Нормативные документы. ТТК. Устройство шероховатой поверхностной обработки асфальтобетонного покрытия путем одиночной поверхностной обработки
ПОВЕРХНОСТНАЯ ОБРАБОТКА ДОРОЖНЫХ ПОКРЫТИЙ
Поверхностная обработка – технологический процесс устройства на дорожных покрытиях тонких слоев с целью обеспечить шероховатость, водонепроницаемость, износостойкость и плотность покрытий. Слой, устраиваемый этим способом, также называют поверхностной обработкойПоверхностные обработки используются:
Либо как профилактический слой, который закрывает и предохраняет в плохую погоду основные конструктивные слои дорожных покрытий от преждевременного разрушения;
либо как слой износа, подверженный стиранию в процессе движения, предохраняя наилучшим образом структуру дороги. Такому слою требуется только периодическое обновление для придания структуре дороги ее первоначальных качеств;
либо как верхний слой дорожного покрытия с характеристиками шероховатости, обеспечивающими сцепление и хорошее дренирование поверхностных вод, приводящими к значительному понижению порога аквапланирования и создающими, благодаря повышенному удельному давлению, хорошее сопротивление формированию гололеда.
Кроме технических преимуществ, поверхностные обработки имеют достаточно конкурентоспособную стоимость по сравнению с комплексом верхних слоев дорожных одежд, используемых в этих случаях.
Существует много различных способов устройства поверхностных обработок, из которых в настоящей статье рассматривается лишь один – использование для этой цели фракционного щебня и различных органических вяжущих, в том числе эмульгированных.
Чтобы создать поверхностную обработку, соответствующую представленным требованиям, необходимо при ее устройстве соблюдать несколько принципиальных положений:
Использовать вяжущее, которое прочно и надолго соединяется с поверхностью покрытия или основания. Это соединение называется парой «вяжущее – основа»;
каменный материал должен быть прикреплен к покрытию или основанию, а каждая щебенка должна быть прочно соединена с соседними. Это взаимодействие называют парой «вяжущее – щебень»;
количество вяжущего должно быть достаточным, чтобы покрыть пленкой каждую щебенку на необходимую высоту и заполнить все микротрещины покрытия, но не быть избыточным, чтобы не выступать на поверхность щебеночного слоя. Это основной принцип дозировки и распределения вяжущего;
каменный материал должен быть чистым, обладать высокими физико-механическими свойствами (прочностью, морозостойкостью, сопротивлением истиранию и др.), иметь определенные формы и размеры. Это основные требования к каменным материалам;
количество каменного материала должно быть достаточным, чтобы создать нужную структуру поверхности, но не быть излишним, чтобы избежать необходимости удаления его. Это принцип дозировки и распределения каменного материала;
каждая щебенка должна занять наиболее стабильное положение, а все вместе должны создавать сплошной монолитный слой с шероховатой поверхностью. Это основной принцип уплотнения.
Таковы основные принципы обеспечения высокого качества поверхностной обработки. Кроме того, есть ряд дополнительных условий:
Все работы по устройству поверхностной обработки должны быть выполнены в наиболее благоприятных условиях погоды. Это принцип назначения сроков выполнения работ;
до начала работ должны быть решены все организационные вопросы, касающиеся поставки материалов, подготовки машин и оборудования. Это принцип организации работ;
в процессе работ должны строго выполняться требования к технологии производства работ и качеству применяемых материалов. Это принцип организации контроля качества.
Поверхностные обработки с использованием фракционированного щебня устраивают преимущественно на участках дорог с опасными и затрудненными условиями движения на дорогах I – III категорий.
В зависимости от типа и состояния покрытия поверхностные обработки могут быть одиночными и двойными; на цементобетонных покрытиях – только двойными.
Требования к материалам
Щебень
Щебень поверхностной обработки воспринимает и передает на нижележащие слои нагрузку от автомобилей, служит слоем износа и обеспечивает сцепление между дорогой и колесами автомобилей.
Каменный материал, применяемый для устройства поверхностной обработки, должен обладать высокими физико-механическими свойствами, такими как прочность, морозоустойчивость, сопротивление удару и износу (истиранию), хорошей прочностью сцепления с вяжущим и т.д. Соответствие горной породы вяжущему определяют путем испытания в лабораторных условиях на прочность сцепления.
Влияние формы щебенок на стабильность их положения
Рис. 1. Влияние формы щебенок на стабильность их положения
Форма щебенок должна быть как можно ближе к кубической, чтобы обеспечить устойчивое положение на поверхности покрытия. Яйцевидная форма щебенок, так называемая форма «колумбового яйца», не имеет стабильного положения. Плоские плитки и щебенки в виде вытянутой иглы хрупки и плохо укладываются в покрытие (рис. 1).
Щебень поверхностной обработки должен быть очень чистым, что обуславливает его тщательную мойку во время производства. Наличие глины, даже в очень слабых пропорциях, весьма нежелательно: глина крайне гидрофильна, и сильное разбухание, которое происходит при наличии воды, приводит к тенденции разрыва связки «вяжущее – щебень».
Правильно выбранная форма и размер щебенок формируют шероховатость поверхностной обработки, обеспечивают снижение шума в салоне автомобиля при движении.
Прицепной битумощебнераспределитель БЩР-375 совместного производства ОАО "Строммашина" и фирмы Breining (Fayat Group), Германия
Прицепной битумощебнераспределитель БЩР-375 совместного производства ОАО «Строммашина» и фирмы Breining (Fayat Group), Германия
Важное значение имеет выбор размера щебня. Установлено, что размеры щебня порядка 10–15 и 15–20 мм вызывают довольно высокий уровень шума в салоне автомобиля и мешают прослушиванию музыки при скорости движения более 130 км/ч. Исходя из этого, отдают предпочтение поверхностной обработке из щебня фракций 5–10 мм.
Еще один фактор, который необходимо учитывать при назначении требований к размеру щебня, состоит в исключении возможности разбития лобовых стекол автомобилей щебенками, вылетающими из-под колес автомобилей при движении с высокой скоростью. Использование мелкозернистого щебня позволяет почти полностью решить эту проблему.
Для устройства поверхностных обработок применяют щебень марки не ниже 1200 по ГОСТ 8267-82 из трудношлифуемых изверженных и метаморфических горных пород для автомобильных дорог I и II категорий, марки 1000 – для дорог III категории и марки не ниже 800 – для дорог IV категории, фракций 5–10, 10–15, 15–20 мм (допускается применение щебня фракций 5–15 и 10–20 мм при условии обеспечения коэффициента сцепления) преимущественно кубовидной формы зерен (зерна пластинчатой формы составляют не более 15%); содержание пылеватых, глинистых и илистых частиц в щебне не должно превышать 1% массы. Выбор фракции щебня производят в зависимости от твердости дорожного покрытия.
Вяжущее
При устройстве поверхностной обработки в качестве вяжущих используют вязкие битумы, битумы с добавками дегтей, битумы и дегти с добавками полимеров, битумные эмульсии.
Вяжущее обеспечивает гидроизоляцию покрытия, приклеивание каменного материала к покрытию или основанию и соединение щебенок в единый слой.
Марку битума выбирают по ГОСТ 22245-90 с учетом дорожно-климатической зоны: для I – БНД 90/130 и БНД 130/200, для II и III – БНД 60/90, БНД 90/130, БНД 130/200, БН 60/90, БН 90/130 и БН 130/200, для IV и V – БНД 60/90, БНД 90/130, БН 60/90 и БН 90/130.
Битум должен выдерживать испытание на сцепление со щебнем, используемым для устройства поверхностной обработки. При неудовлетворительном сцеплении битума со щебнем следует использовать добавки соответствующих ПАВ или производить предварительную обработку щебня дегтем или смесью битума с дегтем.
Применяемые каменноугольные дегти должны иметь марку Д-5, Д-6 или Д-7 по ГОСТ 4641-80 и использоваться на автомобильных дорогах не выше III категории. На участках дорог, проходящих по населенным пунктам, применение каменноугольных дегтей не разрешается.
При устройстве поверхностной обработки с использованием эмульсий применяют преимущественно катионные битумные эмульсии класса ЭБК-1, ЭБК-2, отвечающие требованиям ГОСТ 52128. В условиях III – IV дорожно-климатических зон и при благоприятных погодных условиях во II зоне допускается применение анионных эмульсий класса ЭБА-1, ЭБА-2. Эмульсии должны выдерживать испытание на сцепление пленки вяжущего со щебнем.
При устройстве поверхностной обработки на катионных битумных эмульсиях используют необработанный органическим вяжущим щебень, на анионных эмульсиях – преимущественно черный щебень.
При устройстве поверхностной обработки на дорогах с интенсивностью движения свыше 3000 авт/сут., с движением преимущественно грузовых автомобилей, также в районах с резко континентальным климатом применяют битум и деготь с добавками полимеров. Дегтеполимерное вяжущее используют на дорогах не выше II категории.
Виды поверхностных обработок
Различают несколько видов поверхностных обработок, каждая из которых имеет свою сферу наиболее эффективного применения (рис. 2).
Виды поверхностных обработок
Рис. 2. Виды поверхностных обработок
Однослойная поверхностная обработка с однократным распределением вяжущего и щебня. Применяется для создания шероховатой поверхности и слоя износа дорожной одежды с достаточной прочностью. Это самый распространенный вид шероховатой поверхностной обработки, наиболее подходящий для всех видов движения. Чаще всего она устраивается из щебня фракций 5–10 мм.
Однослойная поверхностная обработка с двойным распределением щебня. На слой нанесенного вяжущего сначала рассыпают крупную фракцию щебня (например, 10–15 или 15–20 мм), прикатывают катком, а затем рассыпают более мелкую фракцию щебня (например, 5–10 мм) и уплотняют. Применяется на дорогах с интенсивным движением и высокой скоростью движения. Такая поверхностная обработка способствует улучшенной герметичности покрытия, устранению мелких неровностей и деформаций, лучше распределяет усилия от колес автомобилей. Особенно эффективно такая обработка работает на хорошем жестком основании.
Двухслойная поверхностная обработка. На первый слой разлитого вяжущего рассыпают крупную фракцию щебня и уплотняют. Затем разливают второй слой вяжущего, рассыпают более мелкую фракцию щебня и окончательно уплотняют. Применяется на покрытиях с недостаточной прочностью, при наличии сетки трещин, ямочности, колей, при высокой интенсивности движения, т.е. в тех случаях, когда необходимо не только создать шероховатый слой износа и защитный слой, но и улучшить ровность, несколько повысить прочность и сдвигоустойчивость. Применяется также на цементобетонных покрытиях.
Поверхностная обработка типа «сэндвич». На покрытие рассыпают щебень более крупной фракции, затем распределяют вяжущее, рассыпают щебень мелкой фракции и уплотняют. Структура получаемого слоя поверхностной обработки сравнима с однослойной поверхностной обработкой, устроенной путем розлива вяжущего и двойной россыпью щебня. Такая поверхностная обработка рекомендуется при неоднородном по ровности покрытии для его выравнивания и некоторого усиления. Применяется на дорогах второстепенного, местного значения.
