushed stone at a consumption rate of 2 to 4 kg/m 2.
Protective layers can be considered at the same time as wear layers, in which case their thickness is calculated for the service life of the coating. Such layers, which have the purpose of protective and wear layers, are built on all lightweight coatings. These coverings (see Chapter 3) are built mainly from crushed stone and gravel materials, which after laying and compaction still have a residual porosity of about 20...25%.
In winter, the freezing of water in the voids of the coating and in the pores of the mineral material causes their premature destruction. Therefore, after completion of the construction of the coating, a protective layer is immediately laid. This layer, both as a protective layer and as a wear layer that determines the service life of the coating before its renewal, has sufficient thickness for wear, water resistance and roughness.
On transitional type coatings of crushed stone, gravel and especially cement-soil, which do not have wear resistance, protective layers and wear layers are laid using organic binders. Such layers can be considered independent thin-layer coatings, since they will have increased technical and operational performance compared to the coating on which it is laid.
Protective layers and wear layers combine common methods of work: surface treatment by pouring, layer laying ready mixture, embedding of crushed stone.
4.1. Device for surface treatment using watering method
Surface treatment can be single or double. The total thickness of the structural layers of surface treatment ranges from 1.0 to 4.0 cm.
Purpose of surface treatment on transitional type coatings:
improves sanitary and hygienic conditions;
strengthens the pavement structure.
On lightweight surfaces:
strengthens the pavement structure;
improves technical and operational qualities;
makes the coating more waterproof.
On capital coatings:
increases roughness;
protects the coating from wear;
creates a waterproof layer.
Surface treatment is carried out using the most durable, wear-resistant, low-grinding, water- and frost-resistant materials. Requirements for crushed stone for surface treatments (Table 4.1).
Table 4.1
Requirements for crushed stone for surface treatments
Climatic conditions | |||
in terms of strength |
by frost resistance |
||
Moderate Moderate Moderate |
Table 4.2
Cementing materials for surface treatments and impregnations
Table 4.3
Consumption of materials for surface treatments
Type of processing |
Layer thickness, cm |
Crushed stone fractions, mm |
Bottling number |
Consumption of crushed stone, m 3 /100 m 2 |
Bitumen consumption, |
Single | |||||
Notes. 1. Consumption rates are given for petroleum bitumen. When using bitumen emulsions, the consumption in terms of bitumen is reduced by 30...35%; when using black crushed stone for processing, which is always preferable, the bitumen consumption is reduced by 30...40%; to obtain greater roughness during heavy traffic, the bitumen consumption is reduced by 40...50 % against the norms given in the table.
When applying surface treatments, thoroughly clean the surface to be treated with mechanical brushes, perform patching and prime the surface. The list of operations for the surface treatment device is given in Table 4.4.
Surface treatment is a technological process of installing thin layers on road surfaces in order to ensure roughness, water resistance, wear resistance and density of the coatings. The layer arranged in this way is also called surface treatment
Surface treatments are used:
- or as a preventive layer that covers and protects the main structural layers of road surfaces from premature destruction in bad weather;
- or as a wear layer, subject to abrasion during movement, protecting the road structure in the best possible way. Such a layer requires only periodic updating to give the road structure its original qualities;
- or as the top layer of a road surface with roughness characteristics that provide traction and good drainage of surface water, leading to a significant decrease in the threshold for aquaplaning and creating, due to the increased specific pressure, good resistance to the formation of ice.
In addition to technical advantages, surface treatments have a fairly competitive cost compared to the complex of upper layers of road pavements used in these cases.
There are many different methods for applying surface treatments, of which only one is discussed in this article - the use of fractional crushed stone and various organic binders, including emulsified ones, for this purpose.
