От используемых материалов существуют. Основные механические характеристики материалов
Полнотекстовый поиск:
Химия->Дипломная работа
Для разделения азеотропных смесей в технологии основного органического и нефтехимического синтеза широкое распространение получили ректификационные ме...полностью>>
Главная > Реферат >Химия
ФЕДЕРАЛЬНОЕ АГЕНТСТВО ПО ОБРАЗОВАНИЮ
Государственное образовательное учреждение высшего
профессионального образования
РОССИЙСКИЙ ГОСУДАРСТВЕННЫЙ ГУМАНИТАРНЫЙ УНИВЕРСИТЕТ
ИНСТИТУТ ЭКОНОМИКИ, УПРАВЛЕНИЯ И ПРАВА
Экономический факультет
Кафедра экономических теорий
Шохова (Горбушина) Алёна Геннадьевна
контрольная работа по материаловедению
тема №1 «основные свойства материалов»
СТУДЕНТКА 4 КУРСА (СРОК ОБУЧЕНИЯ – 5,5 ЛЕТ)
Научный руководитель
преподаватель
Воропаев Е.Г.
Москва 2011
Введение
Работоспособность машин и агрегатов в значительной степени зависит от свойств материалов, которые характеризуются конкретными параметрами. Параметры материалов определяют с помощью опытных измерений, используя специальные технические средства. Требования к исследуемым стандартным образцам материалов (например, масса, габаритные размеры, чистота поверхности и др.) устанавливаются соответствующими Государственными стандартами.
Механические свойства материалов характеризуют возможность их использования в изделиях, эксплуатируемых при воздействии внешних нагрузок.
Основными показателями свойств материалов являются:
прочность;
твердость;
триботехнические характеристики.
Их параметры существенно зависят от формы, размеров и состояния поверхности образцов, а также режимов испытаний (скорости нагружения, температуры, воздействия окружающих сред и других факторов).
Прочность - свойство материалов сопротивляться разрушению, а также необратимому изменению формы под действием внешних нагрузок. Она обусловлена силами взаимодействия атомных частиц, составляющих материал.
Если при растяжении образца сила внешнего воздействия на пару атомов превосходит силу их притяжения, то атомы будут удаляться друг от друга. Напряжение, возникающее в материале и отвечающее силе межатомного притяжения, соответствует теоретической прочности.
При возникновении в материале локального напряжения больше теоретической прочности произойдет разрыв материала по этому участку. В результате образуется трещина. Рост трещин продолжается, пока в результате их слияния одна из трещин не распространится на все сечение образца и не произойдет его разрушение.
Деформирование - изменение относительного расположения частиц в материале (растяжение, сжатие, изгиб, кручение, сдвиг). Таким образом, деформация - изменение формы и размеров изделия или его частей в результате деформирования. Деформацию называют упругой, если она исчезает после снятия нагрузки, или пластичной, если она не исчезает (необратима).
Реальные материалы обладают технической прочностью, основные характеристики которой удобно рассмотреть с помощью диаграммы растяжения образца из пластичного материала (рис.1).
Предел упругости - напряжение, при котором остаточные деформации (т.е. деформации, обнаруживаемые при разгрузке образца) достигают значения, установленного техническими условиями. Предел упругости σу ограничивает область упругих деформаций материала.
Предел текучести - напряжение, отвечающее нижнему положению площадки текучести на диаграмме для материалов, разрушению которых предшествует заметная пластическая деформация.
Прочие материалы характеризуют условным пределом текучести - напряжением, при котором остаточная деформация достигает значения, установленного техническими условиями. Обычно остаточная деформация не превышает 0,2%. Отсюда и обозначение: σ0,2.
Предел текучести является основной характеристикой прочности пластичных материалов.
Предел прочности - напряжения или деформации, соответствующие максимальному (в момент разрушения образца) значению нагрузки. Отношение наибольшей силы, действующей на образец, к исходной площади его поперечного сечения называют временным сопротивлением (разрушающим напряжением) и обозначают ав.
Предел прочности - основная характеристика механических свойств хрупких материалов, т.е. материалов, которые разрушаются при малых пластических деформациях.
Правила определения характеристик технической прочности материалов при растяжении, сжатии, изгибе, кручении и других видах напряженного состояния установлены государственными стандартами (ГОСТ).
Динамическая прочность - сопротивление материалов динамическим нагрузкам, т.е. нагрузкам, значение, направление и точка приложения которых быстро изменяются во времени.
Усталость материалов - процесс постепенного накопления повреждений под действием переменных напряжений, приводящих к изменению свойств материалов, образованию и разрастанию трещин. Свойство материалов противостоять усталости называется выносливостью.
Ползучесть - непрерывное пластическое деформирование материалов под действием постоянной нагрузки. Любые твердые материалы в той или иной степени подвержены ползучести во всем диапазоне температур эксплуатации. Вредные последствия ползучести материалов особенно проявляются при повышенных температурах.
Причиной неудовлетворительной прочности изделий может быть влияние поверхностных дефектов и напряжений, которые возникают из-за неравномерного распределения нагрузки, обусловленного особенностями конструкции. Поэтому прочность конструкционных элементов (сварочных швов, болтов, валов и т.д.) - конструкционная прочность - во многих случаях ниже технической прочности исходных материалов.
Твердость является механической характеристикой материалов, отражающей их прочность, пластичность и свойства поверхностного слоя изделия. Она выражается сопротивлением материала местному пластическому деформированию, возникающему при внедрении в материал более твердого тела - индентора. В зависимости от способа внедрения и свойств индентора твердость материалов оценивают по различным критериям, используя несколько методов:
вдавливание индентора;
динамические методы;
царапанье.
Вдавливание индентора в образец с последующим измерением отпечатка является основным технологическим приемом при оценке твердости материалов. В зависимости от особенностей приложения нагрузки, конструкции инденторов и определения чисел твердости различают методы:
Бринелля;
Роквелла;
Виккерса.
Динамические методы измерения твердости не приводят к возникновению дефектов поверхности изделий. Распространен способ определения твердости в условных единицах по высоте отскакивания легкого ударника (бойка), падающего на поверхность испытуемого материала с определенной высоты. Применяется и метод измерения твердости с помощью ультразвуковых колебаний, основанный на регистрации изменения частоты колебаний измерительной системы в зависимости от твердости исследуемого материала.
Путем царапанья сравнивают твердость исследуемого и эталонного материалов. В качестве эталонов приняты 10 минералов, расположенных в порядке возрастания их твердости: 1 - тальк, 2 - гипс, 3 - кальцит, 4 - флюорит, 5 - апатит, 6 - ортоклаз, 7 - кварц, 8 - топаз, 9 - корунд, 10 - алмаз.
Триботехнические характеристики определяют эффективность применения материалов в узлах трения.
Под триботехникой понимают совокупность технических средств, обеспечивающих оптимальное функционирование узлов трения.
Основные триботехнические характеристики материалов:
износостойкость;
прирабатываемость;
коэффициент трения.
Износостойкость - свойство материала оказывать сопротивление изнашиванию в определенных условиях трения. Отношение величины износа к интервалу времени, в течение которого он возник, или к пути, на котором происходило изнашивание, представляет собой соответственно скорость изнашивания и интенсивность изнашивания. Износостойкость материалов оценивают величиной, обратной скорости и интенсивности изнашивания.
Прирабатываемость - свойство материала уменьшать силу трения, температуру и интенсивность изнашивания в процессе приработки. Обеспечение износостойкости напрямую связано с предупреждением катастрофического изнашивания и прирабатываемостью.
Коэффициент трения - отношение силы трения двух тел к нормальной силе, прижимающей эти тела друг к другу. Его значения зависят от скорости скольжения, давления и твердости материалов трущихся поверхностей.
Триботехнические характеристики материалов зависят от следующих основных групп факторов, влияющих на работу узлов трения:
внутренних, определяемых природой материалов;
внешних, характеризующих вид трения (скольжение, качение);
среды и вида смазочного материала.
Совокупность этих факторов обусловливает вид изнашивания: абразивное, адгезионное, эрозионное, усталостное и др.
Основная причина всех видов изнашивания - работа сил трения, под действием которых происходит многократное деформирование поверхностных слоев трущихся тел, изменение их структуры, и т.д.
Коррозия - физико-химический процесс изменения свойств, повреждения и разрушения материалов вследствие перехода их компонентов в соединения с компонентами окружающей среды.
Под коррозионным повреждением понимают любой дефект структуры материала, возникший в результате коррозии. Если механические воздействия ускоряют коррозию материалов, а коррозия облегчает их механические разрушения, имеет место коррозионно-механическое повреждение материалов.
Электрохимическая коррозия - процесс взаимодействия материалов и окружающей среды посредством электродных реакций. Металлы наиболее подвержены этому виду коррозии вследствие высокой электрической проводимости и химической активности.
Коррозионное повреждение различных участков материала может быть неодинаковым. По характеру разрушения материалов различают равномерную и местную коррозию. Последняя возникает из-за химической или физической неоднородности среды, и материала на отдельных участках поверхности изделия.
С конструктивными особенностями изделий связаны щелевая и контактная коррозии. Первая протекает внутри или в непосредственной близости от узкого отверстия или зазора в конструкциях. Вторая вызвана контактированием металлов, различающихся по электродному потенциалу.
Для оценки сопротивления материалов коррозии используют следующие параметры:
фронт коррозии - воображаемая поверхность, отделяющая поврежденный материал от неповрежденного;
скорость коррозии - это скорость продвижения ее фронта;
техническая скорость коррозии - ее наибольшая. скорость, вероятностью превышения которой нельзя пренебречь в конкретных условиях.
Сопротивление материалов коррозии характеризуют с помощью параметра коррозионной стойкости - величины, обратной технической скорости коррозии материала в данной коррозионной системе. Условность этой характеристики заключается в том, что она относится не к материалу, а в целом к коррозионной системе. Коррозионную стойкость материала нельзя изменить, не изменив других параметров коррозионной системы. Противокоррозионная защита - это изменение коррозионной системы, ведущее к снижению скорости коррозии материала.
1 Основные механические характеристики материалов
Механические свойства материалов - совокупность показателей, характеризующих сопротивление материала воздействующей на него нагрузке, его способность деформироваться при этом, а также особенности его поведения в процессе разрушения. В соответствии с этим механические свойства материалов измеряют напряжениями (обычно в кгс/мм 2 или Мн/м 2), деформациями (в %), удельной работой деформации и разрушения (обычно в кгс×м/см 2 или Мдж/м 2), скоростью развития процесса разрушения при статической или повторной нагрузке (чаще всего в мм за 1 сек или за 1000 циклов повторений нагрузки, мм/кцикл). Механические свойства материалов определяются при механических испытаниях образцов различной формы.
В общем случае материалы в конструкциях могут подвергаться самым различным по характеру нагрузкам: работать на растяжение, сжатие, изгиб, кручение, срез и т. д. или подвергаться совместному действию нескольких видов нагрузки, например растяжению и изгибу. Также разнообразны условия эксплуатации материалов и по температуре, окружающей среде, скорости приложения нагрузки и закону её изменения во времени. В соответствии с этим имеется много показателей механических свойств и много методов механических испытаний. Для металлов и конструкционных пластмасс наиболее распространены испытания на растяжение, твёрдость, ударный изгиб; хрупкие конструкционные материалы (например, керамику, металлокерамику) часто испытывают на сжатие и статический изгиб; механические свойства композиционных материалов важно оценивать, кроме того, при испытаниях на сдвиг. Для увеличения выносливости при изгибе применяют цементацию. Твердость увеличивает повышенное содержание углерода, но оно обеспечивает и высокую хрупкость материала из-за потери пластичности.
Для того, чтобы оценить свойства не образца, а материала, перестраивается диаграмма растяжения P = f (Dl) в координатах s и e. Для этого уменьшим в F раз ординаты и в l раз абсциссы, где F и l - соответственно площадь поперечного сечения и рабочая длина образца до нагружения. Так как эти величины постоянны, то диаграмма s = f (e) имеет тот же вид, что и диаграмма растяжения, но будет характеризовать уже не свойства образца, а свойства материала.