При выборе способа устройства поверхностной обработки покрытий необходимо учитывать ее назначение, условия движения на дороге, климатические условия района строительства, показатель твердости дорожного покрытия, наличие материалов и средств механизации.
Технология производства работ
Существует два способа устройства поверхностных обработок:
Традиционный – с раздельным распределением материалов;
способ с синхронным распределением вяжущего и щебня.
Традиционный способ
Работы по устройству одиночной поверхностной обработки традиционным способом с использованием битумов, дегтебитумов, битумо- и дегтеполимерных вяжущих производят в следующем порядке:
розлив вяжущего;
распределение щебня;
укатка;
уход в период формирования.
Работы по устройству двойной поверхностной обработки производят в такой последовательности:
Подготовка поверхности (очистка от пыли и грязи) и ремонтные работы;
первый розлив вяжущего;
первая россыпь щебня;
укатка;
второй розлив вяжущего;
вторая россыпь щебня (между первой и второй россыпью щебня допускается перерыв не более 3–5 суток);
укатка;
уход в период формирования.
Битумощебнераспределитель Chipsealer-19 фирмы Secmair, Франция
Очистку покрытия от пыли и грязи выполняют механическими щетками, наиболее загрязненные участки промывают с помощью поливомоечной машины.
Струны щеток, какова бы ни была их природа (нейлон, сталь), должны быть в хорошем состоянии и достаточно жесткими, чтобы обеспечить эффективное соскабливание.
В случаях, когда старое покрытие не удается полностью очистить от пыли и грязи, оставшихся в мелких трещинах и впадинах, его необходимо подгрунтовать путем розлива жидкого битума по норме 0,3–0,5 л/м2 или битумной эмульсией с расходом 0,5–0,8 л/м2.
Розлив вяжущего производят автогудронатором. Для равномерного розлива вяжущего необходимо обеспечить бесперебойность действия сопел, равномерность работы насоса и требуемую скорость перемещения гудронатора.
Сопла должны быть теплоизолированы и оснащены устройством обогрева, позволяющим поддерживать или обеспечивать определенную температуру вяжущего.
В зависимости от выбранного вяжущего и от ширины обрабатываемой поверхности водитель определяет, с помощью элементов регулировки гудронатора (номограмма, вычислительный диск, программирование), необходимое соотношение между скоростью передвижения и количеством оборотов насоса, который определяет дозирование вяжущего на покрытии. Во время осуществления распределения соотношение между скоростью автомобиля и количеством оборотов насоса поддерживается постоянным, путем, либо автоматического слежения, либо непосредственного считывания шофером показаний тахометра и счетчика оборотов.
Во время розлива температура битума марок БНД 60/90, БНД 90/130, БН 60/90 и БН 90/130 должна составлять 150–160°C; марок БНД 130/200 и БН 130/200 – 100–130°C; температура полимерно-битумного вяжущего – 140–160°C; дегтеполимерного вяжущего – 100–110°C.
Распределение щебня производят самоходным щебнераспределителем, автомобилем-самосвалом с навесным приспособлением или другим механизмом, обеспечивающим быстрое и равномерное распределение щебня. Кузов всех этих механизмов должен быть плоским и без локальных деформаций. Высота сброса щебня должна быть небольшой, чтобы обеспечить более однородное распределение заполнителя на покрытии. Автощебнераспределители могут быть оснащены системой гидравлического расширения, позволяющей изменять без остановки рабочую ширину от 2,50 до 4 м.
Битумощебнераспределитель НР-27 фирмы Savalco
Щебень распределяют непосредственно после розлива вяжущего слоем в одну щебенку и укатывают катком 6–8 т за 4–5 проходов по одному следу.
Уплотнение поверхностной обработки покрытий обеспечивает укладку щебня и его закрепление на покрытии. Пневматические шинные уплотнители великолепно обеспечивают эти функции. Они приспосабливаются к неровностям дороги и не дробят щебень.
В течение первых дней эксплуатации необходимо осуществлять уход за формирующимися слоями. Незакрепившийся щебень должен быть удален с покрытия не позднее чем через 1 сутки после открытия движения. Скорость движения автомобилей ограничивают 40 км/ч и регулируют по ширине проезжей части.
Выброшенный лишний щебень подбирается очистительными машинами-сборщиками, очистительными машинами и втягивающими машинами. Оснащенные различными щетками и всасывающими соплами, они оборудованы сборными емкостями для мелкозернистого материала, который они поднимают. Эти всасывающие механизмы представляют большой прогресс в технологии поверхностных покрытий, поскольку они позволяют значительно снизить самый большой вред от загрязнения: битье ветровых стекол автомобилей после возобновления движения.
Поверхностную обработку с использованием битумных эмульсий выполняют в следующем порядке:
Подготовка поверхности (очистка от пыли и грязи) и выполнение в случае необходимости ремонтных работ;
смачивание поверхности водой (в жаркую сухую погоду);
розлив эмульсии по покрытию в количестве 30% нормы;
распределение щебня в количестве 70% нормы;
розлив оставшейся эмульсии (70%);
распределение оставшегося щебня (30%);
укатка;
уход в период формирования.
Температуру и концентрацию эмульсии устанавливают в зависимости от погодных условий. При температуре воздуха ниже 20°C рекомендуется применять эмульсию с температурой 40–50°C и концентрацией битума 55–60%. Подогрев эмульсии до указанной температуры следует производить непосредственно в автогудронаторе в процессе транспортирования к месту работ. При температуре воздуха выше 20°C эмульсию применяют в холодном состоянии, а концентрацию битума можно снизить до 50%.
Распределение щебня осуществляют таким образом, чтобы щебень распределялся не далее 20 м от автогудронатора, разливающего эмульсию.
Уход за поверхностной обработкой с применением битумных эмульсий выполняется так же, как и при использовании битума. При использовании анионных эмульсий движение автомобилей открывается не ранее чем через 1 сутки после окончания работ.
Технология поверхностной обработки с синхронным распределением вяжущего и щебня
Основным отличием новой технологии устройства поверхностной обработки является синхронное, практически одновременное распределение вяжущего и россыпь щебня (рис. 3).
Поверхностная обработка с синхронным распределением материалов
Рис. 3. Поверхностная обработка с синхронным распределением материалов
При устройстве поверхностной обработки традиционными методами разрыв во времени между распределением вяжущего и россыпью щебня лимитируется временем остывания горячего битума и может достигать 1 часа.
При синхронном распределении вяжущего и щебня разрыв между этими операциями не превышает 1 сек, что существенно сказывается на повышении качества поверхностной обработки, как при использовании в качестве вяжущего горячего битума, так и битумной эмульсии.
Повышение качества при использовании в роли вяжущего горячего битума объясняется тем, что за столь короткий промежуток времени битум не успевает остыть и сохраняет жидкую консистенцию и высокую клеящую способность. В результате битум хорошо проникает в микропоры щебня и покрытия, обволакивает каждую щебенку и прочно приклеивает их к покрытию и одну к другой.
Битумощебнераспределитель Twinsealer фирмы Rincheval (Fayat Group), Франция
Уплотнение уложенного слоя также происходит при горячем состоянии битума, что обеспечивает максимальный эффект уплотнения.
При использовании в роли вяжущего битумной эмульсии высокое качество поверхностной обработки с синхронным распределением вяжущего и щебня объясняется тем, что за столь короткий промежуток времени распад эмульсии только начнется, и эмульсия в жидком состоянии заполнит все микропоры щебня и покрытия, покроет каждую щебенку тонким слоем вяжущего и обеспечит возможность хорошего уплотнения слоя поверхностной обработки.
Синхронное распределение решает все проблемы организации и координации работ, возникающие при асинхронном распределении, поскольку при каждой остановке в распределении щебня автоматически прекращается и распределение вяжущего. Существенно сокращаются простои из-за климатических условий и повышается производительность работ. Это важно при использовании вяжущих высокой вязкости, но особенно важно при работе в неблагоприятных погодных условиях.
Синхронное распределение вяжущего и щебня благоприятно сказывается на формировании сопряжения между вяжущим и щебнем, что гарантирует высокие эксплуатационные характеристики поверхностной обработки, уменьшает риск неудачи работ из-за разницы температур основания и вяжущего, а также из-за наличия сухих тонкодисперсных фракций при устройстве поверхностных обработок с использованием эмульсий.
Битумощебнераспределитель Twinsealer фирмы Rincheval (Fayat Group), Франция
Битумощебнераспределитель Twinsealer фирмы Rincheval (Fayat Group), Франция
Опыт показывает, что высокий уровень качества поверхностной обработки с синхронным распределением вяжущего и щебня позволяет добиться поразительных результатов, когда тонкий слой щебня и вяжущего выдерживает интенсивное воздействие колес автомобилей в течение 10–15 лет.
Таким образом, синхронное распределение вяжущего и щебня с временем задержки в 1 секунду является самым важным нововведением в практике поверхностной обработки за последние 20 лет.
Для реализации идеи поверхностной обработки с синхронным распределением вяжущего и щебня фирма SECMAIR разработала и выпускает широкую номенклатуру битумощебнераспределителей различной производительности, а также других машин для содержания и ремонта дорожных покрытий с использованием щебня, обработанного битумом или битумной эмульсией.
Выпускаемые машины могут работать при движении передним ходом или при движении задним ходом (рис. 4).
Принципы работы машин для поверхностной обработки
Рис. 4. Принципы работы машин для поверхностной обработки
Учитывая значительный интерес российских дорожников к внедрению технологии поверхностной обработки с синхронным распределением вяжущего и битума, французская фирма SECMAIR и ГУП Саратовский научно-производственный центр «Росдортех» создали в г. Саратове совместное производство машин типа Chipsealer.
В 1999 г. начат выпуск следующих машин:
Chipsealer-40. Это высокопроизводительное оборудование, предназначенное для устройства шероховатых поверхностных обработок в больших объемах. Оборудование Chipsealer-40 монтируется на базе полуприцепа Caizer и обладает полностью автономной системой энергообеспечения. За один цикл загрузки кузова щебнем позволяет выполнять поверхностную обработку на полосе шириной 3,75 м длиной до 800 м за 10 минут.
Chipsealer-26 выполнен на базе российского полуприцепа СЗАП – 9905. В качестве автомобиля-тягача могут использоваться седельные тягачи МАЗ и КамАЗ. Имеет такие же характеристики, как и Chipsealer-40, но меньшие габариты кузова для щебня и резервуара для вяжущего.
Chipsealer-19 – предназначен для выполнения ремонта дорожных покрытий и устройства шероховатых поверхностных обработок в небольших объемах.
Машины типа «Стоппер»
Применяются для сдерживания эрозии покрытия на ранней стадии путем устройства местной поверхностной обработки на участках шелушения и выкрашивания покрытия, появления мелких трещин, сетки трещин, мелких выбоин и колей. Машина имеет на одном шасси емкость для вяжущего, кузов для щебня, грейферный ковш для загрузки щебня в кузов и распределительные устройства для нанесения битума и щебня (рис. 5).