In order to create a surface treatment that meets the presented requirements, it is necessary to observe several fundamental principles when designing it:
- use a binder that bonds firmly and permanently to the surface of the coating or base. This connection is called the “binder-base” pair;
- the stone material must be attached to the covering or base, and each crushed stone must be firmly connected to its neighbors. This interaction is called the “binder – crushed stone” pair;
- the amount of binder should be sufficient to cover each crushed stone with a film to the required height and fill all microcracks in the coating, but not be excessive so as not to protrude onto the surface of the crushed stone layer. This is the basic principle of binder dosage and distribution;
- The stone material must be clean, have high physical and mechanical properties (strength, frost resistance, abrasion resistance, etc.), and have certain shapes and sizes. These are the basic requirements for stone materials;
- quantity stone material should be sufficient to create the desired surface structure, but not excessive to avoid the need to remove it. This is the principle of dosage and distribution of stone material;
- each crushed stone should take the most stable position, and all together should create a continuous monolithic layer with a rough surface. This is the basic principle of compaction.
These are the basic principles for ensuring high quality surface treatment. In addition, there are a number of additional conditions:
- All surface treatment work must be carried out in the most favorable weather conditions. This is the principle of setting deadlines for completing work;
- Before the start of work, all organizational issues regarding the supply of materials, preparation of machinery and equipment must be resolved. This is the principle of work organization;
- During the work, the requirements for the technology of work and the quality of the materials used must be strictly met. This is the principle of organizing quality control.
Surface treatments using fractionated crushed stone are carried out mainly on sections of roads with dangerous and difficult traffic conditions on roads of I – III categories.
Depending on the type and condition of the coating, surface treatments can be single or double; on cement concrete pavements - only double ones.
Material requirements
Crushed stone
Crushed stone of surface treatment absorbs and transmits the load from cars to the underlying layers, serves as a wear layer and provides traction between the road and the wheels of cars.
The stone material used for surface treatment must have high physical and mechanical properties, such as strength, frost resistance, resistance to impact and wear (abrasion), good adhesion strength to the binder, etc. The suitability of the rock for the binder is determined by testing in laboratory conditions for adhesion strength.
Rice. 1. The influence of the shape of crushed stones on the stability of their position
The shape of the crushed stone should be as close to cubic as possible to ensure a stable position on the surface of the coating. The ovoid shape of the rubble, the so-called “Columbus egg” shape, does not have a stable position. Flat tiles and crushed stones in the form of an elongated needle are fragile and do not fit well into the coating (Fig. 1).
Crushed stone for surface treatment must be very clean, which requires careful washing during production. The presence of clay, even in very weak proportions, is highly undesirable: clay is extremely hydrophilic, and the strong swelling that occurs in the presence of water leads to a tendency for the binder-crushed stone bond to break.
The correctly selected shape and size of crushed stones form the roughness of the surface treatment and reduce noise in the car interior when driving.
Trailed bitumen crusher distributor BShchR-375 jointly produced by Strommashina OJSC and Breining (Fayat Group), Germany
The choice of crushed stone size is important. It has been established that crushed stone sizes of the order of 10–15 and 15–20 mm cause quite high level noise in the car interior and interfere with listening to music at speeds exceeding 130 km/h. Based on this, preference is given to surface treatment using crushed stone of fractions 5–10 mm.
Another factor that must be taken into account when setting requirements for the size of crushed stone is to eliminate the possibility of breaking car windshields from crushed stones flying out from under the wheels of cars when driving at high speeds. The use of fine-grained crushed stone can almost completely solve this problem.
For surface treatment, crushed stone of grade no lower than 1200 according to GOST 8267-82 is used from hard-to-grind igneous and metamorphic rocks for roads of categories I and II, grade 1000 for roads of category III and grade no lower than 800 for roads of category IV, fractions 5 –10, 10–15, 15–20 mm (the use of crushed stone of fractions 5–15 and 10–20 mm is allowed, provided that the adhesion coefficient is ensured) predominantly cuboid-shaped grains (plate-shaped grains make up no more than 15%); the content of dusty, clayey and silty particles in crushed stone should not exceed 1% of the mass. The choice of crushed stone fraction is made depending on the hardness of the road surface.
Astringent
When applying surface treatment, viscous bitumen, bitumen with tar additives, bitumen and tar with polymer additives, and bitumen emulsions are used as binders.
