Frame-panel houses. How to choose a wooden house yourself
When deciding to build a private house and facing a choice between timber or a frame with panels, the future owner experiences difficulties. There are many advantages in favor of one or the other object, but their disadvantages are also quite serious, and therefore it is possible to give preference to any of the objects only after a detailed study of each. Below we describe in detail each parameter of the finished structure.
Frame-panel construction - advantages and disadvantages
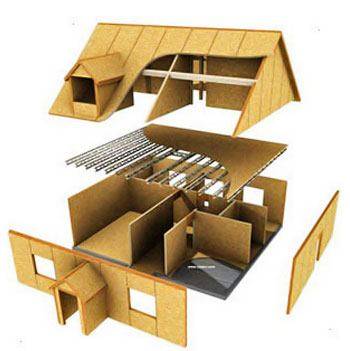
The technology for constructing such houses is relatively new and has already received recognition in terms of construction time - indeed, you can finish your own house just a few months from the start of the project idea. What else is attractive about such objects:
- The cost of a building produced according to frame technology using panels lower than timber panels of the same configuration and number of floors. This is important for young families who do not have a large budget for solid wood construction.
- Such objects are more protected from fire than profiled timber. It's all about less wood throughout the entire object and a large number of impregnations.
- Shield objects are warm. This is due to the fact that polyurethane insulation is pre-laid inside the walls, which does not allow heat to freely leave the home.
- Even voluminous panel houses made of timber do not require a solid foundation - a slab or a monolithic strip. The structure is lightweight compared to a solid wood object.
- You can finish and insert windows and doors immediately after making the frame - the house does not shrink, so the double-glazed windows and door panels will not be squeezed out and they will not break under the weight.
- Construction can be carried out at any time of the year, not excluding autumn or spring.
- The durability of panel structures can reach 70 years or more.
And now about the shortcomings that will make future owners think about the feasibility of such construction:
To this we can add that due to the good heat capacity of the house, rodents can live in the walls. They will use insulation for their nests, and owners may end up with, in addition to unwanted neighbors, cold corners and a weak structure in general. And now, in order to understand which is better: a panel house or a house made of timber, you need to analyze the advantages and disadvantages of profiled or glued raw materials.
Log houses - advantages and disadvantages
Solid wood is a building ecology. A house made of timber and a panel building are fundamentally different in this regard.
Owners of future massif buildings do this consciously and put this parameter at the forefront when leaving for permanent residence from stuffy concrete boxes. What other advantages does this object have:
About the disadvantages:
When deciding to use wood, the future homeowner must understand the truth - he is agreeing to build an object from the most capricious type of raw material.
The lightness and lack of ecology in frame objects deprives the structure of the idea of a home - a durable structure with a pleasant pine smell, where more than one generation will grow up. Therefore, if there is an opportunity to delay construction and increase capital, then this should definitely be done.
- Page 2
We build turnkey panel country houses
In construction, there are many options for low-rise buildings, which are developed using the latest technologies. Thus, panel house projects have become popular, which are not only quickly erected, but also developed without problems by specialist designers. The future of suburban construction lies in frame technology.
If you want to live in a house that will fully meet all individual requirements, then you should leave the purchase of a ready-made object aside and pay attention to projects of one-story panel houses. Many people turn to professional architects and builders for promising turnkey projects of cottage or country houses.
It is quite possible to get a ready-made house inexpensively if you contact latest technology, which has gained popularity among our foreign neighbors. Cottages and country houses, built using technology frame construction not only high-quality and rational, but also economical. In winter, such a house is warm, cozy and no less comfortable than in an ordinary brick house.
Panel houses for permanent residence (permanent residence)
If a person wants to save money, he can study prices for country houses according to the usual method of construction and using frame technology - the difference is noticeable even to an unprofessional eye. Thanks to the foreign method, it is possible to build not only panel country houses, but also frame cottages.
Reasonable ratios speak for themselves: one cubic meter frame wall 1.7 times cheaper compared to foam concrete blocks, 1.3 times cheaper than timber walls, 2.2 times cheaper than brick walls taking into account identical indicators.