Оборудование машины типа "Стоппер"
Рис. 5. Оборудование машины типа «Стоппер»
1 – теплоизолированный бак для вяжущего;
2 – грейферный ковш для погрузки щебня;
3 – кузов для щебня;
4 – площадка оператора;
5 – распределитель вяжущего;
6 – распределитель щебня;
7 – пневматический каток;
8 – направление движения
Еще одним отличием является наличие у «Стоппера» уплотняющего блока из 8 пневматических гладких колес, которые при помощи 4 гидравлических домкратов опускаются на поверхность в рабочее положение и поднимаются вверх в транспортное положение. Это особенно важно для ускоренного формирования ремонтного слоя в холодном и влажном климате. В сухом и жарком климате указанное формирование происходит под действием движущегося транспорта, и необходимость в уплотняющем блоке отпадает. Кроме того, «Стопперы» приспособлены для проведения локального ремонта с применением поверхностной обработки.
Машины для устройства поверхностной обработки
Для устройства поверхностной обработки традиционным способом, т.е. с раздельным распределением вяжущего и щебня, используют автогудронаторы и распределители щебня.
Автогудронаторы различают и выбирают по:
Вместимости цистерны (грузоподъемности);
ширине распределения вяжущего; при этом, как правило, выбирают ширину распределения равной ширине полосы движения дороги или на 5–10 см меньшую.
Распределители щебня различают по:
Вместимости (емкости) бункера для щебня;
ширине распределения щебня; при этом, как правило, ширину распределения щебня принимают равной ширине распределения вяжущего;
типу хода (движения): прицепные и навесные базовые машины. Как правило, в качестве базовых машин для прицепных и навесных распределителей щебня используют автомобили-самосвалы.
Для устройства поверхностной обработки методом синхронного (одновременного последовательного) распределения вяжущего и щебня используют битумо-(эмульсие)-щебнераспределители.
Битумощебнераспределители различают по:
Ширине обработки, т.е. по соответствию (кратности) этого параметра ширине проезжей части автомобильной дороги;
емкости (вместимости) бака для вяжущего и бункера для щебня;
методу загрузки щебнем, т.е. использованию специальных загрузочных машин для загрузки щебня в бункер или специального самозагрузочного оборудования.
Рис. 6. Выработка машин по загрузке эмульсией и щебнем
На рис. 6 представлены графики выработки (в тыс. м2) всех трех типов машин: автогудронаторов, распределителей щебня и битумо-(эмульсие)-щебнераспределителей при норме розлива битумной эмульсии в 1,4 и 2,1 л/м2 и норме распределения щебня в 10,0 и 15,0 кг/м2. В зависимости от ширины розлива вяжущего и распределения щебня на рис. 6 представлены также выработка в пог. м полосы обработки.
Представленные графики с учетом величин вместимости бака для вяжущего и бункера для щебня и битумощебнераспределителей показывают, что вместимость бака для вяжущего обеспечивает значительно большую выработку, чем вместимость бункера для щебня. Таким образом, бункер для щебня должен быть заполнен несколько раз для обеспечения выработки вяжущего. Соотношение выработок по вяжущему и щебню для различных битумощебнераспределителей колеблется от 2,0 до 9,5. Поэтому значительное влияние на сменную выработку (производительность) оказывает метод загрузки щебня.
Совместная работа автогудронатора и прицепного щебнераспределителя ЗАО "Бецема", загружаемого из самосвала
Совместная работа автогудронатора и прицепного щебнераспределителя ЗАО «Бецема», загружаемого из самосвала
При загрузке щебня в бункер щебнераспределителя (без самозагрузки) на базе с использованием одноковшового фронтального погрузчика или крана с грейфером (челюстным ковшом), т.е. с двойным пробегом от места работы до базы и обратно, затраты времени на одну загрузку составляют от 40 минут до 1 часа 20 минут.
При загрузке щебня в бункер битумощебнераспределителя на месте работ с использованием самозагрузки или с использованием автомобиля-самосвала с краном-манипулятором, оснащенным грейфером, затраты времени на одну загрузку составляют от 10 до 15 минут.
При загрузке щебня в бункер битумощебнераспределителя с самозагрузкой из приемного бункера, расположенного сзади машины и загружаемого из автомобиля-самосвала, даже при остановке битумощебнераспределителя, затраты времени на одну загрузку составляют от 2 до 6 минут.
При расчете загрузка вяжущего совмещена с загрузкой щебня, т.е. производится через две–девять загрузок щебня, скорость движения битумощебнераспределителя принята равной 4 км/ч = 1,1 м/сек = 66 м/мин., ширина распределения принята равной 3 м, коэффициент использования по времени принят равным 0,8 (при загрузке на базе) и 0,6 (при загрузке на дороге), что связано с необходимостью и большой сложностью ритмичной подачи материалов, применением дополнительных машин (автомобилей-самосвалов, автобитумовозов).
ТЕХНОЛОГИИ ПРОИЗВОДСТВА ВЫСОКОКАЧЕСТВЕННОГО ЩЕБНЯ
Технологии производства высококачественного щебня
Щебень – наиболее широко используемый продукт добычи и переработки нерудных строительных материалов.
Объемы производства щебня в мире превышают 3 млрд. м3 в год. Интересной особенностью щебня как продукта, производимого из природного минерального сырья, является то, что цены на него во всем мире за последние 50 лет выросли в 2,5–3 раза. В то же время цены на большинство продуктов, производимых на базе минерального сырья (например, черные и цветные металлы), за это же время упали в 3–5 раз.
Кажущаяся простота производства щебня – дробление горных пород – обманчива, так как современные технологии производства строительных материалов и изделий на их основе предъявляют все более высокие требования к качеству щебня, используемого, в основном, как заполнитель при производстве бетонов, асфальтобетонов и дорожных покрытий .
Щебень для дорожного строительства
Щебень является одним из основных материалов, применяющихся для строительства, ремонта и содержания автомобильных дорог. От его качества в значительной мере зависят их потребительские свойства (ровность, коэффициент сцепления и т.д.) и долговечность. Особенно это относится к щебню, применяемому для устройства верхних слоев дорожной одежды, непосредственно воспринимающих высокие механические нагрузки от движущегося транспорта, находящихся под воздействием природных факторов и антигололедных химических средств.
Щебень, применяемый в дорожном хозяйстве, условно можно разделить на три группы:
Щебень для устройства оснований дорожных одежд (любые, но преимущественно осадочные скальные и рыхлые горные породы с крупностью фракций 5–20, 20–40, 40–70, 0–40, 0–70 мм);
щебень для нижних слоев покрытий (метаморфические и магматические горные породы с крупностью фракций 5–20 и 20–40 мм);
щебень для верхних слоев покрытий из асфальтобетонных смесей типа А и поверхностной обработки (магматические и частично метаморфические горные породы крупностью щебня от 5 до 20 мм) с содержанием зерен пластинчатой (лещадной) и игловатой формы не более 15% (группа 1 по ГОСТ 8267-93), который принято называть «кубовидным».
Общий объем производства каменных материалов (щебень, гравий, песок) в России в настоящее время составляет примерно 140 млн м3 в год, причем примерно половина этого количества используется в дорожном строительстве.
За последние годы сформировался устойчивый спрос на щебень кубовидной формы со стороны дорожно-строительных организаций, но эта потребность в РФ сейчас удовлетворяется только на 30–40%.
В соответствии с президентской программой «Дороги России XXI века» СоюздорНИИ был произведен расчет потребности в дорожно-строительных материалах, в том числе в различных видах щебня. В таблице 1 приведена потребность в щебне узких фракций кубовидной формы из магматических горных пород для различных регионов России.
Наименование региона Значение потребности по годам и периодам
2001 г. 2002 г. 2003 г. 2004 г. 2005 г. 2001–05 гг. 2006–10 гг. 2011–20 гг. 2001–20 гг.
Центр 2,3 2,4 2,5 2,6 2,7 12,5 25,8 96,6 134,9
Северо-Запад 1,1 1,1 1,2 1,2 1,3 5,9 10,6 38,88 55,3
Поволжье 1,7 1,8 1,9 1,9 2 9,3 16,2 70,3 95,8
Северный Кавказ 0,6 0,6 0,6 0,7 0,7 3,2 7,7 23,7 34,6
Урал 1,5 1,6 1,6 1,6 1,7 8 14,4 52,9 75,3
Сибирь 1,4 1,4 1,4 1,6 1,7 7,5 15,5 57,7 80,7
Дальний Восток 0,7 0,7 0,8 0,8 0,8 3,8 6,7 30 40,5
Всего щебня: 9,3 9,6 10 10,4 10,9 50,2 96,9 370 517,1
В среднем за год по периодам: 10 19,4 37 25,8
Таблица 1
Потребность в щебне узких фракций кубовидной формы (млн м3) для развития сети автомобильных дорог по регионам России (2001 – 2020 гг.)
В настоящее время протяженность сети дорог общего пользования с твердым покрытием в России составляет около 600 тыс. км, и основная часть щебня кубовидной формы будет использована на их ремонт и содержание. Наибольшее количество всех видов щебня будет потребляться в Центральном регионе, где дорожное строительство ведется наиболее интенсивно.
Современная практика показывает, что щебень из магматических горных пород для дорожного строительства в нашей стране производится в основном на стационарных дробильно-сортировочных заводах, расположенных вблизи месторождений, главным образом на северо-западе России и на Урале.
Мобильная камнедробильная установка для получения кубовидного щебня на площадке ООО "ЭнСиСи Индустри" (Санкт-Петербург)
Мобильная камнедробильная установка для получения кубовидного щебня на площадке ООО «ЭнСиСи Индустри» (Санкт-Петербург)
Анализ продукции, выпускаемой предприятиями нерудной промышленности, разрабатывающими месторождения магматических горных пород, показывает, что они в основном производят щебень в виде фракций 5–20 мм и 20–40 мм, в отдельных случаях – фракций 5–10, 10–20 и 5–15 мм. К щебню фракции 5–20 мм, используемой для приготовления асфальтобетонных смесей для верхних слоев покрытий, имеются серьезные претензии со стороны дорожно-строительных организаций.
Производимый щебень фракции 5–20 мм обычно сильно закрупнен. Это не позволяет подобрать оптимальный зерновой состав минеральной части асфальтобетонных смесей, что существенно ухудшает физико-механические характеристики асфальтобетона. Исследования СоюздорНИИ, а также отечественный и зарубежный опыт строительства и эксплуатации автомобильных дорог позволили установить, что щебень для приготовления асфальтобетонных смесей для верхних слоев покрытий должен выпускаться в виде узких фракций (5–10, 10–15, 15–20 мм). Из узких фракций сравнительно просто подобрать требуемые смеси оптимального зернового состава.