The binder provides waterproofing of the coating, gluing the stone material to the coating or base and connecting the crushed stone into a single layer.
The grade of bitumen is selected according to GOST 22245-90, taking into account the road-climatic zone: for I - BND 90/130 and BND 130/200, for II and III - BND 60/90, BND 90/130, BND 130/200, BN 60 /90, BN 90/130 and BN 130/200, for IV and V - BND 60/90, BND 90/130, BN 60/90 and BN 90/130.
The bitumen must withstand the adhesion test to the crushed stone used for the surface treatment device. If the adhesion of bitumen to crushed stone is unsatisfactory, additives of appropriate surfactants should be used or crushed stone should be pre-treated with tar or a mixture of bitumen and tar.
The coal tars used must be grade D-5, D-6 or D-7 in accordance with GOST 4641-80 and used on roads no higher than category III. On sections of roads passing along settlements, the use of coal tars is not permitted.
When applying surface treatment using emulsions, predominantly cationic bitumen emulsions of the EBK-1, EBK-2 classes are used, which meet the requirements of GOST 52128. In conditions of III – IV road-climatic zones and under favorable weather conditions in zone II, the use of anionic emulsions of the EBA- class is allowed. 1, EBA-2. Emulsions must withstand the adhesion test of the binder film to crushed stone.
When performing surface treatment on cationic bitumen emulsions, crushed stone untreated with an organic binder is used; on anionic emulsions, predominantly black crushed stone is used.
When constructing surface treatment on roads with a traffic intensity of over 3000 vehicles/day, with the traffic of mainly trucks, also in areas with a sharply continental climate, bitumen and tar with polymer additives are used. Tar-polymer binder is used on roads no higher than category II.
There are several types of surface treatments, each of which has its own area of most effective application(Fig. 2).
Rice. 2. Types of surface treatments
- Single-layer surface treatment with single distribution of binder and crushed stone. It is used to create a rough surface and a wear layer for road pavements with sufficient strength. This is the most common type of rough surface treatment and is most suitable for all types of traffic. Most often it is made from crushed stone of fractions 5–10 mm.
- Single-layer surface treatment with double distribution of crushed stone. A large fraction of crushed stone (for example, 10–15 or 15–20 mm) is first scattered onto the layer of applied binder, rolled with a roller, and then a smaller fraction of crushed stone (for example, 5–10 mm) is scattered and compacted. Used on roads with heavy traffic and high speeds. This surface treatment improves the tightness of the coating, eliminates minor irregularities and deformations, and better distributes the forces from the wheels of cars. This treatment works especially effectively on a good, hard base.
- Double layer surface treatment. A coarse fraction of crushed stone is scattered onto the first layer of spilled binder and compacted. Then the second layer of binder is poured, a finer fraction of crushed stone is scattered and finally compacted. It is used on coatings with insufficient strength, in the presence of a network of cracks, pitting, ruts, and with high traffic intensity, i.e. in cases where it is necessary not only to create a rough wear layer and a protective layer, but also to improve evenness, slightly increase strength and shear resistance. Also used on cement concrete pavements.
- Sandwich surface treatment. Crushed stone of a larger fraction is scattered onto the coating, then the binder is distributed, crushed stone of a fine fraction is scattered and compacted. The structure of the resulting surface treatment layer is comparable to a single-layer surface treatment arranged by pouring binder and double scattering of crushed stone. This surface treatment is recommended for non-uniform coatings to level it out and strengthen it somewhat. Used on roads of secondary, local importance.
When choosing a method for surface treatment of coatings, it is necessary to take into account its purpose, traffic conditions on the road, climatic conditions of the construction area, the hardness of the road surface, the availability of materials and mechanization equipment.
Work technology
There are two ways to apply surface treatments:
- traditional - with separate distribution materials;
- method with synchronous distribution of binder and crushed stone.