Наибольшее напряжение, до которого материал следует закону Гука, называется пределов пропорциональности (sn).
Величина предела пропорциональности зависит от той степени точности, с которой начальный участок диаграммы можно рассматривать как прямую. Степень отклонения кривой s = f (e) от прямой s = Еe определяют по величине угла, который составляет касательная к диаграмме с осью s. В пределах закона Гука тангенс этого угла определяется величиной 1/E. Обычно считают, что если величина de/ds оказалась на 50% больше чем 1/Е, то предел пропорциональности достигнут.
Упругие свойства материала сохраняются до напряжения, называемого пределом упругости (sу) - наибольшего напряжения, до которого материал не получает остаточных деформаций.
Для
того чтобы найти предел упругости,
необходимо после каждой дополнительной
нагрузки образец разгружать и следить,
не образовалась ли остаточная деформация.
Так как пластические деформации в
отдельных кристаллах появляются уже в
самой ранней стадии нагружения, ясно,
что величина предела упругости, как и
предела пропорциональности, зависит
от требований точности, которые
накладываются на производимые замеры.
Обычно остаточную деформацию,
соответствующую пределу упругости,
принимают в пределах eост=
(1¸5)
10-5, т. е. 0,001 ¸
0,005%. Соответственно этому допуску
предел упругости обозначается через
s0.001
или s0.005
Следующей характеристикой является предел текучести - напряжение, при котором происходит рост деформации без заметного увеличения нагрузки. В тех случаях, когда на диаграмме отсутствует явно выраженная площадка текучести, за предел текучести принимается условно величина напряжения, при котором остаточная деформация eост = 0,002 или 0,2% (рис. 2). В некоторых случаях устанавливается предел eост =0,5%.
Условный предел текучести обозначается через s0.2 и s0.5 зависимости от принятой величины допуска на остаточную деформацию. Индекс 0,2 обычно в обозначениях предела текучести опускается. Если необходимо отличить предел текучести на растяжение от предела текучести на сжатие, то в обозначение вводится соответственно дополнительный индекс «р» или «с». Таким образом, для предела текучести получаем обозначения sтр и sст.
Предел текучести легко поддается определению и является одной из основных механических характеристик материала.
Отношение максимальной силы, которую способен выдержать образец, к его начальной площади поперечного сечения носит название предела прочности, или временного сопротивления, и обозначается через sвр (сжатие - sвс).
sвр не есть напряжение, при котором разрушается образец. Если относить растягивающую силу не к начальной площади сечения образца, а к наименьшему сечению в данный момент, можно обнаружить, что среднее напряжение в наиболее узком сечении образца перед разрывом существенно больше, чем sвр. Таким образом, предел прочности также является условной величиной. В силу удобства и простоты ее определения она прочно вошла в расчетную практику как основная сравнительная характеристика прочностных свойств материала.
При испытании на растяжение определяется еще одна характеристика материала - удлинение при разрыве d%.
Удлинение
при разрыве представляет собой величину
средней остаточной деформации, которая
образуется к моменту разрыва на
определенной стандартной длине образца.
Определение d%.
производится следующим образом.
Перед испытанием на поверхность образца наносится ряд рисок, делящих рабочую часть образца на равные части. После того как образец испытан и разорван, обе его части составляются по месту разрыва (рис. 3). Далее, по имеющимся на поверхности рискам от сечения разрыва вправо и влево откладываются отрезки, имевшие до испытания длину 5d (рис. 3). Таким образом определяется среднее удлинение на стандартной длине l0 = 10d. В некоторых случаях за l0 принимается длина, равная 5d.
Удлинение при разрыве будет следующим:
Возникающие деформации распределены по длине образца неравномерно. Если произвести обмер отрезков, расположенных между соседними рисками, можно построить эпюру остаточных удлинений, показанную на рис. 3. Наибольшее удлинение возникает в месте разрыва. Оно называется обычно истинным удлинением при разрыве.
Диаграмма растяжения, построенная с учетом уменьшения площади F и местного увеличения деформации, называется истинной диаграммой растяжения.
Пластичность и хрупкость. Твердость
Способность материала получать большие остаточные деформации, не разрушаясь, носит название пластичности. Свойство пластичности имеет решающее значение для таких технологических операций, как штамповка, вытяжка, волочение, гибка и др. Мерой пластичности является удлинение d при разрыве. Чем больше d, тем более пластичным считается материал. Противоположным свойству пластичности является свойство хрупкости, т. е. способность материала разрушаться без образования заметных остаточных деформаций. Материалы, обладающие этим свойством, называются хрупкими. Для таких материалов величина удлинения при разрыве не превышает 2-5%, а в ряде случаев измеряется долями процента. К хрупким материалам относятся чугун, высокоуглеродистая инструментальная сталь, стекло, кирпич, камни и др. Диаграмма растяжения хрупких материалов не имеет площадки текучести и зоны упрочнения (рис. 4).
По-разному
ведут себя пластичные и хрупкие материалы
и при испытании на сжатие. Как уже
упоминалось, испытание на сжатие
производится на коротких цилиндрических
образцах. Для малоуглеродистой стали
диаграмма сжатия образца имеет вид
кривой, показанной на рис. 10. Здесь, как
и для растяжения, обнаруживается площадка
текучести с последующим переходом к
зоне упрочнения. В дальнейшем, однако,
нагрузка не падает, как при растяжении,
а резко возрастает. Происходит это в
результате того, что площадь поперечного
сечения сжатого образца увеличивается;
сам образец вследствие трения на торцах
принимает бочкообразную форму (рис. 5).
Довести образец пластического материала
до разрушения практически не удается.
Испытуемый цилиндр сжимается в тонкий
диск (см. рис. 5), и дальнейшее испытание
ограничивается возможностями машины.
Поэтому предел прочности при сжатии
для такого рода материалов найден быть
не может.
Иначе ведут себя при испытании на сжатие хрупкие материалы. Диаграмма сжатия этих материалов сохраняет качественные особенности диаграммы растяжения (см. рис. 4). Предел прочности хрупкого материала при сжатии определяется так же, как и при растяжении. Разрушение образца происходит с образованием трещин по наклонным или продольным плоскостям.
С
опоставление
предела прочности хрупких материалов
при растяжении sвр
с пределом прочности при сжатии sвр
показывает, что эти материалы обладают,
как правило, более высокими прочностными
показателями при сжатии, нежели при
растяжении. Величина отношения
для чугуна k колеблется в пределах 0,2 ¸ 0,4. Для керамических материалов k = 0,1 ¸ 0,2.
Для пластичных материалов сопоставление прочностных характеристик на растяжение и сжатие ведется по пределу текучести (sтр и sтс). Принято считать, что sтр » sтс.
Существуют материалы, способные воспринимать при растяжении большие нагрузки, чем при сжатии. Это обычно материалы, имеющие волокнистую структуру, - дерево и некоторые типы пластмасс. Этим свойством обладают и некоторые металлы, например магний. Деление материалов на пластичные и хрупкие является условным не только потому, что между теми и другими не существует резкого перехода в показателе d. В зависимости от условий испытания многие хрупкие материалы способны вести себя как пластичные, а пластичные - как хрупкие.
Очень большое влияние на проявление свойств пластичности и хрупкости оказывает время нагружения и температурное воздействие. При быстром нагружении более резко проявляется свойство хрупкости, а при длительном воздействии нагрузок - свойство пластичности. Например, хрупкое стекло способно при длительном воздействии нагрузки при нормальной температуре получать остаточные деформации. Пластичные же материалы, такие, как малоуглеродистая сталь, под воздействием резкой ударной нагрузки проявляют хрупкие свойства.
Одной из основных технологических операций, позволяющих изменять в нужном направлении свойства материала, является термообработка.Известно, например, что закалка резко повышает прочностные характеристики стали и одновременно снижает ее пластические свойства. Для большинства широко применяемых в машиностроении материалов хорошо известны те режимы термообработки, которые обеспечивают получение необходимых механических характеристик материала.
Испытание образцов на растяжение и сжатие дает объективную оценку свойств материала. В производстве, однако, для оперативного контроля над качеством изготовляемых деталей этот метод испытания представляет в ряде случаев значительные неудобства. Например, при помощи испытания на растяжение и сжатие трудно контролировать правильность термообработки готовых изделий. Поэтому на практике большей частью прибегают к сравнительной оценке свойств материала при помощи пробы на твердость.
Под твердостью понимается способность материала противодействовать механическому проникновению в него посторонних тел. Понятно, что такое определение твердости повторяет, по существу, определение свойств прочности. В материале при вдавливании в него острого предмета возникают местные пластические деформации, сопровождающиеся при дальнейшем увеличении сил местным разрушением. Поэтому показатель твердости связан с показателями прочности и пластичности и зависит от конкретных условий ведения, испытания.
Наиболее широкое распространение получили пробы по Бринелю и по Роквеллу. В первом случае в поверхность исследуемой детали вдавливается стальной шарик диаметром 10 мм, во втором - алмазный острый наконечник. По обмеру полученного отпечатка судят о твердости материала. Испытательная лаборатория обычно располагает составленной путем экспериментов переводной таблицей, при помощи которой можно приближенно по показателю твердости определить предел прочности материала. Таким образом, в результате пробы на твердость удается определить прочностные показатели материала, не разрушая детали.
Влияние температуры и фактора времени на механические характеристики материала
Все сказанное выше о свойствах материалов относилось к испытаниям в так называемых нормальных условиях, но диапазон температур, в пределах которого реально работают конструкционные материалы, выходит далеко за рамки указанных нормальных условий. Есть конструкции, где материал находится под действием чрезвычайно высоких температур, как, например, в стенках камер воздушно-реактивных и ракетных двигателей. Имеются конструкции, где, напротив, рабочие температуры оказываются низкими. Это-элементы холодильных установок и резервуары, содержащие жидкие газы.
В широких пределах изменяются также и скорости нагружения, и время действия внешних сил. Существуют нагрузки, весьма медленно меняющиеся и быстро меняющиеся. Есть нагрузки, действующие годами, а есть такие, время действия которых исчисляется миллионными долями секунды. Понятно, что и зависимости от указанных обстоятельств механические свойства материалом будут проявляться по-разному. Обобщающий анализ свойств материала с учетом температуры и времени оказывается очень сложным и не укладывается и простые экспериментально полученные кривые, подобные диаграммам растяжения. Функциональная зависимость между четырьмя параметрами s, e, температурой t° и временем t
f(s,e, t°, t)=0
не является однозначной и содержит в сложном виде дифференциальные и интегральные соотношения входящих в нее величин. Так как в общем виде аналитическое или графическое описание указанной функции дать не удается, то влияние температуры и фактора времени рассматривается в настоящее время применительно к частным классам задач. Деление на классы производится и основном по типу действующих внешних сил. Различают медленно изменяющиеся, быстро и весьма быстро изменяющиеся нагрузки.
Основными
являются медленно изменяющиеся, или
статические нагрузки. Скорость изменения
этих нагрузок во времени настолько
мала, что кинетическая энергия, которую
получают перемещающиеся частицы
деформируемого тела, составляет ничтожно
малую долю от работы внешних сил. Иначе
говоря, работа внешних сил преобразуется
только в упругую потенциальную энергию,
а также в необратимую тепловую энергию,
связанную с пластическими деформациями
тела. Испытание материалов в так
называемых нормальных условиях происходит
под действием статических нагрузок
Е
сли
вести испытания на растяжение при
различных температурах образца,
оставаясь в пределах «нормальных»
скоростей деформации
то можно в определенном интервале получить зависимость механических характеристик от температуры. Эта зависимость обусловлена температурным изменением внутрикристаллических и межкристаллических связей, а в некоторых случаях и структурными изменениями материала.