Поставляемый щебень фракции 5–20 мм в большинстве случаев содержит чрезмерное количество зерен лещадной формы – 25–40% и более. Повышенное их содержание отрицательно влияет на удобоукладываемость и плотность асфальтобетонных смесей. Они обладают меньшей механической прочностью по сравнению с кубовидными и поэтому в процессе строительства и при эксплуатации дорог разрушаются, что может приводить к образованию поверхностей, не покрытых битумом. Эти места являются первичными очагами разрушения асфальтобетона при проникновении воды и действии затем попеременного замораживания-оттаивания.
Асфальтобетонные смеси на кубовидном щебне (группа I) обладают лучшей уплотняемостью по сравнению с щебнем групп II и V за счет взаимного перемещения и взаимозаклинивания зерен.
В связи с этим действующая нормативно-техническая документация ограничивает содержание в смесях зерен лещадной формы: 15% - для смесей типа А, 25% – типа Б, 35% - для смесей типа В.
Особенно отрицательно действие зерен лещадной формы проявляется при поверхностной обработке асфальтобетонных покрытий с использованием фракционированного щебня, когда при укладке материала разрушается большая часть таких зерен. В этом случае их содержание в щебне не должно превышать 10%.
Отрицательное воздействие на свойства асфальтобетона оказывает и повышенное количество пылевато-глинистых примесей, которые препятствуют контакту битума с поверхностью щебня. Поэтому их содержание не должно превышать: 1% – для приготовления асфальтобетонной смеси; 0,5% – для поверхностной обработки.
Дробильно-сортировочная установка с дробилкой КИД-900 на Абзаковском карьере
При формировании структуры асфальтобетона щебень является главным компонентом, определяющим устойчивость минерального остова. Лабораторными исследованиями установлено, что коэффициент внутреннего трения tg ц зависит от зернового состава асфальтобетона. На него практически не влияет вязкость применяемого битума и асфальтового вяжущего вещества. В асфальтобетонах с остаточной пористостью 3,0–3,5% коэффициент внутреннего трения возрастает при увеличении содержания кубовидных зерен щебня.
Высокие показатели внутреннего трения обеспечивают плотные асфальтобетоны типа А на основе дробленых каменных материалов и специальные многощебенистые составы, например щебеночно-мастичный асфальтобетон (ЩМА) по ТУ 5718.030.01393697-99.
В щебеночно-мастичных асфальтобетонных смесях высоко содержание прочного фракционированного щебня (70–80%) с улучшенной (кубовидной) формой зерен, что создает устойчивый каркас. Повышенное содержание минерального активированного порошка (8–15%) и битумного вяжущего (не менее 5,5%) значительно уменьшает количество пустот в уплотненном слое покрытия. Для структурирования и стабилизации битумного вяжущего рекомендуется вводить специальные стабилизирующие добавки, например волокна.
Структура ЩМА оптимально сочетает максимальную жесткость минерального остова и высокую пластичность асфальтового вяжущего. Повышенное содержание прочного кубовидного щебня призвано обеспечивать высокое сцепление с колесом автомобиля, шероховатость, сдвигоустойчивость и износостойкость покрытия, а увеличенное количество асфальтового вяжущего вещества (мастики) – повышать водо- и морозостойкость, водонепроницаемость, устойчивость к деформациям и усталостную стойкость защитного слоя. При устройстве шероховатых покрытий важно обеспечить повышенные требования к свойствам каменных материалов. Щебень должен быть изготовлен из горных пород, обладающих высокой износостойкостью, иметь кубовидную форму, быть однородным по прочности, трудношлифуемым и не иметь загрязняющих примесей. Содержание зерен лещадной формы в нем должно быть ограничено. Щебень должен обладать хорошо выраженной шероховатостью естественного скола, поэтому предпочтение отдается горным породам зернистой кристаллической структуры, а также породам, способным оставаться шероховатыми за счет компонентов разной твердости согласно ВСН 73-67.
Комплектная технологическая линия на основе дробилки КИД-1200М на ОАО "Павловскгранит", Воронежская область
Комплектная технологическая линия
на основе дробилки КИД-1200М на ОАО «Павловскгранит», Воронежская область
Для реконструкции Московской кольцевой автомобильной дороги (МКАД) АО «Центродорстрой» были использованы три дробильно-сортировочные установки фирмы «Сведала» и налажено производство улучшенного щебня из габбро-диабаза. Получаемый щебень фракции 5–10 и 10–15 мм с лещадностью менее 15% применяли в асфальтобетонной смеси типа А на полимерно-битумном вяжущем для устройства верхнего слоя покрытия взамен ранее использовавшегося гранитного щебня фракции 5–20 мм. По результатам контроля качества верхнего слоя покрытия МКАД можно судить о влиянии качества щебня на свойства асфальтобетона.
Асфальтобетонное покрытие стало более сдвигоустойчивым, хотя максимальная крупность применяемого в смеси щебня была снижена с 20 до 15 мм. Среднее значение угла внутреннего трения повысилось примерно на 1,5°, а разброс этого показателя снизился почти в 2 раза. Среднее сопротивление сдвигу при расчетных условиях для МКАД возросло с 0,789 до 0,840 МПа. При этом стандартный показатель прочности при сжатии при 50°С повысился в среднем на 0,3 МПа, а его вариация не превысила 12%.
Применение более качественного щебня в асфальтобетоне позволило снизить вероятность образования колеи в верхнем слое покрытия даже в форс-мажорных случаях колонного движения и заторов автомобилей.
Щебень для производства бетонов
Щебень как крупный заполнитель бетонов, образуя жесткий скелет, увеличивает его прочность и модуль деформации, уменьшает ползучесть, усадку, повышает его долговечность, сокращает расход цемента.
Мелкий заполнитель – песок – оказывает влияние на реологические свойства бетонной смеси – вязкость, предельное напряжение сдвига бетона, а также на его плотность.
Форма зерен крупного заполнителя непосредственно влияет на удобоукладываемость бетонной смеси. Кроме этого, щебень с зернами плоской (лещадной) или игловатой формы имеет значительно большую пустотность, чем щебень с зернами кубовидной формы. По данным ВНИИЖелезобетона, объемный насыпной вес щебня с содержанием зерен плоской и игловатой формы до 15% ниже, чем щебня с зернами кубовидной формы.
Объемный насыпной вес щебня, состоящего полностью из зерен плоской или игловатой формы, на 9–10% ниже, чем щебня с зернами кубовидной формы. Указанные факторы вызывают увеличение расхода цемента. Поэтому, хотя форма зерен крупного заполнителя, по данным ряда исследований, не оказывает значительного влияния на прочность бетона, ей должно быть уделено серьезное внимание.
В щебне для дорожного бетона содержание зерен плоской и игловатой формы допустимо до 25%, для асфальтобетона - до 15%, для оснований дорог (необработанных) – до 25%.
Следует отметить, что принятое ограничение содержания в щебне зерен плоской и игловатой формы с отношением большего и меньшего размеров выше 3 не полностью характеризует форму зерен. В этой связи представляет интерес принятая в некоторых зарубежных стандартах оценка формы зерен по так называемому «индексу формы», то есть среднему отношению наибольшего и наименьшего размеров зерен пробы. Такая оценка позволяет судить о форме всего количества зерен щебня.
По бельгийскому стандарту NB № 329, 1962 щебень подразделяется на три категории: обычный, недодробленный и передробленный кубической формы (табл. 2).
Размер фракций в мм Категория щебня
обычный недодробленный передробленный кубической формы
8–16; 8–12; 12–16 0,275 0,39 0,45
16–22 0,275 0,425 0,485
22–40 0,35 0,425 –
40–63 0,35 – –
Таблица 2
Наименьшие значения «индекса формы» для различных категорий щебня (по бельгийскому стандарту NB № 329, 1962)
Как видно из данных таблицы, к обычному щебню практически не предъявляются требования к форме зерен (он может быть отнесен к щебню плоской и игловатой формы по нашим стандартам), но к щебню более высоких категорий требования к форме зерен довольно жесткие.
В ряде работ отмечается отрицательная роль плоских и удлиненных заполнителей, применение которых снижает прочность и повышает расход цемента, а также ухудшает морозостойкость бетона. С учетом этого при строительстве бетонного полотна автомобильных дорог должно быть обеспечено отсутствие в щебне кусков лещадной и игловатой формы, исходя из того, что бетонная смесь с такими заполнителями становится неудобоукладываемой, плохо уплотняется и в бетоне остаются раковины, борьба с которыми требует увеличения расхода цемента.
Для проверки влияния на параметры бетона наличия в щебне кусков лещадной формы в институте ВНИИЖелезобетон были выполнены исследования. В опытах использовался щебень из природных горных пород. Результаты показали, что прочность бетона по мере увеличения в щебне содержания кусков лещадной формы (до 50 и 100%), как правило, снижается с одновременным снижением объемного веса бетона, то есть при недоуплотнении бетонной смеси. Наличие в большом количестве (более 50%) щебня лещадной формы затрудняло уплотнение бетона, а это приводило к снижению прочности.
Отрицательное воздействие наличия в щебне более 50% кусков лещадной формы объясняется укладкой щебня в основном плашмя, черепицеобразно, что затрудняет взаимное скольжение смежных кусков и требует увеличения мощности вибрационного оборудования.
Сравнительные физико-механические свойства щебня различной лещадности приведены в табл. 3.
Свойства Щебень лещадный Щебень кубовидный
Содержание зерен лещадной и игловидной формы, % 89 0
Предел прочности при сжатии в водонасыщенном состоянии (в цилиндре), МПа 40–60 120
Дробимость при сжатии в цилидре,% 15–22 2–5
Показатель сопротивления щебня удару на копре ПМ 41–152 120–370
Износ в полочном барабане, % 18–29 15–20
Морозостойкость, марка 25 300
Таблица 3 Физико-механические свойства щебня различной лещадности
Щебень для балластного слоя на железнодорожных путях
Основным назначением балластного слоя является обеспечение вертикальной и горизонтальной устойчивости рельсошпальной решетки при динамических нагрузках.
Характер упрочнения балласта в процессе укладки и эксплуатации путей существенно зависит от начальной пустотности щебеночного каркаса, то есть от состава и формы зерен щебня. Предельная пустотность щебеночного балласта составляет 0,33–0,34, а начальная достигает 0,45–0,50, что вызвано в значительной степени наличием лещадных зерен. Лещадные и игловатые зерна ломаются под нагрузкой и повышают неравномерность осадки балласта при эксплуатации.
Отечественные стандарты на щебень для балласта требуют получения двух фракций – 25–60 мм и 5–25 мм, причем содержание зерен крупнее верхнего предела и менее нижнего предела не должно превышать 5%.
Повышение скорости движения поездов вызвало изменение требований к балласту, особенно по его горизонтальной устойчивости. В результате в отечественные стандарты было внесено требование по обеспечению кубовидности щебня – ограничение содержания лещадных зерен 18%.
Европейские стандарты также требуют ограничения лещадности щебня, используемого для железных дорог, на уровне 15–20%.
Технологии и оборудование для производства высококачественного щебня
При производстве щебня кубовидной формы необходимо учитывать, что форма зерен дробленого материала определяется текстурно-структурными особенностями исходной горной породы, используемым оборудованием и технологией переработки.