Traditional way
Work on installing a single surface treatment using the traditional method using bitumen, tar bitumen, bitumen and tar polymer binders is carried out in the following order:
- bottling of binder;
- crushed stone distribution;
- rolling;
- care during the formation period.
Work on the installation of double surface treatment is carried out in the following sequence:
- surface preparation (cleaning from dust and dirt) and repair work;
- first filling of binder;
- first scattering of rubble;
- rolling;
- second filling of binder;
- second scattering of crushed stone (a break of no more than 3–5 days is allowed between the first and second scattering of crushed stone);
- rolling;
- care during the formation period.
The coating is cleaned of dust and dirt using mechanical brushes; the most contaminated areas are washed using a watering machine.
Brush strings, whatever their nature (nylon, steel), must be in good condition and sufficiently rigid to ensure effective scraping.
In cases where the old coating cannot be completely cleaned of dust and dirt remaining in small cracks and depressions, it must be primed by pouring liquid bitumen at a rate of 0.3–0.5 l/m2 or bitumen emulsion at a rate of 0.5 –0.8 l/m2.
The binder is poured using an asphalt distributor. For uniform filling of the binder, it is necessary to ensure uninterrupted operation of the nozzles, uniform operation of the pump and the required speed of movement of the asphalt distributor.
The nozzles must be thermally insulated and equipped with a heating device that allows them to maintain or provide a certain temperature of the binder.
Depending on the selected binder and the width of the treated surface, the driver determines, using the asphalt distributor adjustment elements (nomogram, computer disk, programming), the required ratio between the speed of movement and the number of revolutions of the pump, which determines the dosage of the binder on the coating. During distribution, the ratio between the vehicle speed and the number of pump revolutions is maintained constant, either by automatic tracking or by the driver directly reading the tachometer and revolution counter.
During bottling, the temperature of bitumen grades BND 60/90, BND 90/130, BN 60/90 and BN 90/130 should be 150–160° C; grades BND 130/200 and BN 130/200 – 100–130° C; temperature of polymer-bitumen binder – 140–160° C; tar-polymer binder – 100–110° C.
The distribution of crushed stone is carried out using a self-propelled crushed stone distributor, a dump truck with an attachment or another mechanism that ensures quick and uniform distribution of crushed stone. The body of all these mechanisms must be flat and without local deformations. The height of crushed stone discharge should be small to ensure a more uniform distribution of aggregate on the pavement. Automatic chip spreaders can be equipped with a hydraulic expansion system, which allows you to change the working width from 2.50 to 4 m without stopping.
Crushed stone is distributed immediately after pouring the binder into one layer of crushed stone and rolled with a 6–8 t roller in 4–5 passes along one track.
Compaction of the surface treatment of coatings ensures the laying of crushed stone and its fastening to the coating. Pneumatic tire seals provide these functions perfectly. They adapt to road unevenness and do not crush crushed stone.
During the first days of operation, it is necessary to take care of the developing layers. Loose crushed stone must be removed from the surface no later than 1 day after the opening of traffic. The speed of vehicles is limited to 40 km/h and adjusted according to the width of the roadway.
The discarded excess crushed stone is picked up by cleaning collection machines, cleaning machines and retracting machines. Equipped with a variety of brushes and suction nozzles, they are equipped with collection containers for the fine material they lift. These suction mechanisms represent a major advance in surface coating technology, as they can significantly reduce the biggest pollution hazard: the breaking of car windshields once driving resumes.
Surface treatment using bitumen emulsions is carried out in the following order:
- preparing the surface (cleaning it from dust and dirt) and performing repair work if necessary;
- wetting the surface with water (in hot, dry weather);
- pouring the emulsion over the coating in an amount of 30% of the norm;
- distribution of crushed stone in an amount of 70% of the norm;
- bottling the remaining emulsion (70%);
- distribution of the remaining crushed stone (30%);
- rolling;
- care during the formation period.