На рис. 6 показана зависимость от температуры модуля упругости Е, предела текучести sтр, предела прочности sвр и удлинения при разрыве e для малоуглеродистой стали в интервале 0-500°С. Как видно из приведенных кривых, модуль упругости в пределах изменения температуры до 300°С практически не меняется. Более существенные изменения претерпевают величина sвр и, особенно, d, причем имеет место, как говорят, «охрупчивание» стали - удлинение при разрыве уменьшается. При дальнейшем увеличении температуры пластичные свойства стали восстанавливаются, а прочностные показатели быстро падают.
Чем выше температура, тем труднее определить механические характеристики материала.
Изменение во времени деформаций и напряжений, возникающих в нагруженной детали, носит название ползучести.
Частным проявлением ползучести является рост необратимых деформаций при постоянном напряжении. Это явление носит название последействия. Наглядной иллюстрацией последействия может служить наблюдаемое увеличение размеров диска и лопаток газовой турбины, находящихся под воздействием больших центробежных сил и высоких температур. Это увеличение размеров необратимо и проявляется обычно после многих часов работы двигателя.
Другим частным проявлением свойств ползучести является релаксация - самопроизвольное изменение во времени напряжений при неизменной деформации. Релаксацию можно наблюдать, в частности, на примере ослабления затяжки болтовых соединений, работающих в условиях высоких температур.
Вид
диаграмм релаксации, дающих зависимость
напряжения от времени, представлен на
рис. 7. Основными механическими
характеристиками материала в условиях
ползучести являются предел длительной
прочности и предел ползучести.
Пределом длительной прочности называется отношение нагрузки, при которой происходит разрушение растянутого образца через заданный промежуток времени, к первоначальной площади сечения.
Таким образом, предел длительной прочности зависит от заданного промежутка времени до момента разрушения. Последний выбирается равным сроку службы детали и меняется в пределах от десятков часов до сотен тысяч часов. Соответственно столь широкому диапазону изменения времени меняется и предел длительной прочности. С увеличением времени он падает.
Пределом ползучести называется напряжение, при котором пластическая деформация за заданный промежуток времени достигает заданной величины.
Как видим, для определения предела ползучести необходимо задать интервал времени (который определяется сроком службы детали) и интервал допустимых деформаций (который определяется условиями эксплуатации детали). Предел длительной прочности и предел ползучести сильно зависят от температуры. С увеличением температуры они уменьшаются.
Среди различных типов статических нагрузок особое место занимают периодически изменяющиеся, или циклические, нагрузки. Вопросы прочности материалов в условиях таких нагрузок связываются с понятиями выносливости или усталости материала.
После статических рассмотрим класс динамических, нагрузок.
К оценке этих нагрузок существуют два подхода. С одной стороны, нагрузка считается быстро изменяющейся, если она вызывает заметные скорости частиц деформируемого тела, причем настолько большие, что суммарная кинетическая энергия движущихся масс составляет уже значительную долю от общей работы, внешних сил. С другой стороны, скорость изменения нагрузки может быть связана со скоростью протекания пластических деформаций. Нагрузка может рассматриваться как быстро изменяющаяся, если за время нагружения тела пластические деформации не успевают образоваться полностью. Это заметно сказывается на характере наблюдаемых зависимостей между деформациями и напряжениями.
Первый критерий
в оценке быстро изменяющихся нагрузок
используется в основном при анализе
вопросов колебаний упругих тел,
второй - при изучении механических
свойств материалов в связи с процессами
быстрого деформирования. Поскольку
при быстром нагружении образование
пластических деформаций не успевает
полностью завершиться, материал с
увеличением скорости деформации
становится более хрупким и величина d
уменьшается. Так как скольжение частиц
образца по наклонным площадкам затруднено,
должна несколько увеличиться разрушающая
нагрузка. Сказанное иллюстрируется
сопоставлением диаграмм растяжения
при медленно и быстро изменяющихся
силах (рис.
8).
Наиболее заметно сказывается влияние скорости деформации при высоких температурах. В нагретом металле уже при сравнительно небольшом увеличении скорости нагружения обнаруживается тенденция к увеличению sвр и уменьшению d.
Последним из трех рассматриваемых видов нагрузок являются весьма быстро изменяющиеся во времени нагрузки. Скорость их изменения настолько велика, что работа внешних сил почти полностью переходит в кинетическую энергию движущихся частиц тела, а энергия упругих и пластических деформаций оказывается сравнительно малой.
Весьма быстро изменяющиеся нагрузки возникают при ударе тел, движущихся со скоростями в несколько сотен метров в секунду и выше. С этими нагрузками приходится иметь дело при изучении вопросов бронепробиваемости, при оценке разрушающего действия взрывной волны, при исследовании пробивной способности межпланетной пыли, встречающейся на пути космического корабля.
Так как энергия деформации материала в условиях весьма больших скоростей нагружения оказывается сравнительно малой, то свойства материала как твердого тела имеют в данном случае второстепенное значение. На первый план выступают законы движения легко деформируемой (почти жидкой) среды, и особую роль приобретают вопросы физического состояния и физических свойств материала в новых условиях.
2 Температурные характеристики материалов
Параметры, отражающие изменение свойств материалов в зависимости от их температуры, являются одними из важнейших характеристик материалов. Стойкость материалов к повышенным температурам и нагрузкам в значительной степени определяет прогресс в автомобилестроении. Свойство материалов стабильно сохранять комплекс эксплуатационных характеристик при низких температурах влияет на работоспособность машин и оборудования, эксплуатируемых в условиях Севера. При осуществлении технологических процессов (литье, ковка, сварка и др.) важное значение имеет температурное изменение деформационно-прочностных характеристик материалов.
Жаростойкость - когда механические параметры материалов сохраняются или незначительно изменяются при высоких температурах.
Жароупорность - свойство материалов противостоять коррозионному воздействию газов при высокой температуре.
В качестве характеристики жаростойкости легкоплавких материалов используют температуру размягчения, при которой изделие, нагреваемое с установленной скоростью, под действием постоянного изгибающего момента деформируется на допустимую величину.
Для легкоплавких кристаллических материалов (подобных воскам) характеристикой жаростойкости служит температура плавления.
Температура вспышки - температура, при которой пары жидкости образуют с воздухом смесь, вспыхивающую при контакте с источником зажигания (например, электрический разряд). Если продолжить нагревание после вспышки, происходит воспламенение материала, когда к нему подносится открытое пламя. Температуру, при которой материал воспламеняется и после удаления внешнею источника зажигания продолжает гореть не менее 5 с, считают температурой воспламенения.
Жаропрочность - свойство материалов длительное время сопротивляться деформированию и разрушению при высоких температурах, которые имеют место в двигателях внутреннего сгорания.
Хладноломкость - возрастание хрупкости материалов при понижении температуры. При низких температурах (н технике - от 0 до - 50°С) снижается пластичность и вязкость материалов, повышается склонность к хрупкому разрушению. При температурах ниже температурь! вязкого разрушения наступает переход к хрупкому и наблюдается резкое снижение ударной вязкости материала. О его пригодности к эксплуатации при низкой температуре судят по температурному запасу вязкости, равному разности температуры эксплуатации и Т50.
Температурное расширение материалов регистрируют по изменению размеров и формы при изменении температуры. Количественно тепловое расширение твердых материалов характеризуют температурным коэффициентом линейного расширения.
Теплопроводность - перенос энергии от более нагретых участков материала к менее нагретым. Эта величина обусловливает выравнивание температуры изделия.
Коэффициент температуропроводности является мерой теплоизоляционных свойств материала.
3 Электрические и магнитные свойства материалов
В автомобилестроении применяют специальные материалы: электроизоляционные, магнитные, проводниковые, полупроводниковые и другие. Для их эффективного применения необходима информация о параметрах электрических, магнитных и других специфических свойств.
Электропроводность - свойство материалов проводить электрический ток, обусловленное наличием в них подвижных заряженных частиц - носителей тока.
Природу электропроводности твердых материалов объясняет зонная теория, согласно которой энергетический спектр электронов состоит из чередующихся зон разрешенных и запрещенных энергий. В нормальном состоянии электроны могут иметь только определенные значения энергии, т.е. занимать разрешенные энергетические уровни (валентную зону). Пустые или частично заполненные более высокие энергетические уровни образуют зону проводимости. Электроны, возбуждаясь, т.е. приобретая добавочную энергию, например, при нагревании материалов, могут переходить в зону проводимости. Если валентная зона и зона проводимости перекрываются, то при незначительном возбуждении электроны будут перемещаться от одних атомов к другим. Материалы такого типа - проводники - обладают высокой электропроводностью. Электропроводность диэлектриков очень мала, так как переход заметного числа электронов в зону проводимости - случайное явление, обусловленное, например, дефектами структуры.
Электрическое сопротивление - свойство материалов как проводников противодействовать электрическому току.
Вес вещества, помещенные во внешнее магнитное поле, намагничиваются. Намагничивание связано с наличием магнитных моментов у частиц вещества.
Характерной герметикой намагничивания материалов служит намагниченность, равная суммарному магнитному моменту атомов в единичном объеме материала.
Характеризующая связь намагниченности с магнитным полем в материале, называется магнитной восприимчивостью. В зависимости от знака и значения магнитной восприимчивости материалы делят на:
диамагнетики;
парамагнетики;
ферромагнетики.
Диамагнетизм - свойство материалов намагничивания во внешнем магнитном поле в направлении, противоположном полю. Диамагнетизм присущ всем веществам.
Диамагнетики обладают отрицательной магнитной восприимчивостью. Во внешнем магнитном поле они намагничиваются против поля. В отсутствие внешнего магнитного поля диамагнетики немагнитны.
Парамагнетики обладают положительной магнитной восприимчивостью. Они слабо намагничиваются по направлению поля, а в отсутствие поля - немагнитны.
Ферромагнетики характеризуются большим значением магнитной восприимчивости и ее зависимостью от напряженности поля и температуры. Обладают самопроизвольной намагничиваемостью даже в отсутствие внешнего намагничивающего поля.
Антиферромагнетики - материалы, намагниченность которых в отсутствие магнитного поля равна нулю.
Магнитная восприимчивость, как правило, существенно зависит от температуры: у парамагнетиков - уменьшается при нагревании, у ферромагнетиков - увеличивается скачком, достигая максимума вблизи точки Кюри. В точке Кюри исчезает самопроизвольная намагниченность ферромагнитных материалов, и они приобретают свойства обычных парамагнетиков.
4 Химические свойства материалов
Характеризуют их способность реагировать на различные вещества, способные изменить химический состав материала. К химическим свойствам относятся растворимость и коррозионная стойкость, в том числе кислото, щелоче и газостойкость.
Растворимость - способность материала растворяться в воде, масле, бензине, скипидаре и других жидкостях - растворителях. Растворимость может быть и положительным, и отрицательным свойством.
Коррозионная стойкос ть - способность материала сопротивляться коррозионному воздействию среды. Коррозионная среда может быть жидкой (вода, растворы солей, щелочей и кислот, органические растворители) и газообразной (пары, производственные газы).
Кислотостойкость - способность материала сохранять свои свойства под действием кислот.
Щелочестойкость - способность материалов сохранять свои свойства под действием щелочей.
Газостойкость - способность материала не вступать во взаимодействие с газами, находящимися в окружающей среде.
5 Физические свойства материалов
Характеризуют физическое состояние материала, а также его способность реагировать на внешние факторы, не влияющие на химический состав материала.
К физическим свойствам материалов относят:
Модуль упругости первого рода;
Коэффициент температурного (линейного) расширения;
Коэффициент теплопроводности (теплоемкость материала);
Удельный вес материала;
Удельная теплоемкость материала;
Удельное электрическое сопротивление.
6 Технологические свойства материалов
Технологические свойства материалов характеризуют восприимчивость материалов технологическим воздействием при переработке в изделия. Знание этих свойств позволяет рационально осуществлять процессы изготовления изделий.