In terms of comfort and warmth, panel buildings are also several times superior, and their beauty and uniqueness of structures can be appreciated at different photos. It is convenient to build such houses on any terrain and on soil with different indicators - this indicator is no less important than the efficiency indicators.
Therefore, if you are looking for an economical way to get cozy housing outside the city in a short construction period, then you should think about panel house construction. Regardless of the architectural complexity, projects of such houses are developed promptly, taking into account all the necessary criteria. From an environmental point of view, a panel house will be complete, because most of them are built using breathable materials.
You can buy an economy class prefabricated panel house from us
The construction estimate is influenced by many factors: there is no need to build an expensive foundation, conduct engineering surveys at the construction site to study the soil, etc. Interior finishing can begin immediately after installing the panel structure. In a short time and for little money, a beautiful, cozy house appears before your eyes, meeting all the necessary individual characteristics.
Modern houses, built using foreign technology, comply with all construction standards, so you can live in them year-round with the whole family or come on vacation whenever you wish. A wide variety of materials can be used for exterior cladding of a house. construction products, but if the facade is entirely made of wood or other material, then there is no need for additional cladding.
Regardless of the height of the panel house and its other aesthetic characteristics, projects are developed quickly, for which specially designed computer programs are used. For such housing, the owner will be able to pay a little money, but will receive a unique house design, which is incomparable with nearby cottages.
Owning your own home, reliable and cozy, is a real dream. But most people start a grandiose construction project, which will take a lot of time and require large financial investments. So how can you become the owner of your own home or cottage? There is a way out - frame-panel houses, which you can easily build with your own hands, with minimal investment funds.
This type of house is very popular in the West; buildings are erected in a few weeks and are durable, reliable and visually attractive. In this article you can learn how to choose a place, start construction correctly and what materials are needed to build your own frame and panel house.
Before construction work, it is necessary to choose the right location for the house. Since a large number of building elements made of wood are used, you should not place the building on too wet and swampy soil. Despite the strength of the structure, all parts and elements will be exposed to moisture over time, which will deteriorate their condition and appearance.
It is forbidden for old and spreading trees to grow near the house. Their roots can damage a lightweight foundation, causing the structure to tilt or shrink over time.
It is advisable to build the house on a hill. Before starting work, you need to check the soil for the presence of groundwater. They can cause destruction and deformation of a building due to the instability of the soil above them.
Types of foundation for frame-panel houses
Since the structure of the building is light, there is no need to pour a large foundation. There are three types of supports you can use for your home.
Strip foundation, not deeply buried in the ground.
Screw piles.
Screw piles
Screw support for home- This is one of the simplest types of foundation. It is quite difficult to make screw posts with your own hands, so building elements are purchased in specialized stores. The finished piles look like hollow metal pipes of different diameters and lengths with a pointed screw at the end. You can install piles using special equipment or on your own. The number of piles depends on the size and area of the house.
Piles can be driven into any soil, and seasonality does not affect the work technology. A pile screwed in at an angle cannot be removed. It's better to leave it in the ground. A twisted pile will not perform its functions and after the foundation is erected it may skew to the side.
To create a columnar foundation, asbestos-cement pillars are purchased, which are dug a meter into the ground. Cement is poured into the middle of the posts, which strengthens their structure. The more columns, the more stable the foundation of the house is.
Strip foundation
Strip foundation - construction procedure
Creating this support requires the presence of cement and the manufacture of formwork to pour the structure. Since the house is lightweight, the foundation can be poured shallowly.
Materials for the construction of frame-panel houses
A beam having dimensions of at least 150 by 150 mm. With its help, horizontal lintels and vertical posts are erected in the building.
Board or plywood for covering the frame.
Insulation material.
Roofing felt, with the help of which waterproofing is carried out between the embedded beam and the foundation.
Polyurethane foam.
Fastening materials: nails, anchors, screws.
First of all, the room is waterproofed. To do this, roofing material is laid in several layers on the foundation support pillars. The layers are held together with bitumen mastic. Then the lags are laid.