The temperature and concentration of the emulsion are set depending on weather conditions. At air temperatures below 20° C, it is recommended to use an emulsion with a temperature of 40–50° C and a bitumen concentration of 55–60%. The emulsion should be heated to the specified temperature directly in the asphalt distributor during transportation to the work site. At air temperatures above 20° C, the emulsion is used cold, and the bitumen concentration can be reduced to 50%.
The distribution of crushed stone is carried out in such a way that the crushed stone is distributed no further than 20 m from the asphalt distributor pouring the emulsion.
Maintenance of surface treatment using bitumen emulsions is carried out in the same way as when using bitumen. When using anionic emulsions, vehicle traffic is opened no earlier than 1 day after completion of work.
Surface treatment technology with synchronous distribution of binder and crushed stone
The main difference new technology surface treatment device is a synchronous, almost simultaneous distribution of binder and crushed stone scattering (Fig. 3).
Rice. 3. Surface treatment with synchronous distribution of materials
When applying surface treatment using traditional methods, the time gap between the distribution of the binder and the scattering of crushed stone is limited by the cooling time of hot bitumen and can reach 1 hour.
With the synchronous distribution of binder and crushed stone, the gap between these operations does not exceed 1 second, which significantly affects the improvement of the quality of surface treatment, both when using hot bitumen and bitumen emulsion as a binder.
The increase in quality when using hot bitumen as a binder is explained by the fact that in such a short period of time the bitumen does not have time to cool down and retains a liquid consistency and high adhesive ability. As a result, bitumen penetrates well into the micropores of crushed stone and coating, envelops each crushed stone and firmly glues them to the coating and one to another.
Compaction of the laid layer also occurs when the bitumen is hot, which ensures maximum compaction effect.
When using bitumen emulsion as a binder, the high quality of surface treatment with synchronous distribution of binder and crushed stone is explained by the fact that in such a short period of time the decomposition of the emulsion will only begin, and the emulsion in a liquid state will fill all the micropores of the crushed stone and coating, cover each crushed stone with a thin layer of binder and will provide the possibility of good compaction of the surface treatment layer.
Synchronous distribution solves all the problems of organizing and coordinating work that arise during asynchronous distribution, since with each stop in the distribution of crushed stone, the distribution of the binder automatically stops. Downtime due to climatic conditions is significantly reduced and work productivity increases. This is important when using high viscosity binders, but is especially important when working in adverse weather conditions.
The synchronous distribution of the binder and crushed stone has a beneficial effect on the formation of a interface between the binder and crushed stone, which guarantees high performance characteristics of surface treatment, reduces the risk of work failure due to the difference in temperatures of the base and binder, as well as due to the presence of dry fine fractions when applying surface treatments with using emulsions.
Experience shows that a high level of quality of surface treatment with synchronous distribution of binder and crushed stone makes it possible to achieve amazing results when a thin layer of crushed stone and binder withstands the intense impact of car wheels for 10–15 years.
Thus, the synchronous distribution of binder and crushed stone with a delay time of 1 second is the most important innovation in surface treatment practice in the last 20 years.
To implement the idea of surface treatment with synchronous distribution of binder and crushed stone, SECMAIR has developed and produces a wide range of bitumen crushed stone distributors of various capacities, as well as other machines for the maintenance and repair of road surfaces using crushed stone treated with bitumen or bitumen emulsion.
Manufactured vehicles can operate when moving forward or when moving in reverse (Fig. 4).
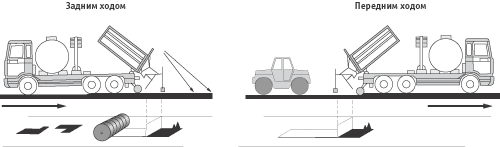
Rice. 4. Operating principles of surface treatment machines
Taking into account the significant interest of Russian road workers in the introduction of surface treatment technology with synchronous distribution of binder and bitumen, the French company SECMAIR and the State Unitary Enterprise Saratov Research and Production Center "Rosdortech" created a joint production of Chipsealer type machines in Saratov.