Форма зерен щебня зависит также от принципа работы дробильного агрегата. Оптимальная изометричная кубообразная форма создается в агрегатах ударного действия – молотковых, ударно-центробежных и отбойно-центробежных дробилках. Из раздавливающих камень агрегатов (щековые, валковые, стандартные конусные дробилки) получают щебень с высоким содержанием зерен лещадной и игловатой формы. Так, при дроблении песчаников в отбойно-центробежной дробилке ОЦД-100 лещадные и игловатые зерна составили 9–13% во фракции 5–10 мм и всего 4,6–5,3% – во фракции 10–20 мм, в то время как щебень из конусной дробилки СМ-561 содержал соответственно 53–55% и 39–50% таких зерен. В гранитном щебне из дробилки ОЦД-100 лещадных и игловатых зерен было только 6 и 2%, а в щебне из дробилки СМ-561 – соответственно 23 и 14%, т. е. в 4–7 раз больше.
Для получения щебня кубовидной формы обычно применяют специальные конусные дробилки или дробилки ударного действия. Последние позволяют получать щебень, форма зерен которого близка к кубовидной, но иногда и к окатанной, кроме того, они являются дорогими в эксплуатации и характеризуются повышенным выходом отсевов дробления.
Некоторого снижения содержания зерен лещадной формы в щебне можно добиться и при использовании стандартных конусных дробилок. Для этого необходимо, чтобы в процессе работы была полностью заполнена камера дробления. При этом измельчение происходит не только между конусами дробилки, но и между зернами материала, находящимися в камере (дробление «в слое» или «в стесненных условиях»). В таком случае имеющиеся в исходном материале и образующиеся в процессе дробления зерна лещадной формы, как механически наиболее слабые, разрушаются. Для осуществления этого процесса дробилка должна быть оборудована более мощным электродвигателем, датчиком уровня материала в камере дробления, а также аккумулирующим бункером с питателем.
Технология Стандартная конусная дробилка под завалом Стандартная конусная дробилка под завалом в замкнутом цикле Роторная молотковая дробилка Роторная центро-бежная дробилка Конусная вибро-инерционная дробилка
Обеспе-чиваемая лещадность, % 25–40 15–30 10–20 5–15 10–15
Степень дробления 2,5–4 3–5 4–6 2–3 4–10
Диапазон крупности, мм питание 80 80 100 40–60 60–270
Диапазон крупности, мм готовый м-л 25 20 20 20 15–60
Выход отсева (?5мм) низкий высокий высокий высокий средний
Удельная металло-емкость средняя высокая низкая низкая высокая
Удельная энергоемкость низкая средняя высокая средняя низкая
Примечания Резко возрастают транспортные потоки, снижение производи-тельности дробилки по готовому продукту Применение только на малопрочных неабразивных материалах Требует сравнительно мелкое питание Степень дробления может регулироваться без остановки машины
Таблица 4
Сравнительная характеристика различных технологий получения кубовидного щебня
В таблице 4 приводятся данные по применению различных типов дробильных агрегатов для производства щебня. На основании их анализа можно сделать заключение, что для получения кубовидного щебня необходимо обеспечить многократное дробящее воздействие на кусок породы, а разрушающая сила должна действовать не на раздавливание, а на сдвиг.
Основываясь на этих принципах, способы производства кубовидного щебня могут быть следующими (табл. 4):
Использование стандартных конусных дробилок, работающих «под завалом» в замкнутом цикле;
использование роторных молотковых дробилок;
использование роторных центробежных дробилок;
использование дробилок, обеспечивающих многократное сдвиговое воздействие на дробимую породу – конусных виброинерционных дробилок.
Использование ударных и отражательных дробилок, в конечном счете, может рассматриваться как дополнительная операция дробления, назначение которой – исправление формы зерен без существенного сокращения размеров дробимого материала.
Дробильный комплекс фирмы Zeppelin
Дробильный комплекс
фирмы Zeppelin
Центробежные дробилки ударного типа с небольшими конструктивными отличиями изготавливают как в России, так и за рубежом. В России – это ассоциация «Урал-Центр», ЗАО «Новые технологии», ОАО «Дробмаш». За рубежом – фирма «Metso Minerals» (Финляндия), KRUPP, MARTIN STECKERT, FORSTER, SPILLE (Германия) и другие.
Центробежные дробилки-грануляторы могут принимать максимальный кусок не более 60–70 мм (лучше 40 мм) и производить кубовидный щебень фракции 5–20 мм с производительностью по питанию до 200 т/ч и выходом фракции менее 5 мм 35–50%.
По данным предприятия «Урал-Центр» назначение их дробилок – «последняя стадия дробления в трех- или четырехстадийных схемах дробления, определяющая качество конечного продукта. Максимальный линейный размер куска питания не должен превышать 70 мм. Питанием дробилки ДЦ является продукт конусных дробилок КСД или КМД согласно технологической схеме с контрольным грохочением по классу – 40 мм», то есть она фактически передрабливает горную массу крупностью менее 40 мм.
Разрушение дробимого материала «в слое» применительно к конусным дробилкам – сравнительно новый технологический метод, разработка которого принадлежит отечественной школе дезинтеграции.
Специалистами «Механобра» разработаны новые образцы дезинтегрирующего вибрационного оборудования, обеспечивающие принудительное самоизмельчение материала внутри собственного слоя под воздействием виброимпульсного сжатия с одновременным сдвигом при дозировании силы воздействия на слой материала по величине предела прочности дефектных поверхностей его структуры. Реализация таких принципов рационального разрушения осуществляется в конусных инерционных дробилках (КИД) и виброщековых дробилках (ВЩД).
1. Срок службы дорог, построенных на кубовидном щебне в 2–2,5 раза больше, чем на щебне игловатой и пластинчатой формы. Кубовидный щебень образует устойчивую трехмерную структуру дорожного полотна, требует меньшего расхода вяжущих – цемента или битума. Лещадные частицы в процессе уплотнения ломаются, образуя «островки» лещадных зерен, что является причиной локальных разрушений дорожных покрытий.
2. Прочность бетона при использовании кубовидного щебня возрастает на 5–10% при одновременном уменьшении расхода цемента на 7–12% и снижении на 3–5% водопотребности бетонной смеси.
3. Стандартные щековые и конусные дробилки не обеспечивают получение щебня необходимой формы.
4. Ударно-центробежные дробилки-грануляторы обеспечивают снижение содержания лещадных зерен в дробленом щебне до требований стандартов, но могут быть использованы как дополнительная стадия дробления – «кубикатор».
5. Конусные инерционные дробилки обеспечивают получение кубовидного щебня в широком диапазоне крупности при минимальном числе стадий дробления.
АСФАЛЬТОБЕТОННЫЕ ЗАВОДЫ И ТЕХНОЛОГИЧЕСКОЕ ОБОРУДОВАНИЕ ДЛЯ ИХ ОСНАЩЕНИЯ
Асфальтобетонные заводы (АБЗ) являются основными производственными предприятиями дорожного хозяйства и предназначены для приготовления различных асфальтобетонных смесей для строительства, реконструкции и ремонта слоев асфальтобетонного покрытия
Однако перечень выполняемых на АБЗ технологических операций, а следовательно и номенклатура технологического оборудования АБЗ, значительно шире просто комплекса операций по приготовлению смесей и перечня необходимого дляприготовления их оборудования.
Перечень технологических и обеспечивающих операций включает:
Технологические операции (комплекс операций) по приготовлению смесей, включая предварительное дозирование минеральных материалов, нагрев и сушку минеральных материалов, сортировку (грохочение) и кратковременное хранение нагретых каменных материалов, точное дозирование минеральных материалов, битума или другого специального вяжущего, минерального порошка и добавок, смешение составляющих в мешалке и выгрузка из мешалки готовой (товарной) асфальтобетонной смеси;
технологические операции по приему, хранению и подаче в бункеры по фракциям каменных материалов, а при необходимости получение на АБЗ необходимых по крупности фракций щебня и песка путем дробления и сортировки более крупных фракций щебня;
технологические операции по приему, хранению, нагреву и подаче в дозаторы битума;
технологические операции по приему, хранению и подаче в дозатор минерального порошка (заполнителя);
технологические операции по приему, хранению, нагреву и подаче в дозатор поверхностно-активных веществ (ПАВ);
технологические операции по складированию, кратковременному хранению и отгрузке готовой асфальтобетонной смеси.
Для выполнения всего комплекса технологических операций в состав АБЗ входит следующее технологическое оборудование:
Асфальтосмесительные установки;
приемные устройства для каменных материалов, площадки для их хранения и машины для их подачи в бункеры асфальтосмесительных установок;
приемные устройства для битума, хранилища (емкости) для битума, битумонагревательное оборудование, битумные насосы;
приемные устройства и площадки для бочек с ПАВ или емкости для ПАВ, нагреватели для ПАВ и насосы для их подачи к смесителю;
приемные устройства и емкости для хранения минерального порошка и насосы (пневмосистемы) для подачи его к смесителю;
загрузочное устройство (скип или элеватор) готовой смеси, бункеры-накопители готовой смеси;
дробильно-сортировочное оборудование для получения требуемых фракций щебня и песка.
Схема асфальтосмесительной установки непрерывного действия
1. Бункеры-дозатор
2. Сборный конвейер
3. Конвейер с контролем влажности
4. Сушильно-смесительный барабан
5. Дозатор и подача старого асфальтобетона
6. Смесительная зона
7. Бункер ожидания скипа
8. Пылесос-вентилятор
9. Накопительный бункер
10. Кабина управления
11. Силос минпорошка
12. Бункер старого асфальтобетона
13. Конвейер с контролем влажности
15. Пылеуловитель и силос пыли
16. Битумный бак-цистерна
17. Нагреватель масла
18. Конвейер сушильного барабана
Помимо основного технологического оборудования в состав АБЗ могут входить:
Оборудование для приготовления и хранения битумных эмульсий;
хранилища топлива (газа, дизтоплива или мазута);
постройки административно-бытового назначения;
объекты электроэнергетического обеспечения;
котельные;
компрессорные станции;
водопроводное хозяйство;
сети электро-, тепло- и водоснабжения;
лаборатория;
ремонтная мастерская;
материально-технический склад.
АБЗ различают:
По типу размещения: на прирельсовые и притрассовые (приобъектные);
по длительности работы на одном месте: на стационарные, инвентарные (перебазируемые) и передвижные (часто перебазируемые);
по количеству и суммарной производительности асфальтосмесительных установок.
Прирельсовые АБЗ сооружают непосредственно у железнодорожной ветки, по которой поступают все или большинство исходных материалов: щебень, песок, битум, минеральный порошок, ПАВ и топливо.
Притрассовые АБЗ сооружают непосредственно вблизи от строящейся автомобильной дороги с целью сокращения дальности и времени транспортирования готовой асфальтобетонной смеси. Все исходные материалы и топливо доставляют автомобильным транспортом с прирельсовых базисных складов или непосредственно с предприятий их производящих: с карьеров каменных материалов и песка, заводов по производству битума и минерального порошка.