The beam, which will act as a log, is laid with its ends on the base of the foundation. The middle of the logs should lie on the fundamental supports located inside the perimeter of the building.
The surface of the timber on which the flooring will be laid in the room must be flat. To do this, it is recommended to first run the wood through a surface planer or level out uneven areas with a chainsaw.
To keep the structure level, you need to use a level. If the joists are not at the required level, you can raise them by laying down a solid board.
Flooring
It is advisable to make the floor in the house two-level: rough and finishing. Until the walls are erected, a rough board is laid. Insulation and laying of the finished floor are carried out after the walls and roof are erected.
For the rough version of the floor, a floorboard with a thickness of at least 35 cm is required. The board is laid on logs fixed to the foundation.
Construction of a house frame
The connection of vertical and horizontal support beams in the structure of a house is carried out not only using fittings. When connecting, special grooves are cut out at the ends of the support beams, equal to half the thickness of the beam. These grooves are connected using wooden pins called dowels. A hole is drilled in the grooves, having a smaller diameter than the diameter of the dowel, so that the support elements are connected by tension.
The base of the frame must be made of 2 levels: beams along the perimeter of the foundation are stacked on top of each other. The top beam is used to attach the vertical posts of the frame. As many grooves are cut into it as there are racks in the structure of the house.
The racks are installed in grooves, fastened with dowels and additionally supported by special boards called jibs. The jibs will prevent the frame structure from skewing. After all the racks are installed, the upper joists are tied. The timbers laid on the racks must also have grooves cut into which the vertical racks are inserted. Before finally fixing the racks in the frame of the upper logs, it is advisable to make sure that the frame is built without distortions or defects.
The vertical posts are secured to the top frame of timber using long nails (hundreds of nails). The jibs are removed after the construction of the timber frame.
Then you need to attach horizontal jumpers made of timber between the vertical posts. Their connection is also carried out using cut grooves and long nails. The frame is thus further strengthened.
The sheathing of vertical posts can be done with plywood or boards. The material must be attached to the vertical and horizontal posts with a continuous shield, without gaps. Openings for windows and doors should remain free. They are formed during the process of covering the building.
Most often, a gable roof structure is used for frame-panel houses. It looks like a triangle, is easy to install, and perfectly protects the building from precipitation.
The roof installation process can be divided into three stages.

To build a roof, the following material is required.
Beams, minimum 15 by 15 cm.
Board for sheathing.
Fastening accessories.
Roofing material.
It is not recommended to use heavy materials such as clay tiles to install the roof. They significantly make the structure of the house heavier, which is very dangerous for the frame and foundation.
Installation of the roof begins with the laying of load-bearing beams, which are laid on the wall structure every 40 - 50 cm. The edges of the beams should protrude from the outer walls by at least 40 cm. This is necessary to ensure that precipitation does not fall on the walls and under the roof. A board is laid on the beams, which will become the floor of the attic. The board is attached to the beams with nails or self-tapping screws.
Then the roof truss structure is installed. Triangular pediments are installed on both sides of the house. They form the height of the roof. The tops of the gables are connected by timber. Then the rafters are attached to this beam and to the supporting upper frame. They should fit snugly against the beams and not extend beyond the structure. A frame of boards is attached to the rafters, which makes the structure more reliable and stable.
Insulation is laid on the board sheathing, and vapor barrier material and waterproofing are placed on it. The roof is installed on top of the materials. After the roof is installed, it is necessary to install a drainage and storm sewer system around the perimeter of the house, which will remove moisture from the roof, from the walls and foundation of the building.
Video - How to properly install rafters in a gable roof
Installation of doors and windows
If you plan to live in the house in the summer, then windows with one frame are sufficient. If the building will be lived in all year round, then it is worth installing double-glazed windows with several panes. This will help avoid heat loss.
Insulation of walls in a frame-panel house
After the roof of the building is ready, windows and doors are installed, it is necessary to insulate the frame of the house. Insulation can be carried out both inside the house and outside. It is optimal to use two types of insulation.