Основными характеристиками материалов являются:
обрабатываемость резанием;
обрабатываемость давлением;
литейные характеристики;
свариваемость;
склонность к короблению при термической обработке и другие.
Обрабатываемость резанием характеризуют следующими показателями:
качеством обработки материалов - шероховатостью обработанной поверхности и точностью размеров;
стойкостью режущего инструмента;
сопротивлением резанию - скоростью и силой резания;
видом стружкообразования. Обрабатываемость давлением определяют в процессе технологических испытаний (проб) материалов на пластическую деформацию. Методы оценки обрабатываемости давлением зависят от вида материалов и технологии их переработки.
Обрабатываемость давлением порошковых материалов характеризует их текучесть, уплотняемость и формуемость. Методы определения характеристик порошковых материалов установлены государственными стандартами.
Литейные характеристики материалов - совокупность технологических показателей, характеризующие формирование отливки путем заливки расплавленного материала в литейную форму.
Жидкотекучесть - свойство расплавленного материала заполнять литейную форму.
Литейная усадка - уменьшение объема расплава при переходе из жидкого состояния в твердое. Коэффициент усадки индивидуален для каждого вида материала.
Свариваемость - свойство материала образовывать сварное соединение, работоспособность которого соответствует качеству основного материала, подвергнутого сварке. О свариваемости судят по результатам испытания сварных образцов и характеристикам основного материала в зоне сварного шва.
ЗАКЛЮЧЕНИЕ
Так как работоспособность оборудования напрямую зависит от материалов из которого оно изготовлено, то нам крайне важно знать свойства материалов, чтобы оценить прочность, долговечность, качество, сферы использования и границы возможностей данного оборудования.
Список использованной литературы
Тарг С.М. Краткий курс теоретической механики. М; Высшая школа, 1995.
Александров А.В., Потапов В.Д., Державин Б.П. Сопротивление материалов: Учебник для втузов. - М: Высшая школа, М. 1995.-560 с.
Степанова Е.П., Габриель А.С. Сопротивление материалов: Конспект лекций. Омск: Изд-во ОмГТУ, 2005. – 64 с.
М.Л. Бернштейн, В.А Займовский. Механические свойства металлов. Мзд. второе, М., "Металлургия", 1979.
Сорокин. Стали и сплавы Марочник. 2001
Лахтин Ю.М., Леонтьева В.П. Материаловедение, Изд. 2-е, перераб. и доп. М: Машиностроение, 1980.
Арзамасов Б.Н., Макарова В.И., Материаловедение: Учебник для вузов. – М.: МГТУ им.Баумана, 2005. - 646с.
Барташевич А.А., Бахар Л.М. Материаловедение: Учебное пособие.-Изд. 2-е.-Ростов-на-Дону: Феникс, 2005.-348с.
Давыдова И.С., Максина Е.Л., Материаловедение: Учебное пособие. – М.:Изд-во РИОР, 2006. - 240с.
свойств материалов для спортивной одеждыРеферат >> Культура и искусство
... …………………………………………………………………………………………………………..3 Классификация и свойства материалов для спортивной одежды…………….4 Свойства мембранных тканей…………………………………………………………………….6 Свойства материалов типа Gore-tex………………………………………………….6 Свойства материалов типа...
На тему: Основные свойства материалов
Введение
1. Температурные характеристики
2. Электрические и магнитные свойства
3. Технологические свойства
Введение
Работоспособность машин и агрегатов в значительной степени зависит от свойств материалов, которые характеризуются конкретными параметрами. Параметры материалов определяют с помощью опытных измерений, используя специальные технические средства. Требования к исследуемым стандартным образцам материалов (например, масса, габаритные размеры, чистота поверхности и др.) устанавливаются соответствующими Государственными стандартами.
Механические свойства:
Механические свойства материалов характеризуют возможность их использования в изделиях, эксплуатируемых при воздействии внешних нагрузок. Основными показателями свойств материалов являются:
прочность;
твердость;
триботехнические характеристики.
Их параметры существенно зависят от формы, размеров и состояния поверхности образцов, а также режимов испытаний (скорости нагружения, температуры, воздействия окружающих сред и других факторов).
Прочность - свойство материалов сопротивляться разрушению, а также необратимому изменению формы под действием внешних нагрузок. Она обусловлена силами взаимодействия атомных частиц, составляющих материал.
Если при растяжении образца сила внешнего воздействия на пару атомов превосходит силу их притяжения, то атомы будут удаляться друг от друга. Напряжение, возникающее в материале и отвечающее силе межатомного притяжения, соответствует теоретической прочности.
При возникновении в материале локального напряжения больше теоретической прочности произойдет разрыв материала по этому участку. В результате образуется трещина. Рост трещин продолжается, пока в результате их слияния одна из трещин не распространится на все сечение образца и не произойдет его разрушение.
Деформирование - изменение относительного расположения частиц в материале (растяжение, сжатие, изгиб, кручение, сдвиг). Таким образом, деформация - изменение формы и размеров изделия или его частей в результате деформирования. Деформацию называют упругой, если она исчезает после снятия нагрузки, или пластичной, если она не исчезает (необратима).
Реальные материалы обладают технической прочностью, основные характеристики которой удобно рассмотреть с помощью диаграммы растяжения образца из пластичного материала (рис.1).
Предел упругости - напряжение, при котором остаточные деформации (т.е. деформации, обнаруживаемые при разгрузке образца) достигают значения, установленного техническими условиями. Предел упругости σу ограничивает область упругих деформаций материала.
Предел текучести - напряжение, отвечающее нижнему положению площадки текучести на диаграмме для материалов, разрушению которых предшествует заметная пластическая деформация.
Прочие материалы характеризуют условным пределом текучести - напряжением, при котором остаточная деформация достигает значения, установленного техническими условиями. Обычно остаточная деформация не превышает 0,2%. Отсюда и обозначение: σ0,2.
Предел текучести является основной характеристикой прочности пластичных материалов.
Предел прочности - напряжения или деформации, соответствующие максимальному (в момент разрушения образца) значению нагрузки. Отношение наибольшей силы, действующей на образец, к исходной площади его поперечного сечения называют временным сопротивлением (разрушающим напряжением) и обозначают ав.
Предел прочности - основная характеристика механических свойств хрупких материалов, т.е. материалов, которые разрушаются при малых пластических деформациях.
Правила определения характеристик технической прочности материалов при растяжении, сжатии, изгибе, кручении и других видах напряженного состояния установлены государственными стандартами (ГОСТ).
Динамическая прочность - сопротивление материалов динамическим нагрузкам, т.е. нагрузкам, значение, направление и точка приложения которых быстро изменяются во времени.
Усталость материалов - процесс постепенного накопления повреждений под действием переменных напряжений, приводящих к изменению свойств материалов, образованию и разрастанию трещин. Свойство материалов противостоять усталости называется выносливостью.
Ползучесть - непрерывное пластическое деформирование материалов под действием постоянной нагрузки. Любые твердые материалы в той или иной степени подвержены ползучести во всем диапазоне температур эксплуатации. Вредные последствия ползучести материалов особенно проявляются при повышенных температурах.
Причиной неудовлетворительной прочности изделий может быть влияние поверхностных дефектов и напряжений, которые возникают из-за неравномерного распределения нагрузки, обусловленного особенностями конструкции. Поэтому прочность конструкционных элементов (сварочных швов, болтов, валов и т.д.) - конструкционная прочность - во многих случаях ниже технической прочности исходных материалов.
Твердость является механической характеристикой материалов, отражающей их прочность, пластичность и свойства поверхностного слоя изделия. Она выражается сопротивлением материала местному пластическому деформированию, возникающему при внедрении в материал более твердого тела - индентора. В зависимости от способа внедрения и свойств индентора твердость материалов оценивают по различным критериям, используя несколько методов:
вдавливание индентора;
динамические методы;
царапанье.
Вдавливание индентора в образец с последующим измерением отпечатка является основным технологическим приемом при оценке твердости материалов. В зависимости от особенностей приложения нагрузки, конструкции инденторов и определения чисел твердости различают методы:
Бринелля;
Роквелла;
Виккерса.
Динамические методы измерения твердости не приводят к возникновению дефектов поверхности изделий. Распространен способ определения твердости в условных единицах по высоте отскакивания легкого ударника (бойка), падающего на поверхность испытуемого материала с определенной высоты. Применяется и метод измерения твердости с помощью ультразвуковых колебаний, основанный на регистрации изменения частоты колебаний измерительной системы в зависимости от твердости исследуемого материала.
Путем царапанья сравнивают твердость исследуемого и эталонного материалов. В качестве эталонов приняты 10 минералов, расположенных в порядке возрастания их твердости: 1 - тальк, 2 - гипс, 3 - кальцит, 4 - флюорит, 5 - апатит, 6 - ортоклаз, 7 - кварц, 8 - топаз, 9 - корунд, 10 - алмаз.
Триботехнические характеристики определяют эффективность применения материалов в узлах трения.
Под триботехникой понимают совокупность технических средств, обеспечивающих оптимальное функционирование узлов трения.
Основные триботехнические характеристики материалов:
износостойкость;
прирабатываемость;
коэффициент трения.
Износостойкость - свойство материала оказывать сопротивление изнашиванию в определенных условиях трения. Отношение величины износа к интервалу времени, в течение которого он возник, или к пути, на котором происходило изнашивание, представляет собой соответственно скорость изнашивания и интенсивность изнашивания. Износостойкость материалов оценивают величиной, обратной скорости и интенсивности изнашивания.
Прирабатываемость - свойство материала уменьшать силу трения, температуру и интенсивность изнашивания в процессе приработки. Обеспечение износостойкости напрямую связано с предупреждением катастрофического изнашивания и прирабатываемостью.
Коэффициент трения - отношение силы трения двух тел к нормальной силе, прижимающей эти тела друг к другу. Его значения зависят от скорости скольжения, давления и твердости материалов трущихся поверхностей.
Триботехнические характеристики материалов зависят от следующих основных групп факторов, влияющих на работу узлов трения:
внутренних, определяемых природой материалов;
внешних, характеризующих вид трения (скольжение, качение);
среды и вида смазочного материала.
Совокупность этих факторов обусловливает вид изнашивания: абразивное, адгезионное, эрозионное, усталостное и др.
Основная причина всех видов изнашивания - работа сил трения, под действием которых происходит многократное деформирование поверхностных слоев трущихся тел, изменение их структуры, и т.д.
Коррозионная стойкость
Коррозия - физико-химический процесс изменения свойств, повреждения и разрушения материалов вследствие перехода их компонентов в соединения с компонентами окружающей среды.
Под коррозионным повреждением понимают любой дефект структуры материала, возникший в результате коррозии. Если механические воздействия ускоряют коррозию материалов, а коррозия облегчает их механические разрушения, имеет место коррозионно-механическое повреждение материалов.
Электрохимическая коррозия - процесс взаимодействия материалов и окружающей среды посредством электродных реакций. Металлы наиболее подвержены этому виду коррозии вследствие высокой электрической проводимости и химической активности.
Коррозионное повреждение различных участков материала может быть неодинаковым. По характеру разрушения материалов различают равномерную и местную коррозию. Последняя возникает из-за химической или физической неоднородности среды, и материала на отдельных участках поверхности изделия.
С конструктивными особенностями изделий связаны щелевая и контактная коррозии. Первая протекает внутри или в непосредственной близости от узкого отверстия или зазора в конструкциях. Вторая вызвана контактированием металлов, различающихся по электродному потенциалу.
Для оценки сопротивления материалов коррозии используют следующие параметры:
фронт коррозии - воображаемая поверхность, отделяющая поврежденный материал от неповрежденного;
скорость коррозии - это скорость продвижения ее фронта;
техническая скорость коррозии - ее наибольшая. скорость, вероятностью превышения которой
нельзя пренебречь в конкретных условиях. Сопротивление материалов коррозии характеризуют с помощью параметра коррозионной стойкости - величины, обратной технической скорости коррозии материала в данной коррозионной системе. Условность этой характеристики заключается в том, что она относится не к материалу, а в целом к коррозионной системе. Коррозионную стойкость материала нельзя изменить, не изменив других параметров коррозионной системы. Противокоррозионная защита - это изменение коррозионной системы, ведущее к снижению скорости коррозии материала.