Стационарные АБЗ сооружают, как правило, неразборными и рассчитывают на эксплуатацию на одном месте до 10 лет и более.
Инвентарные АБЗ сооружают разборными и рассчитывают на эксплуатацию на одном месте в течение 2–4 лет.
Передвижные АБЗ сооружают разборными и рассчитывают на эксплуатацию на одном месте до 1 года.
Количество смесительных установок на АБЗ колеблется в пределах от 1 до 6. На стационарных АБЗ, как правило, от 2 до 6, а на инвентарных и передвижных от 1 до 2.
С учетом вышесказанного ниже рассматриваются основные технологические комплексы оборудования для приготовления, хранения и отгрузки асфальтобетонной смеси.
По принципу действия асфальтобетонные установки подразделяются на циклические (периодического действия) и непрерывные (непрерывного действия).
С бункером-накопителем под смесителем
Классические схемы асфальтосмесительных установок циклического действия
1. Бункеры-преддозаторы
2. Сборный конвейер
3. Конвейер сушильного барабана
4. Сушильный барабан
5. «Горячий» элеватор
6. Смесительная башня
7. Накопительный бункер
8. Элеватор минпорошка
9. Силос минпорошка
11. Пылеуловитель и силос пыли
12. Пылесос-вентилятор
13. Битумный бак-цистерна
14. Нагреватель масла
15. Кабина управления
С загрузкой автомобилей-самосвалов из отдельного бункера-накопителя
С загрузкой автомобилей-самосвалов
из отдельного бункера-накопителя
С загрузкой автомобилей из смесителя и отдельного бункера-накопителя
С загрузкой автомобилей из смесителя
и отдельного бункера-накопителя
Технология циклического приготовления асфальтобетонных смесей (классическая технология) включает:
Хранение небольшого запаса минеральных материалов (песка и щебня) в бункерах-преддозаторах и предварительное дозирование влажных щебня и песка;
нагрев и сушку минеральных материалов в сушильном барабане;
сортировку (рассев) нагретых минеральных материалов по фракциям и складирование в «горячих» бункерах;
дозирование нагретых минеральных материалов по фракциям на весовой площадке и подача в смеситель;
нагрев минерального порошка в теплообменнике;
дозирование минерального порошка на весовой площадке (или в отдельном дозаторе) и подача в смеситель;
«сухое» (без вяжущего) перемешивание минеральных материалов в смесителе;
нагрев вяжущего (битума или ПБВ) в рабочей емкости;
дозирование вяжущего и подача в смеситель;
«мокрое» (с вяжущим) перемешивание компонентов в смесителе;
выгрузка готовой смеси в кузов транспортного средства или через подъемное устройство («горячий» элеватор или скиповый подъемник) в бункер-накопитель готовой смеси;
С учетом того, что асфальтобетонная смесь является комплексным многокомпонентным материалом, меняющим свойства при изменении состава, все технологические операции (переделы) оказывают значительное влияние на конечные свойства асфальтобетона в покрытии.
Асфальтобетонный завод непрерывного действия Retroflux (Ermont, Франция)
Особо важными параметрами технологических операций, оказывающих влияние на свойства конечного продукта – асфальтобетонной смеси, являются:
Точность предварительного дозирования минеральных материалов, т.к. уменьшение и увеличение дозировки даже одного компонента приводит в итоге к недостатку и переизбытку этого компонента в «горячих» бункерах; обеспечение этого параметра решается путём: повышения точности дозирования, а также введением в систему автоматического управления (АСУ) блока контроля уровня минеральных материалов в «горячих» бункерах.
Температура минеральных материалов на выходе из сушильного барабана, т.к. низкая и высокая температура минеральных материалов приводит к снижению качества смеси: при низкой температуре часть влаги остается на зёрнах минерального материала и ухудшает сцепление битума с поверхностью зёрен, а при высокой температуре зёрен минерального материала происходит окисление битума на поверхности этих зёрен, что меняет его свойства; обеспечение этого параметра решается введением в систему автоматического управления (АСУ) блока контроля температуры минеральных материалов и блоков регулирования мощности горелки сушильного барабана и суммарной производительности преддозаторов.
Температура и режим нагрева органического вяжущего – битума, т.к. высокая температура битума может привести к изменению его свойств, а низкая температура битума ухудшает процесс обволакивания зёрен минерального материала, а резкий режим нагрева битума (высокая температура теплоносителя) также приводит к изменению его свойств; обеспечение этих параметров решается введением в АСУ блоков контроля температуры битума и температуры теплоносителя, а также блока регулирования мощности горелки нагревателя теплоносителя (электронагревателя) битума.
Точность дозирования минеральных материалов, минпорошка и битума, т.к. отклонение от заданного состава смеси является главной причиной получения некачественной смеси; обеспечение этих параметров решается путём использования весовых дозаторов минеральных материалов, минпорошка и битума на тензодатчиках.
Точность соблюдения времени «сухого» и «мокрого» перемешивания компонентов асфальтобетонной смеси в смесителе; обеспечение этого параметра решается введением в АСУ блока задатчика времени перемешивания.
Размеры сечения накопительных бункеров в плане, увеличение которых вызывает сегрегацию смеси по крупности зёрен щебня, резко снижающую однородность и качество смеси; обеспечение этого параметра обеспечивается применением узких накопительных бункеров или применением выгрузки смеси по площади широких бункеров без образования в бункере широких конусов смеси, являющихся главной причиной сегрегации.
Максимальное время хранения асфальтобетонной смеси в накопительных бункерах, т.к. длительное хранение смеси в бункерах приводит к изменению свойств битума, а при снижении температуры смеси препятствует её выгрузке; обеспечение этого параметра обеспечивается загрузкой в накопительные бункеры только требуемого на данную смену работы количества асфальтобетонной смеси.
Температура нагрева минерального порошка, т.к. введение в смеситель минпорошка без нагрева снижает температуру смеси или требует нагрева минеральных материалов до более высокой температуры; применение нагрева минпорошка особо важно для щебеночно-мастичных асфальтобетонных смесей (ЩМАС), в которых содержание минпорошка достигает 13–15%, и обеспечивается применением специальных агрегатов нагрева (теплообменников), в которых отсутствует контакт минпорошка с горячими газами, т.е. нагрев производится через металлический экран (стенку).
Технология непрерывного приготовления асфальтобетонной смеси включает:
Хранение небольшого запаса минеральных материалов в бункерах-дозаторах и дозирование щебня и песка с учетом их влажности;
дозирование минерального порошка;
подача минеральных материалов и минерального порошка в сушильный барабан, их перемешивание, нагрев и сушка;
нагрев вяжущего в рабочей емкости;
дозирование и подача вяжущего в зону «мокрого» перемешивания;
«мокрое» перемешивание компонентов в сушильном барабане-смесителе;
выгрузка готовой смеси через подъемное устройство в бункер-накопитель готовой смеси;
выгрузка готовой смеси из бункера-накопителя в транспортное средство.
В технологии непрерывного действия, где отсутствуют: сортировка горячих минеральных материалов, дозирование горячих минеральных материалов и нагрев минерального порошка, особо важными параметрами технологических операций являются:
Точность дозирования холодных минеральных материалов, определяющая состав асфальтобетонной смеси; обеспечение этого параметра решается путём: повышения точности работы дозаторов непрерывного действия за счёт использования тензометрических систем и введения в АСУ блока контроля влажности минеральных материалов (особенно песка) и блоков регулирования работы дозаторов с учётом влажности материалов.
Точность дозирования битума и минерального порошка, также определяющих состав асфальтобетонной смеси; обеспечение этих параметров решается путём использования высокоточных дозаторов и введением в АСУ регулируемой постоянной связи работы этих дозаторов с дозаторами минеральных материалов.
Точность соблюдения времени «сухого» и «мокрого» перемешивания компонентов асфальтобетонной смеси; обеспечивается путём регулировки места введения в смеситель минпорошка и битума.
Влияние и способы обеспечения параметров бункеров-накопителей смеси те же, что и при циклической технологии приготовления смеси.
Очень важным параметром обеих технологий является обеспечение постоянства фракционного состава и чистоты минеральных материалов в штабелях АБЗ. Это обеспечивается размещением штабелей минеральных материалов на площадках с асфальтобетонным и бетонным покрытием, а также устройством между штабелями сплошных барьеров, препятствующих смешиванию фракций.
Особо важными технологическими параметрами приготовления асфальтобетонной смеси являются:
Точность дозирования всех составляющих – отклонение по весу не более 0,5%;
режим сушки и температура нагрева щебня и песка – отклонения по температуре не более 5°С;
режим и температура нагрева вяжущего – отклонения по температуре не более 5°С;
время «сухого» и «мокрого» перемешивания – отклонение по времени не более 5 сек;
характер подачи готовой смеси в накопительный бункер и выгрузки (истечения) из бункера – с недопущением сегрегации минеральных материалов по крупности;
время хранения готовой смеси в накопительном бункере и равномерность теплоизоляции – с недопущением температурной сегрегации смеси.
Основными причинами и мотивами, определяющими тенденции развития асфальтосмесительных установок, являются:
Желание снизить затраты на производство смесей;
требование заказчика на получение смесей высокого качества, т.е. не ниже требований действующих стандартов;
стремление к снижению энергоемкости производства смесей и металлоемкости установок;
стремление приблизить производство смесей к месту укладки, т.е. необходимость их перемещения и сокращения сроков монтажа и демонтажа;
стремление избежать влияния человеческого фактора на процесс производства смесей, т.е. повышение степени автоматизации работы установок;
стремление к повышению надежности (безотказности) и долговечности установок;
стремление к обеспечению защиты экологии, т.е. снижению пылевых и вредных газовых выбросов в атмосферу.
Основные тенденции развития асфальтосмесительных установок в последние 20 лет – следующие:
Расширение типоразмерного ряда асфальтосмесительных установок, выпускаемых ведущими производителями Европы и США, сопровождающееся заметным повышением производительности больших установок, продолжением выпуска установок малой производительности и увеличением количества типоразмеров.
Расширение уровня автоматизации технологических процессов приготовления смеси на основе увеличения мест оперативного контроля параметров промежуточных процессов и использование компьютеров для хранения информации, ускорения изменения рецептов смесей и настройки систем обеспечения качества (температуры, дозировок и др.).
Быстрое распространение достижений отдельных фирм в обеспечении:
Точности дозирования составляющих на базе тензометрического взвешивания компонентов;
использования универсальных горелок сушильных барабанов, работающих на газе, дизтопливе, мазуте и пылевидном угле;
использования тканевых рукавных фильтров, обеспечивающих высокую степень очистки отходящих газов и возврат пыли в смесь для замены части (до 50%) минерального порошка;
использования теплоизоляции сушильных барабанов.
Схема двухбарабанного сушильно-смесительного агрегата (Astec, США)
Схема двухбарабанного
сушильно-смесительного агрегата
(Astec, США)
Все это обеспечивает высокий уровень унификации установок, выпускаемых различными фирмами.