Materials for external insulation
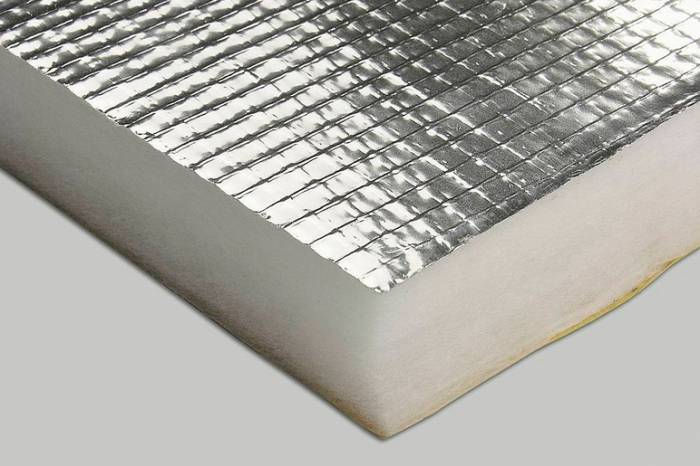
Each type of insulation has certain properties. If you plan to live in the house all year round, then you can use several types of material at the same time. For example, mineral or glass wool are placed between the vertical beams of the frame. Plywood or boards are fastened on top, polystyrene foam boards are mounted on the boards and covered with isolon. Heat loss with such insulation of the building is minimal. Isolon also protects the wooden elements of the building from moisture penetration.
Facade cladding is installed on top of the insulation. This could be siding, imitation rounded timber or other material that will decorate the facade of the house.
Materials for internal insulation of a house
Before insulating the walls inside the house, it is necessary to coat all wooden parts with special compounds that protect against rot, mold, and pests. Then you need to select the material with which the walls in the room will be lined.
Materials
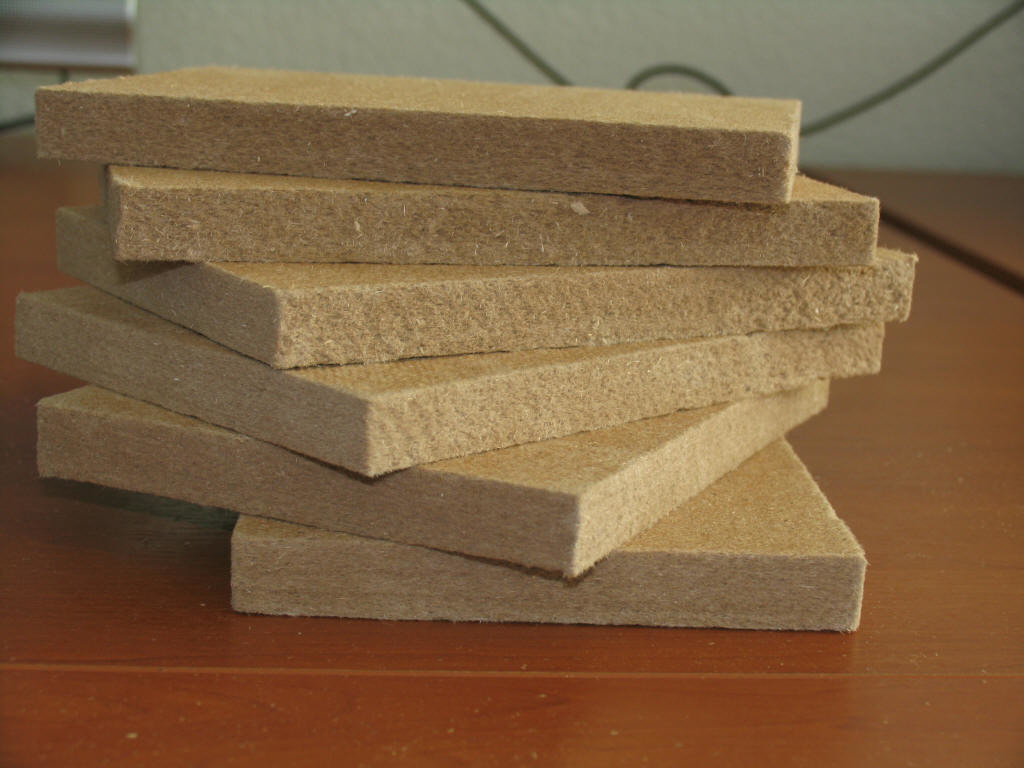
The latter type of insulation is the most convenient for installation; also, its surface does not require preliminary preparation for gluing wallpaper or applying another coating. This material can be used not only for wall cladding, but also for ceilings.