In 1999, production of the following machines began:
- Chipsealer-40. This is high-performance equipment designed for rough surface treatments in large volumes. Chipsealer-40 equipment is mounted on a Caizer semi-trailer and has a completely autonomous power supply system. In one cycle of loading the body with crushed stone, it allows surface treatment on a strip 3.75 m wide and up to 800 m long in 10 minutes.
- Chipsealer-26 made on the basis of the Russian semi-trailer SZAP - 9905. MAZ and KamAZ truck tractors can be used as a tractor vehicle. It has the same characteristics as Chipsealer-40, but the dimensions of the body for crushed stone and the reservoir for binder are smaller.
- Chipsealer-19– designed for repairing road surfaces and installing rough surface treatments in small quantities.
Stopper type machines
Used to control coating erosion on early stage by installing local surface treatment in areas of peeling and chipping of the coating, the appearance of small cracks, a network of cracks, small potholes and ruts. The machine has on one chassis a container for binder, a body for crushed stone, a grab bucket for loading crushed stone into the body and distribution devices for applying bitumen and crushed stone (Fig. 5).
Another difference is that the “Stopper” has a compacting block of 8 pneumatic smooth wheels, which, using 4 hydraulic jacks, are lowered to the surface into the working position and raised up to the transport position. This is especially important for the accelerated formation of the repair layer in cold and humid climates. In dry and hot climates, this formation occurs under the influence of moving vehicles, and there is no need for a compaction block. In addition, “Stoppers” are adapted for local repairs using surface treatment.
Surface Treatment Machines
For a surface treatment device in the traditional way, i.e. with separate distribution of binder and crushed stone, asphalt distributors and crushed stone distributors are used.
Asphalt distributors are distinguished and selected by:
- tank capacity (carrying capacity);
- width of binder distribution; in this case, as a rule, the distribution width is chosen equal to the width of the road lane or 5–10 cm smaller.
Crushed stone distributors are distinguished by:
- capacity (capacity) of the bunker for crushed stone;
- width of crushed stone distribution; in this case, as a rule, the width of the distribution of crushed stone is taken equal to the width of the distribution of the binder;
- type of travel (movement): trailed and mounted base machines. As a rule, dump trucks are used as base machines for trailed and mounted crushed stone spreaders.
For surface treatment using the method of synchronous (simultaneous sequential) distribution of binder and crushed stone, bitumen (emulsion) crushed stone distributors are used.
Bitumen crushed stone distributors are distinguished by:
- processing width, i.e. according to the correspondence (multiplicity) of this parameter to the width of the carriageway of the road;
- capacity (capacity) of the binder tank and crushed stone bunker;
- crushed stone loading method, i.e. the use of special loading machines for loading crushed stone into a bunker or special self-loading equipment.
In Fig. Figure 6 shows production graphs (in thousand m2) of all three types of machines: asphalt distributors, crushed stone distributors and bitumen-(emulsion)-crushed stone distributors at a bitumen emulsion filling rate of 1.4 and 2.1 l/m2 and a crushed stone distribution rate of 10.0 and 15.0 kg/m2. Depending on the width of the binder pouring and the distribution of crushed stone in Fig. 6 also shows production in linear terms. m processing strip.
The presented graphs, taking into account the capacity of the binder tank and the crushed stone hopper and bitumen crushed stone distributors, show that the capacity of the binder tank provides significantly greater production than the capacity of the crushed stone hopper. Thus, the crushed stone hopper must be filled several times to ensure the production of binder. The ratio of production of binder and crushed stone for various bitumen and crushed stone distributors ranges from 2.0 to 9.5. Therefore, the method of loading crushed stone has a significant impact on shift production (productivity).
Joint operation of an asphalt spreader and a trailed crushed stone spreader of Becema JSC, loaded from a dump truck
When loading crushed stone into the crushed stone distributor hopper (without self-loading) at the base using a single-bucket front loader or a crane with a grab (jaw bucket), i.e. with a double mileage from the place of work to the base and back, the time required for one load ranges from 40 minutes to 1 hour 20 minutes.