Расширение типов асфальтосмесительных установок, т.е. выпуск стационарных, транспортабельных и мобильных (быстро перебазируемых и вводимых в работу), а также освоение рядом фирм выпуска асфальтосмесительных установок как циклических, так и непрерывных (непрерывного действия), что ведет к отказу от рассева и хранения нагретых минеральных материалов, а также от повторного их дозирования. Процессы нагрева (и сушки) и смешения производятся в сушильно-смесительном барабане, что сокращает стоимость установки, повышает ее мобильность, но требует повышения точности дозирования минеральных материалов и учета их влажности. Установки с сушильно-смесительным барабаном более компактны, имеют меньший состав агрегатов, менее металло- и энергоемки. Экономия энергозатрат достигает 20–30%.
Расширение типоразмерного ряда и вместимости бункеров-накопителей готовой смеси, что позволяет создать запас асфальтобетонной смеси до начала ее укладки и не выключать асфальтосмеситель при неравномерном подходе автомобилей-самосвалов. При этом принимаются меры против сегрегации готовой смеси в бункере-накопителе за счет смещения выгрузочного лотка (конуса), уменьшения сечения бункера-накопителя и применения нескольких выгрузочных отверстий.
Расширение типоразмерного ряда разнообразного дополнительного оборудования для:
Хранения и подачи вяжущего в виде горизонтальных и вертикальных цистерн различной емкости;
Хранения и подачи минерального порошка и пыли в виде вертикальных силосов различной емкости;
Нагрева вяжущего до рабочих температур и обогрева узлов установок с использованием теплообменников и нагревателей жидкого теплоносителя; при этом жидкий теплоноситель используется для обогрева битумных емкостей, днища и корпуса мешалок, накопительных бункеров, битумного насоса и дозатора, битумопроводов и емкостей битумовозов (автомобильных и железнодорожных) для доставки вяжущего; разнообразие установок нагрева жидкого теплоносителя и использование дорогостоящих специальных термически стойких жидкостей (синтетических и минеральных с присадками), которые можно нагревать до высоких температур в течение продолжительного времени без изменения их физико-механических свойств и выделения на внутренней поверхности трубопроводов отложений, свидетельствует о большом внимании к этим вопросам;
Получения в условиях АБЗ мелкозернистого кубовидного щебня мелких фракций (0–5, 5–10, 10–15 мм), мойки получаемых каменных материалов и широкого применения мытых отсевов дробления высокопрочных горных пород взамен (частично или полностью) природного песка.
Совершенствование конструкций асфальтосмесительных установок с обеспечением возможности введения в смесь добавок старого асфальтобетона в виде фрезажа или продуктов дробления его кусков. В мире опробовано несколько таких решений с введением холодного фрезажа (не более 20% от веса замеса), нагревом фрезажа совместно с каменными материалами или в отдельном сушильном барабане.
Ведущими производителями асфальтосмесительных установок, известными в РФ, являются:
Benninghoven, Германия;
Ammann Asphalt, EC (Швейцария, Германия, Италия, Франция);
Parker Plant Limited, Англия;
Bernardi Impianti S.P.A., Италия;
Marini (Fayat Group), Италия;
Ermont (Fayat Group), Франция;
Astec, США;
SIM, Италия.
Кроме этих фирм свою продукцию на рынке асфальтосмесительных установок представляют:
Lintec, Германия;
Teltomat-Gunter Papenburg, Германия;
Gencor International Ltd, Англия;
ACP Holdings PLC, Англия;
Kalottikone Oy, Финляндия;
KVM, Дания.
В России и странах СНГ основной поставщик асфальтосмесительных установок – ОАО «Кредмаш» (Украина). В Российской Федерации установки выпускают ОАО «Саста», ОАО «Центросвар», ОАО «УралНИТИ».
Схема агрегата для подогрева старого асфальтобетона "фрезажа" (Benninghoven, Германия)
Схема агрегата для подогрева старого асфальтобетона «фрезажа»
(Benninghoven, Германия)
Фирма Benninghoven GmbH & Co. KG существует более 75 лет. Фирма Benninghoven выпускает 5 типов асфальтосмесительных циклических установок: высокомобильные 60–100 т/ч (3 модели), мобильные 100–200 т/ч (4 модели), транспортабельные компактные 100–200 т/ч (4 модели), транспортабельные 120–320 т/ч (5 моделей) и стационарные 120–400 т/ч (6 моделей); горелки сушильных барабанов, работающие на газе, жидком топливе и угольной пыли; компьютерные системы АСУ, битумные цистерны горизонтального и вертикального типов с электроподогревом или подогревом посредством жидкого теплоносителя; установки для ПБВ и другое оборудование для АБЗ, агрегаты подготовки и введения в смесь старого асфальтобетона, а также оборудование для производства, транспортировки (кохеры) и укладки литого асфальта.
Фирма Bernardi Impianti S.P.A. выпускает 4 типа асфальтосмесительных установок: циклические мобильные 60 т/ч, транспортабельные 55–135 т/ч (4 модели), стационарные 55–315 т/ч (8 моделей) и непрерывного действия стационарные 63–202 т/ч (6 моделей).
Фирма Marini (Fayat Group) выпускает 6 типов асфальтосмесительных установок: циклические – мобильные 60 т/ч, транспортабельные 60–200 т/ч (8 моделей), стационарные 35–380 т/ч (11 моделей), непрерывного действия – мобильные 120–160 т/ч (2 модели), транспортабельные 105–405 т/ч (6 моделей) и стационарные 105–485 т/ч (7 моделей).
Фирма SIM, занимающая 6–8% мирового рынка асфальтосмесительных установок и продающая продукцию в более чем 60 стран, выпускает 3 типа асфальтосмесительных установок циклического действия: супермобильные 85 т/ч (два полуприцепа), полумобильные 80–300 т/ч (башенного типа без фундаментов на колесном шасси) и стационарные 80–300 т/ч, а также асфальтовые заводы непрерывного действия 70–350 т/ч; установки для производства модифицированного битума, системы реновации для вторичного использования асфальтовой крошки.
Фирма Ermont (Fayat Group) выпускает асфальтосмесительные установки циклического действия: мобильные на двух шасси производительностью 160 т/ч, транспортабельные и стационарные блочного и контейнерного типа производительностью 160–240 т/ч и непрерывного действия: с параллельной или противоточной конструкцией барабанов в мобильном, транспортабельном или стационарном исполнении с производительностью от 80 до 550 т/ч.
Передвижные асфальтобетонные заводы "HOT-MIX" (Kalottikone Oy, Финляндия)
Передвижные асфальтобетонные
заводы «HOT-MIX»
(Kalottikone Oy, Финляндия)
Фирма Astec выпускает 5 типов асфальтосмесительных установок. Во-первых, это установки непрерывного действия на базе коаксиального сушильно-смесительного барабана (один барабан внутри другого – т.н. технология Double Barrel), в числе которых 5 вариантов мобильных (110–410 т/ч), 5 перемещаемых (110–410 т/ч) и 6 стационарных (110–500 т/ч). Во-вторых, это установки циклического действия: стационарные (5 моделей производительностью 280–580 т/ч) и перемещаемые (9 моделей, производительность от 50 до 250 т/ч).
Фирма Ammann выпускает 2 типа асфальтосмесительных установок циклического действия: Global (транспортабельные и стационарные) – 80–200 т/ч (4 модели) и Universal (транспортабельные) 160–240 т/ч и 240–320 т/ч.
Фирма Parker Plant Ltd выпускает 3 типа асфальтосмесительных установок циклического действия: мобильные 18–240 т/ч (5 моделей), транспортабельные 125–240 т/ч (3 модели) и стационарные 125–320 т/ч (5 моделей).
Фирма Kalottikone Oy выпускает 3 типа асфальтосмесительных установок циклического действия: мобильные 120 и 220 т/ч, транспортабельные 120 т/ч и стационарные 120, 180 и 270 т/ч.
ОАО «Кредмаш» выпускает 3 модели циклических стационарных асфальтосмесительных установок производительностью 56, 110 и 160 т/ч.
ОАО «Саста» выпускает 3 модели циклических стационарных асфальтосмесительных установок производительностью 100, 160 и 200 т/ч.
ОБОРУДОВАНИЕ ДЛЯ РЕМОНТА ТРЕЩИН
Наиболее распространенным видом дефектов дорожного покрытия являются трещины
Так же, как все человечество, которое всегда стремилось создать вечный двигатель, дорожники во всем мире мечтали о дорожном покрытии с бесконечным сроком службы. Однако и первое, и второе пока остается несбыточной мечтой
Множество факторов, которые воздействуют на дорожную одежду, рано или поздно приводят к появлению дефектов на дорожном покрытии. Наиболее распространенным видом дефектов являются трещины. Вовремя не отремонтированные трещины постепенно превращаются в очаг разрушения дорожной одежды. Трещины классифицируются по ширине на узкие – до 5 мм, средние – 5–10 мм и широкие – 10–30 мм.
В зависимости в основном от ширины и причин образования трещин выбирается технология их ремонта и состав применяемого оборудования. Основной задачей при ремонте трещин является предотвращение проникновения через них воды в нижележащие слои дорожной одежды. Гидроизоляция трещин достигается за счет их герметизации битумом или специальными материалами – резинобитумной или битумно-полимерной мастиками.
Следует сразу отметить, что для обеспечения качества герметизации трещин необходимо в первую очередь ориентироваться не на битум, а на мастики горячего применения, физико-механические свойства которых значительно превосходят свойства битума. В настоящее время как отечественные, так и зарубежные фирмы выпускают широкую гамму мастик, лучшими из которых по эксплуатационным качествам являются битумно-полимерные.
При выборе мастик необходимо ориентироваться на их основные свойства: температуру размягчения, которая у отдельных марок составляет +100°С; температуру хрупкости (до?50°С); относительное удлинение (до 150% при температуре +20°С), эластичность (до 95%).
Помимо мастики, огромное влияние на качество герметизации трещин оказывает правильный выбор и строгое соблюдение технологии производства работ и применяемого оборудования.
Узкие трещины не требуют большого набора сложных технологических операций. Как правило, трещины шириной до 5 мм очищают продувкой сжатым воздухом, просушивают, прогревают и заполняют битумной эмульсией или мастикой с высокой проникающей способностью. Просушку трещины, как правило, совмещают с операцией прогрева, при этом необходимым условием является нагрев зоны трещины до температуры не менее 80°С.
Средние и широкие трещины изначально должны быть оценены на предмет разрушения кромок. В случае, если трещина имеет разрушенные кромки, технология ремонта должна начинаться с операции ее разделки, то есть искусственного расширения ее верхней части с образованием камеры, в которой обеспечивается оптимальная работа герметизирующего материала на растяжение в период раскрытия трещины. Причем ширина камеры должна быть не меньше зоны разрушения кромок трещины. Для создания наилучших условий работы герметика в камере соотношение ее ширины и глубины обычно принимается как 1:1. Кроме того, при определении геометрических размеров камеры необходимо учитывать максимально возможное раскрытие трещины и относительное удлинение используемого герметизирующего материала. Обычно ширина камеры находится в пределах 12–20 мм.