You can make frame panel houses with your own hands
Video - Do-it-yourself frame-panel house
In this article: how the fencing of a panel house is constructed; what is laminated timber and thermal timber; analysis of erroneous opinions about panel houses and houses made of timber.
How reliable and beautiful should it be, what costs are really worth incurring to create it? These two questions haunt every potential homeowner like the sword of Damocles, because newly built housing must successfully withstand the very harsh conditions of the Russian climate. Yes, somewhere out there, in the great and vast foreign countries, panel houses and those built from timber regularly serve their owners, withstanding the cold and the onslaught of various hurricanes with human names, but in Russia these same panel houses and buildings built from timber do not have the slightest chance... or is there?
Panel houses - anatomy of cladding
The main operational advantage of frame-panel houses lies in SIP panels - a kind of sandwich consisting of 12 mm OSB boards on the outside and filled with a 100-150 mm layer of insulation, usually polystyrene foam, less often basalt mat.
OSB board consists of three to four layers of wood (pine or aspen) chips, usually glued together with melamine-formaldehyde, urea-formaldehyde and urea-formaldehyde resins, which contain boric acid and synthetic wax. A number of modern manufacturers of oriented strand boards use polyisocyanate glue (MDI), which does not contain phenolic and formaldehyde resins, for gluing layers of chips. The orientation of the chips in the composition of the OSB board is different and depends on the layer in which it is located: in the inner layers the chips are oriented along the width of the board; in the outer layers - along its length. In a sandwich of SIP panels, an OSB board of at least third class is used, intended for construction load-bearing structures operating in particularly wet conditions.
It should be noted that in a number of its characteristics, OSB board is superior to many types of boards made from shavings:
- high mechanical strength, exceeding, for example, the strength properties of chipboard by 2.5 times. In terms of strength, OSB boards are only slightly inferior to plywood;
- properties for holding nails and screws are almost equal to natural wood;
- stable form. Complete absence of structural defects characteristic of other wood chip boards, such as voids and cracks, warped areas and places with fallen knots;
- the internal structure of OSB boards is uniform throughout the entire volume, the quality of both external surfaces is identical;
- high moisture resistance;
- easy mechanical processing. The slabs can be cut, sanded and drilled using ordinary carpentry tools, glued and painted with any paint and varnish materials intended for wood;
- OSB boards are not susceptible to insects;
- treating surfaces with special means increases resistance to moisture and open flame, as a result, the moisture and fire resistance characteristics of OSB boards are higher than that of solid wood.
The characteristics of the filling of SIP panels used to create panel houses are given in articles on expanded polystyrene and mineral wool. Ready-made SIP panels usually have a thickness of 174 and 224 mm, their dimensions are 2,500x1,250 mm and 2,800x1,250 mm, and the average weight per square meter is 17 kg. The walls of a panel house, formed by panels made of oriented strand board and a layer of insulation between them, can withstand temperature differences from -50° to +50°C.
Glued laminated timber - device
This structural material, from which timber houses have been created over the past 100 years, is made from pine, spruce, larch, cedar and fir wood, the debarked trunks of which are cut into lamellas, packages are formed from them and glued together with melamine, resorcinol or polyisocyanate glue (MDI) - the adhesive layer is applied in the thinnest layer. Before gluing, the lamellas are subjected to varietal sorting and drying. Then they are re-culled, examining for the presence of cracks, knots and chips (wane) along the lines of edges and slopes. Wood tension in their structure is relieved by sawing and pressing during the formation of packages, which completely eliminates the formation of through cracks and prevents any distortion. The fibers of adjacent lamellas in the package are selected with opposite fiber orientation, which increases the strength of the final product.