1. Температурные характеристики
Параметры, отражающие изменение свойств материалов в зависимости от их температуры, являются одними из важнейших характеристик материалов. Стойкость материалов к повышенным температурам и нагрузкам в значительной степени определяет прогресс в автомобилестроении. Свойство материалов стабильно сохранять комплекс эксплуатационных характеристик при низких температурах влияет на работоспособность машин и оборудования, эксплуатируемых в условиях Севера. При осуществлении технологических процессов (литье, ковка, сварка и др.) важное значение имеет температурное изменение деформационно-прочностных характеристик материалов.
Жаростойкость - когда механические параметры материалов сохраняются или незначительно изменяются при высоких температурах.
Жароупорность - свойство материалов противостоять коррозионному воздействию газов при высокой температуре.
В качестве характеристики жаростойкости легкоплавких материалов используют температуру размягчения, при которой изделие, нагреваемое с установленной скоростью, под действием постоянного изгибающего момента деформируется на допустимую величину.
Для легкоплавких кристаллических материалов (подобных воскам) характеристикой жаростойкости служит температура плавления.
Температура вспышки - температура, при которой пары жидкости образуют с воздухом смесь, вспыхивающую при контакте с источником зажигания (например, электрический разряд). Если продолжить нагревание после вспышки, происходит воспламенение материала, когда к нему подносится открытое пламя. Температуру, при которой материал воспламеняется и после удаления внешнею источника зажигания продолжает гореть не менее 5 с, считают температурой воспламенения.
Жаропрочность - свойство материалов длительное время сопротивляться деформированию и разрушению при высоких температурах, которые имеют место в двигателях внутреннего сгорания.
Хладноломкость - возрастание хрупкости материалов при понижении температуры. При низких температурах (н технике - от 0 до - 50°С) снижается пластичность и вязкость материалов, повышается склонность к хрупкому разрушению. При температурах ниже температурь! вязкого разрушения наступает переход к хрупкому и наблюдается резкое снижение ударной вязкости материала. О его пригодности к эксплуатации при низкой температуре судят по температурному запасу вязкости, равному разности температуры эксплуатации и Т50.
Температурное расширение материалов регистрируют по изменению размеров и формы при изменении температуры. Количественно тепловое расширение твердых материалов характеризуют температурным коэффициентом линейного расширения.
Теплопроводность - перенос энергии от более нагретых участков материала к менее нагретым. Эта величина обусловливает выравнивание температуры изделия.
Коэффициент температуропроводности является мерой теплоизоляционных свойств материала.
2. Электрические и магнитные свойства
В автомобилестроении применяют специальные материалы: электроизоляционные, магнитные, проводниковые, полупроводниковые и другие. Для их эффективного применения необходима информация о параметрах электрических, магнитных и других специфических свойств.
Электропроводность - свойство материалов проводить электрический ток, обусловленное наличием в них подвижных заряженных частиц - носителей тока.
Природу электропроводности твердых материалов объясняет зонная теория, согласно которой энергетический спектр электронов состоит из чередующихся зон разрешенных и запрещенных энергий. В нормальном состоянии электроны могут иметь только определенные значения энергии, т.е. занимать разрешенные энергетические уровни (валентную зону). Пустые или частично заполненные более высокие энергетические уровни образуют зону проводимости. Электроны, возбуждаясь, т.е. приобретая добавочную энергию, например при нагревании материалов, могут переходить в зону проводимости. Если валентная зона и зона проводимости перекрываются, то при незначительном возбуждении электроны будут перемещаться от одних атомов к другим. Материалы такого типа - проводники - обладают высокой электропроводностью. Электропроводность диэлектриков очень мала, так как переход заметного числа электронов в зону проводимости - случайное явление, обусловленное, например, дефектами структуры.
Электрическое сопротивление - свойство материалов как проводников противодействовать электрическому току.
Вес вещества, помещенные во внешнее магнитное поле, намагничиваются. Намагничивание связано с наличием магнитных моментов у частиц вещества.
Характерной герметикой намагничивания материалов служит намагниченность, равная суммарному магнитному моменту атомов в единичном объеме материала.
Характеризующая связь намагниченности с магнитным полем в материале, называется магнитной восприимчивостью. В зависимости от знака и значения магнитной восприимчивости материалы делят на:
диамагнетики;
парамагнетики;
ферромагнетики.
Диамагнетизм - свойство материалов намагничивания во внешнем магнитном поле в направлении, противоположном полю. Диамагнетизм присущ всем веществам.
Диамагнетики обладают отрицательной магнитной восприимчивостью. Во внешнем магнитном поле они намагничиваются против поля. В отсутствие внешнего магнитного поля диамагнетики немагнитны.
Парамагнетики обладают положительной магнитной восприимчивостью. Они слабо намагничиваются по направлению поля, а в отсутствие поля - немагнитны.
Ферромагнетики характеризуются большим значением магнитной восприимчивости и ее зависимостью от напряженности поля и температуры. Обладают самопроизвольной намагничиваемостью даже в отсутствие внешнего намагничивающего поля.
Антиферромагнетики - материалы, намагниченность которых в отсутствие магнитного поля равна нулю.
Магнитная восприимчивость, как правило, существенно зависит от температуры: у парамагнетиков - уменьшается при нагревании, у ферромагнетиков - увеличивается скачком, достигая максимума вблизи точки Кюри. В точке Кюри исчезает самопроизвольная намагниченность ферромагнитных материалов, и они приобретают свойства обычных парамагнетиков.
3. Технологические свойства
Технологические свойства материалов характеризуют восприимчивость материалов технологическим воздействием при переработке в изделия. Знание этих свойств позволяет рационально осуществлять процессы изготовления изделий.
Основными характеристиками материалов являются:
обрабатываемость резанием;
обрабатываемость давлением;
литейные характеристики;
свариваемость;
склонность к короблению при термической обработке и другие.
Обрабатываемость резанием характеризуют следующими показателями:
качеством обработки материалов - шероховатостью обработанной поверхности и точностью размеров;
стойкостью режущего инструмента;
сопротивлением резанию - скоростью и силой резания;
видом стружкообразования. Обрабатываемость давлением определяют в процессе технологических испытаний (проб) материалов на пластическую деформацию. Методы оценки обрабатываемости давлением зависят от вида материалов и технологии их переработки.
Обрабатываемость давлением порошковых материалов характеризует их текучесть, уплотняемость и формуемость. Методы определения характеристик порошковых материалов установлены государственными стандартами.
Литейные характеристики материалов - совокупность технологических показателей, характеризующие формирование отливки путем заливки расплавленного материала в литейную форму.
Жидкотекучесть - свойство расплавленного материала заполнять литейную форму.
Литейная усадка - уменьшение объема расплава при переходе из жидкого состояния в твердое. Коэффициент усадки индивидуален для каждого вида материала.
Свариваемость - свойство материала образовывать сварное соединение, работоспособность которого соответствует качеству основного материала, подвергнутого сварке. О свариваемости судят по результатам испытания сварных образцов и характеристикам основного материала в зоне сварного шва.
Похожие рефераты:
Характеристика физических, механических и химических свойств материалов, применяемых в промышленном производстве. Технологические испытания стали на изгиб, осадку, сплющивание, загиб и бортование. Изучение строения металлов, сплавов и жидких расплавов.
Сущность пластической деформации металлов и влияние на неё химического состава, структуры, температуры нагрева, скорости и степени деформации. Определение легированных сталей, их состав. Литейные сплавы на основе алюминия: их маркировка и свойства.
Изучение свойств материалов, установления величины предельных напряжений. Условный предел текучести. Механические характеристики материалов. Испытание на растяжение, сжатие, кручение, изгиб хрупких материалов статической нагрузкой. Измерение деформаций.
Физические свойства металлов. Способность металлов отражать световое излучение с определенной длиной волны. Плотность металла и температура плавления. Значение теплопроводности металлов при выборе материала для деталей. Характеристика магнитных свойств.
Перемещение дислокаций при любых температурах и скоростях деформирования в основе пластического деформирования металлов. Свойства пластически деформированных металлов, повышение прочности, рекристаллизация. Структура холоднодеформированных металлов.
Общая характеристика магнитных методов неразрушающего контроля, подробная характеристика магнитопорошкового метода. Выявление поверхностных и подповерхностных дефектов типа нарушения сплошности материала изделия (непроварка стыковых сварных соединений).
Свойства материалов при расчетах на прочность, жесткость и устойчивость определяются механическими характеристиками. Испытания над материалами проводят на деформацию растяжения, сжатия, кручения, изгиба при действии статической или переменной нагрузок.
Зависимость деформационных свойств пластмасс от температуры. Зависимость прочности полимеров от скорости нагружения. Усталостные свойства пластмасс. Проектирование экономически эффективных изделий из пластмасс. Метод механической обработки заготовок.
Качественные и количественные методы исследования коррозии металлов и ее оценки. Определение характера и интенсивности коррозионного процесса с помощью качественного метода с применением индикаторов. Измерение скорости коррозии металла весовым методом.
Описание способов достижения высокой конструктивной прочности железного изделия. Основные формы осуществления мартенситного превращения. Описание относительных температур для различных видов стали. Характеристика стальных изделий с высокой пластичностью.
Введение
1 Классификация строительных материалов по роду сырья, общности технологического процесса их изготовления, функциональному назначению и областям применения.
Чтобы легче ориентироваться в многообразии строительных материалов и изделий, их классифицируют по назначению, исходя из условий работы материалов в сооружениях, или по технологическому признаку, учитывая вид сырья, из которого получают материал, и способ изготовления.
По назначению материалы можно условно разделить на две группы: конструкционные и материалы специального назначения.
Конструкционные материалы, применяемые главным образом для несущих конструкций, различают следующие: 1) природные каменные; 2) .вяжущие; 3) искусственные каменные, получаемые: а) омоноличиванием с помощью вяжущих веществ (бетон, железобетон, растворы); б) спеканием (керамические материалы); в) плавлением (стекло и ситаллы); 4) металлы (сталь, чугун, алюминий, сплавы); 5) полимеры; 6) древесные; 7) композиционные (асбестоцемент, бетонополимер, фибробетон, стеклопластик и др.).
Строительные материалы специального назначения, необходимые для защиты конструкций от вредных воздействий среды или повышения эксплуатационных свойств и создания комфорта, следующие: 1) теплоизоляционные; 2) акустические; 3) гидроизоляционные, кровельные и герметизирующие; 4) отделочные; 5) антикоррозионные; 6) огнеупорные; 7) материалы для защиты от радиационных воздействий и др.
Главным требованием к материалам, из которых изготовляются несущие конструкции, является их способность хорошо сопротивляться изменению формы и разрушению под действием нагрузок, а также в ряде случаев низкие теплопроводность и звукопроницаемость (например, для ограждающих конструкций). Основными требованиями к некоторым материалам являются: водонепроницаемость, низкая электропроводность, радиационная стойкость и т. д.
Плотность, пористость, прочность - это основные характеристики всех строительных материалов, служащие как для оценки качества и особенностей применения материала, так и для различных технико-экономических расчетов. Специальные технологические свойства характеризуют способность материала подвергаться обработке. Например, для каменных материалов важной является способность шлифоваться и полироваться. Податливость к сравнительно легкой формуемости глин и бетонных смесей при производстве строительных изделий является важной технологической характеристикой.
Таким образом, при выборе и обосновании целесообразности применения строительного материала для определенных условий его применения требуется учитывать различные его свойства.
По ряду признаков часто выделяют четыре основные группы технических свойств: физические, механические, химические и технологические.
1 Строение и основные свойства строительных материалов.