When loading crushed stone into the hopper of a bitumen crusher distributor at the work site using self-loading or using a dump truck with a crane equipped with a grab, the time required for one load is from 10 to 15 minutes.
When loading crushed stone into the hopper of a bitumen crushed stone distributor with self-loading from a receiving hopper located at the rear of the machine and loaded from a dump truck, even when the bitumen crushed stone distributor is stopped, the time required for one load ranges from 2 to 6 minutes.
When calculating, the loading of the binder is combined with the loading of crushed stone, i.e. is carried out after two to nine loadings of crushed stone, the speed of movement of the bitumen crushed stone distributor is taken equal to 4 km/h = 1.1 m/sec = 66 m/min., the distribution width is taken to be 3 m, the time utilization factor is taken to be 0.8 (when loading at the base) and 0.6 (when loading on the road), which is associated with the need and great complexity of the rhythmic supply of materials, the use of additional machines (dump trucks, bitumen trucks).
Surface treatment consists of pouring a thin layer of hot bitumen onto a rolled and prepared road surface, cleared of dust, and spreading fine stones (or coarse sand) over it.
The thickness of a single surface treatment is 1-1.5 and double 2.5-4 cm. An even waterproof layer is created on the road surface with sufficient wear resistance and a rough surface that provides a good braking effect. For surface treatment, viscous bitumen BND 130/200 and BND 200/300, having an operating temperature of 90-150° C, and liquid bitumen MG 130/200 and SG 130/200, heated to a temperature of 80-100° C, are used.
The production technology of a single surface treatment includes the following operations: preparing the coating surface for surface treatment (repair, correction of the transverse profile and cleaning the surface from dirt and dust); preliminary pouring of liquid binder (0.5 -0.8 l/m2) onto a coating constructed without the use of black binders; the main pouring of the binder over the surface of the coating with a bitumen (tar) consumption of 0.7-2.4 l/m 2 ; scattering mineral materials 3-15 mm in size into the spilled layer of hot bitumen (fine crushed stone, gravel, coarse sand); rolling out the surface treatment layer.
Coatings on which surface treatment is intended should not have transverse slopes exceeding 30‰. If the slope is greater, they must be softened using, for example, a mixture of sand and bitumen. Before surface treatment, coatings should be cleaned with mechanical brushes, sweepers or watering and washing machines (2-3 passes). Coverings made from reinforced soils are cleared of lumps and layers of dried mud by passing light graders, while metal brushes should be used very carefully so as not to damage the top layer of the reinforced soil.
The surface and seams of pavements require especially thorough cleaning. On the surface of coatings constructed without black binder (in particular, gravel), a certain amount of dusty particles almost always remains, which can cause the surface treatment to peel off from the coating. To avoid this, you should create a contact layer in the form of preliminary pouring, which, if possible, is best done 1-2 days before the main work. In this case, liquid bitumen can be used without heating in warm weather.
Binders are usually poured using an asphalt distributor. Before bottling, they are heated to the operating temperature indicated above. 20-30 minutes after pouring, a layer of liquid bitumen or tar should be covered with mineral material, which is best used as crushed stone from hard rocks; worse - gravel and coarse sand.
In the conditions of forestry enterprises (lespromkhozes), it is necessary to use any durable material, including crushed blast furnace slag. The largest particle size should not exceed the thickness of the binder layer by more than 5 mm. If it rains or gets cold immediately after rolling the wear layer, the area should be closed to traffic until it dries completely and then rolls. For better adhesion of bitumen to the mineral filler, 1-3% slaked lime should be added. It is convenient to spread the mineral material using mounted distributors for dump trucks or mineral fertilizer distributors available in state farms, collective farms and departments of Agricultural Equipment.
The vehicle containing the mineral material must be driven in reverse with the wheels on the scattered layer of fine stones. Immediately after the distribution of the mineral material (before the binder hardens), rolling begins. Typically, fairly heavy rollers are used (5-8 tons), but they should not crush pieces of mineral material; When using weak materials, rolling should be done with lighter rollers. Good results obtained when working with pneumatic rollers (of any weight). The final rolling and formation of the surface treatment layer is carried out under the influence of moving machines for about a month. With double surface treatment, after rolling the 1st layer, all other operations are repeated.