In addition, the strength of some load-bearing elements of the house structure (rafters, floors, columns, trusses, etc.) is further enhanced by gluing metal or plastic reinforcement into the middle of the lamella packages. The ends of the lamellas of various lengths are profiled (milled) to obtain toothed grooves, with which they are joined using glue and pressing to the required length - the production of laminated veneer lumber allows the production of structural material of unlimited length. In addition, using a milling cutter, connecting nodes (usually “groove-tongue”) of building structural elements are formed - houses made of timber are assembled at the installation site like a Lego set, all elements of one building are prepared only in the factory. At the final stage of production, the finished laminated veneer lumber is treated with antiseptic and fire-retardant special agents. Glued laminated timber is produced in thicknesses from 200 to 400 mm, most often 200 mm, because greater thickening seriously affects the increase in its cost.
The timber glued together from lamellas has the following characteristics:
- stability of shape, i.e. there will be no deformation changes during the operation of a house made of laminated veneer lumber;
- almost complete absence of shrinkage (no more than 2%), including seasonal;
- precise geometry of shapes;
- resistance to moisture and seasonal temperature changes;
- the strength of laminated timber is 70% higher than that of wood;
- Compared to wood, the thermal conductivity of laminated timber is lower due to the absence of cracks and other structural damage;
- significantly lower glue content compared to any other laminated wood materials;
- fire resistance.
In addition to the described glue beam, there is another interesting type of it - thermal beam, consisting of two external lamellas with a thickness of 40 to 80 mm and an internal layer of extruded polystyrene foam with a density of 45 kg/m 3. An expanded polystyrene insert, rigidly fixed inside the beam structure using wooden ribs and an adhesive layer, reduces thermal conductivity by 2.5 times, i.e. with a thickness of 200 mm, thermal timber retains heat better than laminated timber with a thickness of 400 mm.
With higher heat resistance, laminated veneer lumber with insulation inside has more low price and weight, compared to laminated veneer lumber. During the process of assembling a house from thermal timber, laminated veneer lumber, which does not contain insulation in its structure, is laid in its lower tier and in the areas where the walls are bound, thereby achieving additional rigidity of the structure. Unlike houses made of thermal timber with 200 mm thick enclosing walls, walls made of laminated timber of similar thickness, according to the requirements of the Russian Federation Law “On Energy Saving” No. 261-FZ, will have to be insulated - in the cold season there will not be enough of them and here it is necessary either insulation or a wall thickness of at least 400 mm is required.
Popular Misconceptions
In Russia, and indeed throughout the world, any new technology first encounters a wall of public opinion, which is mostly conservative. If bathhouses made of timber can be completely assembled and prepared for use in just a month or two, this is considered bad, because “real” bathhouses must go through several stages of shrinkage and repeated caulking of the cracks. What about the panel house? Its design immediately received the label “short-lived”, because there are no such familiar external walls made of concrete, brick or at least wood. Let's look at a few common opinions of this kind...
“Panel houses and those built from timber, and even more so from thermal timber, are short-lived.”
This statement is true in one case - if the house is not properly maintained. And without maintenance and periodic repairs, any house, even a stone one, will certainly decay and collapse. The advantages of a panel house are that any damaged fragment of the enclosing structure can be easily replaced without necessarily damaging the adjacent areas, as would be the case when performing a similar operation with brick wall. Houses made of timber also require periodic maintenance - surface treatment with special means. Proper care will ensure the service life of the house is no less than 50 years.
“The fire hazard of panel houses and houses made of timber is much higher than that of brick houses.”
And this statement is also true - many houses built using these technologies and from these materials burned down immediately after they were put into operation. However, the reason for this lies not in the construction materials, but in the “curvature of the hands” of the builders who installed the chimneys, ventilation systems and electrics. The problem is that many contractors, who publicly declare their competence in building houses from timber and panel houses, actually have a very weak understanding of the assembly process and in general terms - the technology is still new for Russia, there are not enough professional installers. As for the fire hazard of structural enclosing materials, they all undergo mandatory treatment with several layers of fire retardants that prevent direct flame contact with them.
“Low heat capacity of walls - panel houses require more heating.”