1.Взаимосвязь состава, строения и свойств строительных материалов.
Свойства строительного материала определяются его структурой. Для получения материала заданных свойств следует создать его внутреннюю структуру, обеспечивающую необходимые технические характеристики. В конечном итоге знание свойств материалов необходимо для наиболее эффективного его использования в конкретных условиях эксплуатации.
Структуру строительного материала изучают на трех уровнях: макроструктура - строение материала, видимое невооруженным глазом; микроструктура - строение, видимое через микроскоп; внутреннее строение вещества, изучаемое на молекулярно-ионном уровне (физико-химические методы исследования - электронная микроскопия, термография, рентгеноструктурный анализ и др.).
Макроструктуру твердых строительных материалов (исключая горные породы, имеющие свою геологическую классификацию) делят на следующие группы: конгломератная, ячеистая, мелкопористая, волокнистая, слоистая и рыхлозернистая (порошкообразная). Искусственные конгломераты представляют собой большую группу; это различного вида бетоны, керамические и другие материалы. Ячеистая структура материала отличается наличием макропор; она свойственна газо- и пенобетонам, газосиликатам и др. Мелкопористая структура характерна, например, для керамических материалов, получаемых в результате выгорания введенных органических веществ. Волокнистая структура присуща древесине, изделиям из минеральной ваты и др. Слоистая структура характерна для листовых, плитных и рулонных материалов. Рыхлозернистые материалы - это заполнители для бетонов, растворов, различного вида засыпка для тепло-звукоизоляции и др.
По физическому состоянию все вещества, в том чесле и все материалы используемые в строительстве (строительные материалы) подразделяют на твердые, жидкие, газообразные и плазму.
В штукатурных и малярных работах используют материалы, которые находятся в твердом или жидком состоянии.
Твердым телом называют всякое тело, имеющее определенную форму.
Так, к твердым телам относят металлы, камни, лед, воск, битум, стекло и др. Твердые тела могут находиться в кристаллическом (гранит, металлы, лед) и аморфном (воск, стекло, эбонит) состояниях.
Кристаллические тела имеют упорядоченное взаимное расположение образующих их частиц - атомов и молекул, а аморфные - хаотическое их расположение. Кристаллические вещества обладают характерным свойством переходить из твердого состояния в жидкое при определенной, постоянной для данного вещества, температуре. Эта температура, называемая температурой плавления, равна температуре отвердевания (каждое расплавленное вещество при охлаждении вновь отвердевает). Аморфные вещества не имеют четко выраженной температуры плавления и отвердевания, при нагревании они постепенно размягчаются и переходят в жидкое состояние.
Твердые материалы, используемые в штукатурных и малярных работах, бывают сыпучими и комовыми.
Жидкость - агрегатное состояние вещества, сочетающее в себе черты твердого состояния (сохранение объема, определенная прочность на разрыв) и газообразного (изменчивость формы).
В процессе работы штукатуры и маляры имеют дело не только с твердыми и жидкими веществами, но и с так называемыми коллоидно-дисперсными системами и растворами, различными смесями, составами.
Дисперсные системы - образования из двух или большего числа фаз (тел) с сильно развитой поверхностью раздела между ними.
В дисперсных системах одна из фаз - дисперсная фаза - распределена в виде мелких частиц (кристалликов, капель, пузырьков) в другой фазе - дисперсионной среде - газе, жидкости или твердом теле.
Дисперсность - характеристика размеров твердых частиц и капель жидкости (чем мельче частицы, тем больше дисперсность).
На практике в качестве дисперсных систем, размер частиц которых более 0,1 мкм, используют суспензии, эмульсии, коллоиды.
Грубодисперсные системы (суспензии, эмульсии, порошки, пена) неустойчивы; чрезмерное измельчение порошков ведет к их слипанию (коагуляции).
Суспензия -система, в которой частицы твердой дисперсной фазы взвешены в жидкой дисперсионной среде.
К таким системам относятся готовые к применению краски, являющиеся суспензиями пигментов и наполнителей в связующих веществах и растворителях, шпатлевки, подмазочные пасты.
Эмульсия - система, состоящая из двух не растворяющихся друг в друге жидкостей, одна из которых (дисперсная фаза) распределена в другой (дисперсионной среде).
В суспензиях и эмульсиях частицы дисперсной фазы стремятся к седиментации, т. е. к осаждению. В дополнение к этому они могут коагулировать, сцепляться под действием молекулярных сил.
Коллоиды - промежуточные системы между истинными растворами и грубодисперсными системами.
Гелеобразование - одно из важнейших свойств коллоидных систем.
Гели образуются в результате действия молекулярных сил сцепления между коллоидными частицами. Образование гелей имеет значение для объяснения процессов твердения и свойств цементного камня и полимерных материалов.
Ячеистая структура геля удерживает значительное количество жидкой дисперсионной среды. Под действием механических усилий многие гели способны переходить в золи, т. е. разжижаться, это явление называется тиксотропией и проявляется оно при вибрировании бетонных, растворных и других смесей.
Коллоиды способны к набуханию, при этом они увеличиваются в объеме. Животные клеи, белок, крахмал, мыло - коллоиды, которые при длительном соприкосновении с водой образуют коллоидные растворы (золи).
В отличие от грубодисперсных систем коллоидные растворы стойки к седиментации, обладают свечением в проходящем свете и передвижением частиц к электродам при пропускании электротока.
Истинный раствор - молекулярно-дисперсная гомогенная (однородная) система переменного состава из двух и более компонентов.
Раствор называется истинным потому, что вещества действительно и самопроизвольно растворяются в подходящем растворителе с образованием гомогенной системы.
Истинные растворы устойчивы в течение длительного времени. С истинным раствором маляр имеет дело всякий раз, когда растворяет в воде кристаллы медного купороса, квасцов, каустическую соду, кислоту, спирт.
Важнейшее практическое значение имеют явления, происходящие на поверхности раздела фаз для всех дисперсных и особенно коллоидных систем. К таким явлениям относится адсорбция - поглощение и концентрирование вещества на поверхности раздела фаз.
Адсорбирующиеся в ещества называются поверхностно-активными (ПАВ), они понижают поверхностное натяжение, имеют большое значение в технологии строительных материалов. ПАВ способствуют получению устойчивых эмульсий и суспензий (адсорбционный слой обволакивает частицы дисперсной фазы и не дает им слипаться); за счет эффекта адсорбционного понижения прочности ускоряют измельчение порошков, пластифицируют растворные и бетонные смеси, гидрофобизуют поверхности и пр.
2.Свойства, характеризующие особенности физического состояния материалов: плотность, пористость, пустотность
Плотностью называется масса единицы объема материала. р = т/У. (3.1)Большинство строительных материалов – пористые материалы, т.е. в их объеме помимо твердого вещества находятся воздушные ячейки (поры), заполненные воздухом, плотность которого несравнимо ниже плотности твердого вещества. Поэтому для строительных материалов определяют две характеристики: истинную и среднюю плотности. Для характеристики материалов, состоящих из отдельных зерен (цемент, песок, гравий), используют так называемую насыпную плотность.Истинной плотность р называют плотность того вещества, из которого состоит материал. Средней плотность рт называют плотность материала, когда при ее расчете берется его полный объем в естественном состоянии, включая поры и пустоты.Насыпная плотность рнас характеризует отношение массы зернистых и порошкообразных материалов ко всему занимаемому ими объему, включая и пространства между частицами.
Пористость - степень заполнения объема материала порами. Пористость - величина относительная, выражается в процентах или долях объема материала. Пористость строительных материалов колеблется в пределах от 0 (сталь, стекло) до 90...98 % (пенопласт) Пористость материала характеризуют не только с количественной стороны, но и по характеру пор: замкнутые и открытые, мелкие (размером в сотые и тысячные доли миллиметра) и крупные (от десятых долей миллиметра до 2...5 мм). По характеру пор оценивают способность материала поглощать воду. Величина пористости в значительной мере влияет на прочность материала. Строительный материал тем слабее сопротивляется механическим нагрузкам, тепловым, усадочным и другим усилиям, чем больше пор в его объеме. Величина прочности также зависит от размеров пор. Она возрастает с их уменьшением. Прочность мелкопористых материалов, а также материалов с закрытой пористостью выше, чем прочность крупнопористых и с открытой пористостью.
Пустотность - отношение суммарного объема пустот в рыхлом материале ко всему объему, занимаемому этим материалом.
3.Гидрофизические и теплофизические свойства материалов.
Гидрофизические свойства стройматериалов. Водопоглощение - способность материала или изделия впитывать и удерживать в порах и капиллярах воду. Водопоглощение используют для оценки структуры материала с помощью коэффициента насыщения: kн = Wo/П. Уменьшение kн говорит о повышении морозостойкости.
Водопроницаемость - это свойство материала пропускать воду под давлением. Коэффициент фильтрации kф (м/ч - размерность скорости) характеризует водопроницаемость: kф=Vв*а/, где kф=Vв - количество воды, м
Водонепроницаемость материала характеризуется маркой W2; W4; W8; W10; W12, обозначающей одностороннее гидростатическое давление в кгс/см², при котором бетонный образец-цилиндр не пропускает воду в условиях стандартного испытания.
Водостойкость - способность материалов оказывать длительное сопротивление разрушающему действию воды.характеризуется коэффициентом размягчения kp = Rв/Rс, где Rв - прочность материала насыщенного водой, а Rс - прочность сухого материала.
Гигроскопичность - свойство капиллярно-пористого материала поглощать водяной пар из воздуха.
Теплофизические свойства стройматериалов.
Теплопроводность - свойство материала передавать тепло от одной поверхности к другой. При повышении температуры теплопроводность большинства материалов возрастает.
Огнеупорность - свойство материала выдерживать длительное воздействие высокой температуры (от 1580 °C и выше), не размягчаясь и не деформируясь.
Огнестойкость - свойство материала сопротивляться действию огня при пожаре в течение определённого времени.
4.Механические свойства.
ПРОЧНОСТЬ Свойство материала сопротивляться разрушениям под действием напряжений, возникающих от нагрузок, влияния температуры, атмосферных осадков и других факторов. В конструкциях строительные материалы, подвергаясь различным нагрузкам, испытывают напряжение сжатия, растяжения, изгиба, среза и удара. Чаще всего они работают на сжатие или на растяжение. Природные камни, а также бетоны и кирпич хорошо сопротивляются сжатию, значительно хуже - срезу, а еще слабее - растяжению. На растяжение они выдерживают нагрузку в 10- 15 раз меньшую, чем на сжатие. Поэтому указанные материалы следует применять главным образом в строительных конструкциях, работающих на сжатие. Предел прочности определяют нагружением испытуемых образцов материала до их разрушения (на прессах или разрывных машинах). Признаками разрушения являются появление трещин на образце, отслаивание и деформации.
Уменьшение величин допускаемого напряжения объясняется следующими факторами.
1. Полученные при испытаниях показатели дают представление
только о среднем значении прочности материалов. Наиболее слабые ча
сти их разрушаются раньше, чем напряжение достигнет средней вели
чины предела прочности. Многие материалы, нагруженные до напря
жения, составляющего только часть предела прочности (50-70%),
сильно деформируются. Следовательно, запас прочности надо прини
мать тем больше, чем менее однороден материал.
2. В каменных и других хрупких материалах образуются трещины
раньше достижения напряжения, равного пределу прочности.
3. При многократной переменной нагрузке под влиянием так назы
ваемой усталости материала он может разрушаться при напряжении,
равном только половине предела прочности.
4. Под действием атмосферы изменяются первоначальные свойст
ва материала, со временем происходит его «старение», сопровождаемое
понижением прочности.
Для обеспечения сооружениям достаточной прочности при действии перечисленных факторов, а также нагрузок, не учтенных в расчетах, в нормах на строительное проектирование установлены определенные запасы прочности для различных материалов и конструкций.