If you find an error, please highlight a piece of text and click Ctrl+Enter.
Page 42 of 52
11. DEVICE FOR SURFACE TREATMENT OF COATINGS
11.1. Work on surface treatment of coatings should be carried out at an air temperature of at least 15°C. When using a cationic emulsion for surface treatment, at an air temperature of at least 5°C.
SURFACE TREATMENT DEVICE
USING FRACTIONED CRUSHED STONE
11.2. When constructing surface treatment, crushed stone of grade no lower than 1200 should be used from hard-to-grind igneous and metamorphic rocks of fractions 5-10, 10-15 or 15-20 mm with predominantly cubic grain shapes. Crushed stone must be clean, free of dust and clay.
11.3. When installing surface treatment using bitumen, bitumen of the BND 60/90, BND 90/130, BND 130/200, BN 60/90, BN 90/130 or BN 130/200 grades should be used as a binder.
Bitumen must withstand the adhesion test with crushed stone that will be used for the surface treatment device. If the adhesion of bitumen to crushed stone is unsatisfactory, additives of appropriate surfactants should be used, as well as pre-treatment of crushed stone with bitumen.
When constructing surface treatment on road sections with difficult and dangerous traffic conditions, as well as in areas with a sharply continental climate, bitumen with additives of thermoplastic elastomer polymers should be used.
11.4. The consumption of binder and crushed stone must comply with the standards established in the table. 15.
Table 15
Consumption rate |
||||
Crushed stone size, mm | crushed stone, m 3 /100 m 2 | bitumen, l/m 2 | emulsions, l/m 2, at bitumen concentration, % |
|
Single surface treatment |
||||
Double surface treatment |
||||
First placer | First bottling | |||
Second placer | Second bottling | |||
Note. When using black crushed stone, binder consumption rates are reduced by 20-25%.
11.5. Work on the surface treatment device should be carried out on a clean, dust-free surface to be treated, dry when using bitumen and moistened (0.5 l/m2) when using bitumen emulsions.
11.6. The bitumen temperature during filling should be: for brands BND 60/90, BND 90/130, BN 60/90, BN 90/130 - 130 - 160 -C; for brands BND 130/200 and BN 130/200 -100 - 130 °C.
Crushed stone should be distributed mechanically immediately after pouring the bitumen in a layer into one crushed stone and rolled with a roller in 4-5 passes along one track.
During the first 2 - 3 days of operation, it is necessary to limit the speed of vehicles to 40 km/h and adjust it according to the width of the roadway. Loose crushed stone must be removed from the surface.
11.7. When applying surface treatment using bitumen emulsions, predominantly cationic emulsions EBK-1, EBK-2 and anionic emulsions EBA-1, EBA-2 should be used.
Emulsions must pass the test for adhesion of the binder film to crushed stone according to GOST 18659-01.
When applying surface treatment using cationic bitumen emulsions, crushed stone should be used that has not been pre-treated with organic binders; when using anionic emulsions, predominantly black crushed stone should be used.
11.8. Surface treatment using bitumen emulsions should be carried out in the following order:
pouring emulsion over the coating in an amount of 30 % norms;
distribution of crushed stone in an amount of 70% of the norm;
bottling the remaining amount of emulsion;
distribution of the remaining amount of crushed stone;
11.9. At air temperatures below 20 °C, emulsions with a bitumen concentration of 55-60% and a temperature of 40-50 °C should be used. At air temperatures above 20 °C, the emulsion should not be heated, and the bitumen concentration can be reduced to 50%.
Distribution and rolling of crushed stone should be carried out in accordance with clause 11.6. Rolling should be carried out until the emulsion completely disintegrates. When using anionic emulsions, vehicle traffic in accordance with the requirements of clause 11.6 is allowed to open no earlier than 24 hours after the completion of work.
Content |
---|