Indeed, the heat capacity of walls in panel houses is practically absent, but why is this considered a minus? Judge for yourself: you come in the cold season brick house, which has been without heating for some period and you need to heat it to ensure the required temperature in its rooms. It is not possible to heat such a house within 18-20 hours - the heat-intensive walls will absorb heat, therefore, all the thermal energy produced during this time is only used to heat the walls. And in a panel house, only its premises are heated - no energy is spent on heating the walls.
“Panel houses and houses made of timber are equally not environmentally friendly, because phenol-formaldehyde resins are used to create their elements.”
The mentioned resins are indeed present both in the insulation and in the structural elements of these houses, but their content is significantly lower than in a regular wardrobe made of chipboard located in your bedroom. However, today many manufacturers of OSB boards and laminated timber are abandoning phenol-formaldehyde adhesives in favor of polyisocyanate adhesive that does not contain either phenol or formaldehyde. By the way, nowadays, when choosing any building materials It is worth asking if they have an environmental safety certificate.
“Panel houses will not withstand earthquakes and are not able to withstand strong winds, because... They weigh too little."
The only truth in this statement is that such houses really weigh little, making them easy to transport and not requiring the use of heavy construction equipment during construction work. As for resistance to earthquakes and strong winds, it is more clear to give the following examples from real life:
- 1995, Kobe (Japan). The 7.3 magnitude earthquake destroyed bridges and piers and more than 200 public and residential buildings. Meanwhile, six buildings built using SIP technologies, located just 16 km from the epicenter of the earthquake, not only did not collapse, but did not even receive noticeable damage;
- 1992, Florida (USA). Hurricane Andrew, whose wind speed reached 285 km/h, caused enormous damage to the housing stock of Franklin, raging there for more than 5 hours. The panel houses that were in this city withstood the onslaught of the hurricane, receiving only minor damage to the roof.
It is worth noting that hurricanes with such wind speeds have never been observed in Russia.
“Houses made of panels and made of timber are too expensive.”
That's right - the price of construction materials for these houses is not cheap at all, and specialists are required for the construction itself. However, let's look at it from the other side: the construction itself will take no more than 60 days, and half of this period will be spent on foundation work and external communications; there won't be any additional work on façade finishing and, by and large, interior finishing; All structural elements are adjusted to each other at the factory, i.e. they just need to be assembled on site. And if you can use a brick or wooden house no earlier than in a year, then a panel house and a timber house will be at your disposal in less than 2 months.
Modern houses are much more technologically advanced than the old buildings we are used to, which makes the construction process easier and significantly reduces the heat loss of the house during the cold season. And a professionally made turnkey bathhouse from timber will become not only an ideal place for water treatments, but also a real decoration summer cottage, because its design has no flaws, both external and internal. In conclusion, I will note an important aspect of any construction - construction work should be entrusted to real masters in their field and then the house will be a success.
Rustam Abdyuzhanov, rmnt.ru
“Frame-panel” are buildings erected from ready-made structures manufactured in production according to standard dimensions, according to design documentation. These can be panels, panels with external finishing; sections of walls, roofing, ceilings with thermal insulation, vapor barrier, window units, communications, finishing (internal and external). From us you can buy a ready-made prefabricated house made of panel-type wood cheaply and on a turnkey basis.
Frame-panel technology
Such houses are produced at the factory according to standard designs (made to order - more expensive), made taking into account the sizes of finishing materials, dimensions of mechanisms (cranes, vehicles), which allows:
- Reduce the amount of waste (residues), and therefore the total cost
- Pre-assembled sections are easy to transport by vehicle.
- During the construction process, it is easy to add a floor or section (they are installed in parts).
- Ensure accuracy of parameters.
- Eliminate the dependence of the quality and production time of such structures on the time of year and weather.
Our wooden frame is made from planed wood. Panel production time is 2–4 weeks. On-site installation time is 3–6 days. We present to your attention a catalog of projects of frame-panel houses with inexpensive prices.
One of the profiles of the Brusina company is the construction of turnkey panel houses. Projects with prices are presented in our catalog. Cheap, high quality, just on time - our principles.