2. Твердостью называется свойство материала сопротивляться прониканию в него постороннего более твердого тела. Твердость однородных каменных материалов определяют по шкале твердости, в которой десять специально подобранных минералов расположены в таком порядке, что на каждом из них все последующие могут оставлять черту. Для определения твердости древесины, стали и бетона в образцы
вдавливают стальной шарик под определенной нагрузкой и определяют
глубину вдавливания.
3. Истираемостью называют способность материала уменьшаться в весе и объеме под действием истирающих усилий. Истираемость имеет большое значение для тех материалов, которые в условиях службы в строительных конструкциях подвергаются истирающему воздействию (например, материалы для полов, лестниц, угольных и других бункеров).
4. Сопротивлением удару называется способность материала сопротивляться ударным воздействиям.
Строительные материалы в некоторых конструкциях (в полах, дорожных покрытиях, бункерах) кроме истирания подвергаются также ударным воздействиям.
5. Упругостью называется свойство материала восстанавливать первоначальную форму после снятия нагрузки, под действием которой форма материала в той или иной мере изменяется. Восстановление первоначальной формы может быть полным при малых нагрузках и неполным при больших. Предел упругости материала - это то наибольшее напряжение при различных видах деформации материала, при котором еще не обнаруживается их остаточная (пластическая) деформация.
6. Пластичностью называют способность материала под влиянием действующих на него усилий изменять свои размеры и форму без образования трещин и сохранять ее после снятия нагрузки.
Помимо материалов пластичных (битумы, дерево, глиняное тесто и др.) имеются материалы хрупкие, которые разрушаются без предварительной деформации, как только действующие на них усилия достигают величины разрушающих нагрузок. Пластичность и хрупкость материалов могут существенно изменяться в зависимости от таких факторов, как влажность, температура, скорость нарастания действующей нагрузки.
5.Химические свойства материалов Химические свойства материала характеризуют его способность к химическим превращениям под влиянием веществ (воздействий), с которыми он находится в соприкосновении, а также способность сохранять постоянными состав и структуру материала в условиях инертной окружающей среды. Некоторые материалы склонны к самопроизвольным внутренним химическим изменениям в обычной среде. Ряд материалов проявляет активность при взаимодействии с кислотами, водой, щелочами, растворами солей, агрессивными газами и т. Д. Химические превращения протекают также во время технологических процессов производства и применения материалов. Химическая (коррозионная) стойкость - свойство материала сопротивляться коррозионному воздействию среды (жидкой, газообразной, твердой) или физических воздействий (облучение, электрический ток). При контакте с агрессивной средой в структуре материала происходят необратимые изменения, что вызывает снижение его прочности и преждевременное разрушение конструкции. Основными агрессивными агентами, вызывающими коррозию строительных материалов, являются: пресная и соленая вода, минерализованные почвенные воды, растворенные в дождевой воде газы (S03, S02, C02, N02) от промышленных предприятий и автомашин. На промышленных предприятиях коррозию строительных материалов часто вызывают более сильные агенты: растворы кислот и щелочей, расплавленные материалы и горячие газы. Способность материалов не разрушаться в химически агрессивных средах характеризует их химическую стойкость. Химическая стойкость зависит от структуры материалов и их состава. Повышение химической стойкости материалов достигается введением в их состав легирующих элементов, образованием защитных покрытий и другими способами. Химический состав неметаллических кислотостойких материалов представлен преимущественно кислотными оксидами, щелочестойких - основными оксидами. Например, силикатные материалы (стекло, кварц, асбест и др.), содержащие в основном оксид кремния, стойки к действию кислот, но при определенных условиях взаимодействуют со щелочами, а цементный камень, известняк, мрамор, в составе которых превалирует оксид кальция, щелочестойки, но легко разрушаются кислотами. К основным химическим свойствам относят способность материалов сопротивляться действию химически агрессивной среды, вызывающие в них обменные реакции приводящие к разрушению материалов, изменению своих первоначальных свойств: растворимость, коррозионная стойкость, стойкость против гниения, твердение
Основы конструирования приборов
Реферат по теме
Основные механические характеристики материалов
Студента группы ИУ 3-32
Кондратова Николая
Диаграмма растяжения
Построение диаграммы растяжения-сжатия является основной задачей испытаний на растяжение-сжатие. Для этих испытаний используются цилиндрические образцы; полученные диаграммы являются зависимостью между силой, действующей на образец, и его удлинением. На рис. 1 показана типичная для углеродистой стали диаграмма испытания образца в координатах P , D l . Кривая условно может быть разделена на четыре зоны.
Зона ОА носит название зоны упругости. Здесь материал подчиняется закону Гука и
Рис. 1.
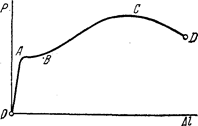
Зона АВ называется зоной общей текучести, а. участок АВ диаграммы - площадкой текучести. Здесь происходит существенное изменение длины образца без заметного увеличения нагрузки. В большинстве случаев при испытании на растяжение и сжатие площадка АВ не обнаруживается, и диаграмма растяжения образца имеет вид кривых, показанных на рис. 2. Кривая 1 типична для алюминия и отожженной меди, кривая 2 - для высококачественных легированных сталей.
Зона ВС называется зоной упрочнения. Здесь удлинение образца сопровождается возрастанием нагрузки, но неизмеримо более медленным (в сотни раз), чем на упругом участке. В стадии упрочнения на образце намечается место будущего разрыва и начинает образовываться так называемая шейка - местное сужение образца (рис.3). По мере растяжения образца утонение шейки прогрессирует. Когда относительное уменьшение площади сечения сравняется с относительным возрастанием напряжения, сила Р достигнет максимума (точка С). В дальнейшем удлинение образца происходит с уменьшением силы, хотя среднее напряжение в поперечном сечении шейки и возрастает. Удлинение образца носит в этом случае местный характер, и поэтому участок кривойCD называется зоной местной текучести. ТочкаD соответствует разрушению образца. У многих материалов разрушение происходит без заметного образования шейки.
Если испытуемый образец, не доводя до разрушения, разгрузить (точка К рис. 4), то в процессе, разгрузки зависимость между силой Р и удлинением Dl изобразится прямой К L (рис. 4). Опыт показывает, что эта прямая параллельна прямой ОА.
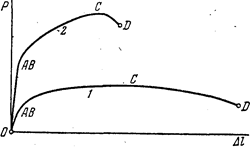
ОМ=Dlупр + Dlост.
Соответственно
e =eупр + eост
Если образец был нагружен в пределах участка ОА и затем разгружен, то удлинение будет чисто упругим, и Dlост = 0.
При повторном нагружении образца диаграмма растяжения принимает вид прямойLK и далее - кривойKCD (рис.4), как будто промежуточной разгрузки и не было.Если взять два одинаковых образца, изготовленных из одного и того же материала, причем один из образцов до испытания нагружению не подвергается, а другой - был предварительно нагружен силами, вызвавшими в образце остаточные деформации.
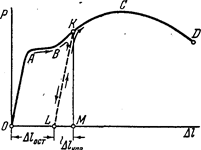
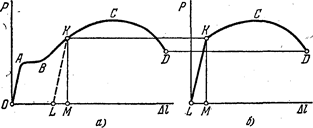
Например, для придания упругих свойств листовой меди или латуни, ее в холодном состоянии прокатывают на валках. Цепи, тросы, ремни часто подвергают предварительной вытяжке силами, превышающими рабочие, с тем, чтобы избежать остаточных удлинений в дальнейшем. В некоторых случаях явление наклепа оказывается нежелательным, как, например, в процессе штамповки многих тонкостенных деталей. В этом случае для того, чтобы избежать разрыва листа, вытяжку производят в несколько ступеней. Перед очередной операцией вытяжки деталь подвергается отжигу, в результате которого наклеп снимается.
Основные механические характеристики материала
Для того, чтобы оценить свойства не образца, а материала, перестраивается диаграмма растяжения P = f (Dl) в координатах s и e. Для этого уменьшим вF раз ординаты ивl раз абсциссы, где F и l - соответственно площадь поперечного сечения и рабочая длина образца до нагружения. Так как эти величины постоянны, то диаграмма s =f (e) имеет тот же вид, что и диаграмма растяжения, но будет характеризовать уже не свойства образца, а свойства материала.
Наибольшее напряжение, до которого материал следует закону Гука, называется пределов пропорциональности (sn).
Величина предела пропорциональности зависит от той степени точности, с которой начальный участок диаграммы можно рассматривать как прямую. Степень отклонения кривой s = f (e) от прямой s = Е e определяют по величине угла, который составляет касательная к диаграмме с осьюs. В пределах закона Гука тангенс этого угла определяется величиной 1/E . Обычно считают, что если величина de/ds оказалась на 50% больше чем 1/Е, то предел пропорциональности достигнут.
Упругие свойства материала сохраняются до напряжения, называемого пределом упругости (s у) --- наибольшего напряжения, до которого материал не получает остаточных деформаций.
Для того чтобы найти предел упругости, необходимо после каждой дополнительной нагрузки образец разгружать и следить, не образовалась ли остаточная деформация. Так как пластические деформации в отдельных кристаллах появляются уже в самой ранней стадии нагружения, ясно, что величина предела упругости, как и предела пропорциональности, зависит от требований точности, которые накладываются на производимые замеры. Обычно остаточную деформацию, соответствующую пределу упругости, принимают в пределах eост= (1¸5) 10 -5 , т. е. 0,001 ¸ 0,005%. Соответственно этому допуску предел упругости обозначается черезs 0.001 или s 0.005
Следующей характеристикой является предел текучести --- напряжение, при котором происходит рост деформации без заметного увеличения нагрузки. В тех случаях, когда на диаграмме отсутствует явно выраженная площадка текучести, за предел текучести принимается условно величина напряжения, при котором остаточная деформация e ост = 0,002 или 0,2% (рис. 6). В некоторых случаях устанавливается предел e ост =0,5%.
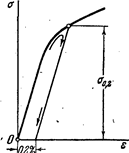
Предел текучести легко поддается определению и является одной из основных механических характеристик материала.
Отношение максимальной силы, которую способен выдержать образец, к его начальной площади поперечного сечения носит название предела прочности, или временного сопротивления, и обозначается через s вр (сжатие - s вс).
s вр не есть напряжение, при котором разрушается образец. Если относить растягивающую силу не к начальной площади сечения образца, а к наименьшему сечению в данный момент, можно обнаружить, что среднее напряжение в наиболее узком сечении образца перед разрывом существенно больше, чем s вр. Таким образом, предел прочности также является условной величиной. В силу удобства и простоты ее определения она прочно вошла в расчетную практику как основная сравнительная характеристика прочностных свойств материала.
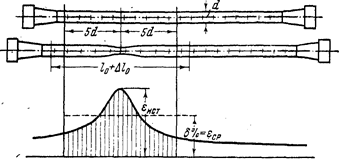
Удлинение при разрыве представляет собой величину средней остаточной деформации, которая образуется к моменту разрыва на определенной стандартной длине образца. Определение d %. производится следующим образом.
Перед испытанием на поверхность образца наносится ряд рисок, делящих рабочую часть образца на равные части. После того как образец испытан и разорван, обе его части составляются по месту разрыва (рис. 7). Далее, по имеющимся на поверхности рискам от сечения разрыва вправо и влево откладываются отрезки, имевшие до испытания длину 5d (рис. 7). Таким образом определяется среднее удлинение на стандартной длине l 0 = 10d. В некоторых случаях за l 0 принимается длина, равная 5d.
Удлинение при разрыве будет следующим:
Возникающие деформации распределены по длине образца неравномерно. Если произвести обмер отрезков, расположенных междусоседними рисками, можно построить эпюру остаточных удлинений, показанную на рис. 7. Наибольшее удлинение возникает в месте разрыва. Оно называется обычно истинным удлинением при разрыве.
Диаграмма растяжения, построенная с учетом уменьшения площадиF и местного увеличения деформации, называется истинной диаграммой растяжения (криваяOC"D" на рис. 8).
Рис. 8 D’
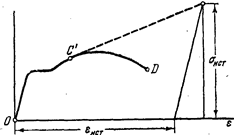
Пластичность и хрупкость. Твердость
Способность материала получать большие остаточные деформации, не разрушаясь, носит название пластичности. Свойство пластичности имеет решающее значение для таких технологических операций, как штамповка, вытяжка, волочение, гибка и др. Мерой пластичности является удлинение d при разрыве. Чем больше d, тем более пластичным считается материал. Противоположным свойству пластичности является свойство хрупкости, т. е. способность материала разрушаться без образования заметных остаточных деформаций. Материалы, обладающие этим свойством, называются хрупкими. Для таких материалов величина удлинения при разрыве не превышает 2-5%, а в ряде случаев измеряется долями процента. К хрупким материалам относятся чугун, высокоуглеродистая инструментальная сталь, стекло, кирпич, камни и др. Диаграмма растяжения хрупких материалов не имеет площадки текучести и зоны упрочнения (рис. 9).
Рис. 9По-разному ведут себя пластичные и хрупкие материалы и при испытании на сжатие. Как уже упоминалось, испытание на сжатие производится на коротких цилиндрических образцах. Для малоуглеродистой стали диаграмма сжатия образца имеет вид кривой, показанной на рис. 10. Здесь, как и для растяжения, обнаруживается площадка текучести с последующим переходом к зоне упрочнения. В дальнейшем, однако, нагрузка не падает, как при растяжении, а резко возрастает. Происходит это в результате того, что площадь поперечного сечения сжатого образца увеличивается; сам образец вследствие трения на торцахпринимает бочкообразную форму (рис. 11). Довести образец пластического материала до разрушения практически не удается. Испытуемый цилиндр сжимается в тонкий диск (см. рис. 11), и дальнейшее испытание ограничивается возможностями машины. Поэтому предел прочности при сжатии для такого рода материалов найден быть не может.
Рис. 10 Рис. 11
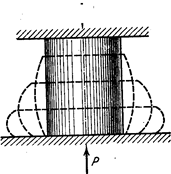
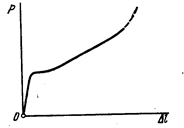
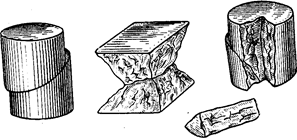
для чугунаk колеблется в пределах 0,2 ¸ 0,4. Для керамических материалов k = 0,1 ¸ 0,2.
Для пластичных материалов сопоставление прочностных характеристик на растяжение и сжатие ведется по пределу текучести (s тр и s тс).Принято считать, что s тр »s тс.
Существуют материалы, способные воспринимать при растяжении большие нагрузки, чем при сжатии. Это обычно материалы, имеющие волокнистую структуру, - дерево и некоторые типы пластмасс. Этим свойством обладают и некоторые металлы, например магний. Деление материалов на пластичные и хрупкие является условным не только потому, что между теми и другими не существует резкого перехода в показателе d. В зависимости от условий испытания многие хрупкие материалы способны вести себя как пластичные, а пластичные - как хрупкие.
Очень большое влияние на проявление свойств пластичности и хрупкости оказывает время нагружения и температурное воздействие. При быстром нагружении более резко проявляется свойство хрупкости, а при длительном воздействии нагрузок - свойство пластичности. Например, хрупкое стекло способно при длительном воздействии нагрузки при нормальной температуре получать остаточные деформации. Пластичные же материалы, такие, как малоуглеродистая сталь, под воздействием резкой ударной нагрузки проявляют хрупкие свойства.
Одной из основных технологических операций, позволяющих изменять в нужном направлении свойства материала, является термообработка.Известно, например, что закалка резко повышает прочностные характеристики стали и одновременно снижает ее пластические свойства. Для большинства широко применяемых в машиностроении материалов хорошо известны те режимы термообработки, которые обеспечивают получение необходимых механических характеристик материала.
Испытание образцов на растяжение и сжатие дает объективную оценку свойств материала. В производстве, однако, для оперативного контроля над качеством изготовляемых деталей этот метод испытания представляет в ряде случаев значительные неудобства. Например, при помощи испытания на растяжение и сжатие трудно контролировать правильность термообработки готовых изделий. Поэтому на практике большей частью прибегают к сравнительной оценке свойств материала при помощи пробы на твердость.
Под твердостью понимается способность материала противодействовать механическому проникновению в него посторонних тел. Понятно, что такое определение твердости повторяет, по существу, определение свойств прочности. В материале при вдавливании в него острого предмета возникают местные пластические деформации, сопровождающиеся при дальнейшем увеличении сил местным разрушением. Поэтому показатель твердости связан с показателями прочности и пластичности и зависит от конкретных условий ведения, испытания.
Наиболее широкое распространение получили пробы по Бринелю и по Роквеллу. В первом случае в поверхность исследуемой детали вдавливается стальной шарик диаметром 10 мм, во втором - алмазный острый наконечник. По обмеру полученного отпечатка судят о твердости материала. Испытательная лаборатория обычно располагает составленной путем экспериментов переводной таблицей, при помощи которой можно приближенно по показателю твердости определить предел прочности материала. Таким образом, в результате пробы на твердость удается определить прочностные показатели материала, не разрушая детали.
Влияние температуры и фактора времени на механические характеристики материала
Все сказанное выше о свойствах материалов относилось к испытаниям в так называемых нормальных условиях, но диапазон температур, в пределах которого реально работают конструкционные материалы, выходит далеко за рамки указанных нормальных условий. Есть конструкции, где материал находится под действием чрезвычайно высоких температур, как, например, в стенках камер воздушно-реактивных и ракетных двигателей. Имеются конструкции, где, напротив, рабочие температуры оказываются низкими. Это-элементы холодильных установок и резервуары, содержащие жидкие газы.
В широких пределах изменяются также и скорости нагружения, и время действия внешних сил. Существуют нагрузки, весьма медленно меняющиеся и быстро меняющиеся. Есть нагрузки, действующие годами, а есть такие, время действия которых исчисляется миллионными долями секунды. Понятно, что и зависимости от указанных обстоятельств механические свойства материалом будут проявляться по-разному. Обобщающий анализ свойств материала с учетом температуры и времени оказывается очень сложным и не укладывается и простые экспериментально полученные кривые, подобные диаграммам растяжения. Функциональная зависимость между четырьмя параметрами s, e, температуройt° и временемt
f ( s , e , t° , t ) =0
не является однозначной и содержит в сложном виде дифференциальные и интегральные соотношения входящих в нее величин. Так как в общем виде аналитическое или графическое описание указанной функции дать не удается, то влияние температуры и фактора времени рассматривается в настоящее время применительно к частным классам задач. Деление на классы производится и основном по типу действующих внешних сил.Различают медленно изменяющиеся, быстро и весьма быстро изменяющиеся нагрузки.
Основными являются медленно изменяющиеся, или статические нагрузки. Скорость изменения этих нагрузок во времени настолько мала, что кинетическая энергия, которую получают перемещающиеся частицы деформируемого тела, составляет ничтожно малую долю от работы внешних сил. Иначе говоря, работа внешних сил преобразуется только в упругую потенциальную энергию, а также в необратимую тепловую энергию, связанную с пластическими деформациями тела. Испытание материалов в так называемых нормальных условиях происходит под действием статических нагрузок
![]() |
Если вести испытания на растяжение при различных температурах образца, оставаясь в пределах «нормальных» скоростей деформации
то можно в определенном интервале получить зависимость механических характеристик от температуры. Эта зависимость обусловлена температурным изменением внутрикристаллических и межкристаллических связей, а в некоторых случаях и структурными изменениями материала.
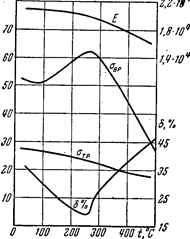
Чем выше температура, тем труднее определить механические характеристики материала.
Изменение во времени деформаций и напряжений, возникающих в нагруженной детали, носит название ползучести.
Частным проявлением ползучести является рост необратимых деформаций при постоянном напряжении. Это явление носит название последействия. Наглядной иллюстрацией последействия может служить наблюдаемое увеличение размеров диска и лопаток газовой турбины, находящихся под воздействием больших центробежных сил и высоких температур. Это увеличение размеров необратимо и проявляется обычно после многих часов работы двигателя.
Другим частным проявлением свойств ползучести является релаксация - самопроизвольное изменение во времени напряжений при неизменной деформации. Релаксацию можно наблюдать, в частности, на примере ослабления затяжки болтовых соединений, работающих в условиях высоких
температур.
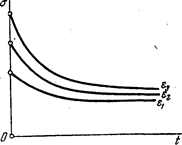
Пределом длительной прочности называется отношение нагрузки, при которой происходит разрушение растянутого образца через заданный промежуток времени, к первоначальной площади сечения.
Таким образом, предел длительной прочности зависит от заданного промежутка времени до момента разрушения. Последний выбирается равным сроку службы детали и меняется в пределах от десятков часов до сотен тысяч часов. Соответственно столь широкому диапазону изменения времени меняется и предел длительной прочности. С увеличением времени он падает.
Пределом ползучести называется напряжение, при котором пластическая деформация за заданный промежуток времени достигает заданной величины.
Как видим, для определения предела ползучести необходимо задать интервал времени (который определяется сроком службы детали) и интервал допустимых деформаций (который определяется условиями эксплуатации детали). Предел длительной прочности и предел ползучести сильно зависят от температуры. С увеличением температуры они уменьшаются.
Среди различных типов статических нагрузок особое место занимают периодически изменяющиеся, или циклические, нагрузки. Вопросы прочности материалов в условиях таких нагрузок связываются с понятиями выносливости или усталости материала.
После статических рассмотрим класс динамических, нагрузок.
К оценке этих нагрузок существуют два подхода. С одной стороны, нагрузка считается быстро изменяющейся, если она вызывает заметные скорости частиц деформируемого тела, причем настолько большие, что суммарная кинетическая энергия движущихся масс составляет уже значительную долю от общей работы, внешних сил. С другой стороны, скорость изменения нагрузки может быть связана со скоростью протекания пластических деформаций. Нагрузка может рассматриваться как быстро изменяющаяся, если за время нагружения тела пластические деформации не успевают образоваться полностью. Это заметно сказывается на характере наблюдаемых зависимостей между деформациями и напряжениями.
Первый критерий в оценке быстро изменяющихся нагрузок используется в основном при анализе вопросов колебаний упругих тел, второй - при изучении механических свойств материалов в связи с процессами быстрого деформирования. Поскольку при быстром нагружении образование пластических деформаций не успевает полностью завершиться, материал с увеличением скорости деформации становится более хрупким и величина d уменьшается. Так как скольжение частиц образца по наклонным площадкам затруднено, должна несколько увеличиться разрушающая нагрузка. Сказанное иллюстрируется сопоставлением диаграмм растяжения при медленно и быстро изменяющихся силах (рис. 15).
Наиболее заметно сказывается влияние скорости деформации при высоких температурах. В нагретом металле уже при сравнительно небольшом увеличении скорости нагружения обнаруживается тенденция к увеличениюs вр и уменьшению d.
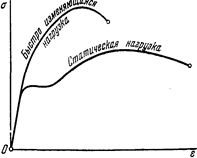
Весьма быстро изменяющиеся нагрузки возникают при ударе тел, движущихся со скоростями в несколько сотен метров в секунду и выше. С этими нагрузками приходится иметь дело при изучении вопросов бронепробиваемости, при оценке разрушающего действия взрывной волны, при исследовании пробивной способности межпланетной пыли, встречающейся на пути космического корабля.
Так как энергия деформации материала в условиях весьма больших скоростей нагружения оказывается сравнительно малой, то свойства материала как твердого тела имеют в данном случае второстепенное значение. На первый план выступают законы движения легко деформируемой (почти жидкой) среды, и особую роль приобретают вопросы физического состояния и физических свойств материала в новых условиях.