В случае, когда кромки трещины не подвергались разрушению и имеется возможность качественно загерметизировать трещину без ее разделки, данную операцию можно исключить из технологического процесса.
Следует отметить, что операция фрезерования или разделки трещины является наиболее дорогостоящей из-за высокой стоимости применяемого инструмента, и включение ее в технологию производства работ должно быть экономически и технически обосновано.
Важнейшим условием обеспечения качества герметизации трещин является наличие хорошего сцепления герметика со стенками неразделанной трещины или отфрезерованной камеры. В связи с чем большое внимание уделяется проведению подготовительных работ по очистке и просушке трещины. Даже небольшое количество грязи или влаги в полости трещины не позволяет обеспечить надежную адгезию мастики к ее стенкам. В некоторых случаях для улучшения адгезии производят подгрунтовку стенок отфрезерованной камеры праймером – маловязкой пленкообразующей (склеивающей) жидкостью.
Однако данная операция более эффективна при ремонте цементобетонных, чем асфальтобетонных покрытий. Для асфальтобетонных покрытий более целесообразно использовать прогрев зоны трещины до температуры, при которой происходит выделение вяжущего из асфальтобетона на стенках трещины, которое увеличивает прочность сцепления герметика со стенками. Бесспорно, основной технологической операцией при ремонте трещин является их заливка горячей мастикой. Мастика предварительно нагревается до температуры 150–180°С, после чего подается в устроенную камеру или непосредственно в полость трещины.
При этом в зависимости от применяемого оборудования можно либо произвести герметизацию самой трещины, либо одновременно с заливкой устроить на поверхности покрытия в зоне трещины пластырь. Такой пластырь шириной 6–10 см и толщиной 1–3 мм позволяет укрепить кромки трещины и предотвратить их разрушение. Однако опыт проведения таких работ на МКАД показывает, что устройство пластыря в зоне трещины на автомобильных дорогах с высокой интенсивностью движения малоэффективно, так как материал пластыря довольно быстро разрушается колесами движущегося транспорта.
Завершающей операцией технологии ремонта трещин является присыпка загерметизированной трещины дробленым сухим песком фракции 3–5 мм, близким по цвету основному минеральному материалу покрытия. Присыпка служит для восстановления общей текстуры и шероховатости покрытия, а также предотвращает налипание мастики на колеса автомобиля.
Технологический процесс санации трещин должен быть практически непрерывен. Операции очистки от пыли и грязи, просушки, прогрева и заливки трещин должны переходить одна в другую при минимальном разрыве по времени.
Технология санации трещин реализуется комплектом оборудования, состоящим в общем виде из фрезы для разделки трещин, механической щетки, компрессора, газогенераторной установки, плавильно-заливочной машины, оборудования для присыпки загерметизированной трещины. Ведущими зарубежными фирмами по выпуску комплектов оборудования или отдельных его видов для санации трещин, активно работающими на российском рынке, являются Breining (Германия), Grun (Германия), Schaefer (Германия), Crafco (США), Stow (США), Cedima (Германия), Strassmayr (Австрия). Все эти фирмы производят оборудование для разделки трещин. В России данное оборудование выпускает фирма «Сплитстоун». Все виды выпускаемого оборудования подразделяются в основном по типу подачи на ручные и самоходные, а также по типу используемого инструмента – алмазный или с твердым сплавом.
Оборудование для разделки трещин фирмы Cedima (Германия)
Рис.1. Оборудование для разделки трещин фирмы Cedima (Германия)
Фирма Cedima выпускает ручную машину для фрезерования трещин модели СRF-60В (рис. 1). Машина предназначена для разделки трещин как в асфальтобетонных, так и в цементобетонных покрытиях. Компактная жесткая рама установлена на специальный колесный ход, который позволяет точно отслеживать конфигурацию трещины при ее фрезеровании. В качестве режущего инструмента используются или алмазные круги малого диаметра, объединенные в пакет, или специальные алмазные фрезы с требуемой шириной режущей кромки. Разделка трещин обычно осуществляется без охлаждения режущего инструмента, то есть используются круги или фрезы для так называемого «сухого» резания. Вместе с тем для связывания пыли, образующейся в процессе резания на машине, имеется водяной бак с гибким подводом воды. Кроме того, пыль из зоны работ может быть также удалена пылесосом, для чего на машине предусмотрено стандартное его подсоединение. Привод режущего инструмента осуществляется от бензинового двигателя через клиноременную передачу. Фирма также выпускает модификацию машины, оснащенную электродвигателем. Машина для разделки трещин модели СRF-60B успешно использовалась при проведении этих работ на МКАД.
Для разделки трещин в асфальто- и цементобетонных покрытиях предназначено также оборудование фирмы Grun. Машина в процессе работы передвигается вручную, производя разделку трещины алмазным инструментом. На ее раме штатно устанавливается пылесос типа циклон для удаления пыли из зоны резания. Так же как и на машине фирмы Сеdima, имеется ручной рычаг для быстрого вывода режущего инструмента с целью предохранения его от поломок.
Аналогичные машины для разделки трещин, использующие алмазный инструмент, выпускает фирма Stow. Модели машин RСС 130Н и С-10, отличающиеся легкостью управления и хорошей маневренностью, могут быть использованы для фрезерования любых криволинейных трещин.
Машина модели FF6-SF для разделки трещин фирмы Вreining имеет существенные отличия от аналогичных машин упоминавшихся ранее фирм, основным из которых является тип используемого режущего инструмента – фрезы с твердым сплавом. В отличие от алмазной резки, когда щебень в асфальтобетонном покрытии разрезается, при фрезеровании твердым сплавом происходит дробление крупных зерен щебня.
Установка для разделки трещин фирмы Crafco (США)
Рис. 2. Установка для разделки трещин фирмы Crafco (США)
При этом, в случае использования для устройства покрытия асфальтобетонной смеси с крупным заполнителем фракции 20 мм и более, происходит вырывание крупных частиц щебня из кромки разделываемой трещины и в целом уменьшение прочности покрытия в зоне трещины. Оборудование с твердым сплавом целесообразно применять при разделке трещин в асфальтобетоне с максимальной крупностью заполнителя 10 мм и менее.
Вторым существенным отличием машины FF6-SF является наличие гидравлического привода режущего инструмента. Выхлопная труба дизельного двигателя, установленного на раме машины, смонтирована таким образом, чтобы отходящие газы были направлены в зону работы фрезы для удаления из разделываемой трещины продуктов резания. Следует также отметить, что режущий инструмент на машине расположен в передней ее части, а управляющий ею оператор находится сзади, что ограничивает обзор зоны производства работ.
Машина для разделки трещин модели РС-200 фирмы Crafco (рис.2) отличается конструкцией режущего узла, с помощью которого фреза точно повторяет конфигурацию трещины, какой бы извилистой она ни была. В качестве режущего инструмента на машине используются фрезы с твердым сплавом, которые могут разделывать трещины как в асфальтобетонных, так и в цементобетонных покрытиях.
Привод шпинделя, на котором монтируется режущая фреза, осуществляется от бензинового 2-цилиндрового двигателя через клиноременную передачу. В отличие от большинства машин, где заглубление режущего инструмента производится механическим способом, на модели РС-200 имеется электрогидравлический привод установки глубины резания. Машина обладает высокой производительностью, которая в зависимости от глубины и ширины обработки, а также обрабатываемого материала находится в пределах 300–600 м/час.
Фрезеровальные диски с твердосплавным покрытием для машин S-FF 12/F и S-FF 19/F фирмы Schaefer (Германия)
Рис. 3. Фрезеровальные диски с твердосплавным покрытием
для машин S-FF 12/F и S-FF 19/F фирмы Schaefer (Германия)
Машины, выпускаемые фирмами Schaefer и Strassmayr имеют привод хода, и также в качестве инструмента на них используются фрезы с твердым сплавом. Особенностью твердосплавного инструмента является возможность его затачивания, если он затупился в процессе работы. Самоходные машины моделей S-FF12, S-FF19 (рис. 3) и S-FF27 обладают высокой производительностью. Гидравлический привод ходовой части позволяет машине модели S-FF12 передвигаться со скоростью до 5,0 км/час, машинам S-FF19 и S-FF27 – до 7,0 км/час.
При этом разделка трещин производится на скоростях 3–8 м/мин. Даже на таких высоких скоростях из-за хорошей маневренности, обеспеченной системой управления, машина при работе точно повторяет все изгибы даже самой криволинейной трещины. Рабочее место оператора находится непосредственно на самой машине, и с него обеспечивается очень хорошая обзорность зоны резания. Кроме того, из-за относительно большой массы на этих машинах наблюдается достаточно малая вибрация, присущая основной массе машин, использующих твердосплавный инструмент.
Дисковая щетка фирмы Schaefer (Германия)
Рис. 4. Дисковая щетка
фирмы Schaefer (Германия)
В случае, когда необходимо произвести санацию достаточно широких и сильно загрязненных трещин, их очистку обычно производят механическими щетками. Такие щетки моделей FВ 16 (рис. 4) и НР 16 выпускают соответственно фирмы Вreining и Schaefer.
В качестве рабочего инструмента используется диск с металлическим ворсом диаметром 300 мм и толщиной 6, 8, 10 или 12 мм в зависимости от ширины трещины, толщина рабочего органа на 2–4 мм должна быть меньше ширины очищаемой трещины.
Привод рабочего органа осуществляется от бензинового или дизельного двигателя мощностью 12 кВт. Управление механической щеткой осуществляется вручную. Следует отметить, что механическая щетка в первую очередь предназначена для прочистки швов в цементобетонных покрытиях, однако ее эффективность при очистке относительно прямолинейных широких трещин в асфальтобетоне не раз подтверждена на практике.
Качества герметизации трещин в асфальтобетонных покрытиях невозможно добиться без выполнения технологических операций их просушки и прогрева. Практически все производители оборудования для санации трещин выпускают так называемые газогенераторные установки.
Оборудование для прогрева стенок трещины типа Fugenwolf фирмы Schaefer (Германия)
Рис. 5. Оборудование для прогрева стенок трещины типа Fugenwolf фирмы Schaefer (Германия)
Название этих установок может быть различное, например, НОТ-DОG у фирмы Вreining, Fugenwolf у фирмы Schaefer (рис. 5) или «тепловое копье» у других фирм, но принцип работы в основном один. Он основан на подаче под большим давлением горячего сжатого воздуха в полость трещины. Сжатый воздух от компрессора производительностью 2,5-5,0 м3/мин с давлением 3,5–12 кг/см2 смешивается с природным газом и в виде газовоздушной смеси поступает в камеру сгорания, где поджигается. Нагретый до температуры 200–1300°С воздух через форсунку со скоростью 400–600 м/сек подается в зону обрабатываемой трещины. Расход газа при этом составляет 3–6 кг/час. Высокоскоростной поток сжатого воздуха, кроме прогрева, эффективно очищает полость самой трещины и, кроме того, вырывает отдельные разрушенные частицы покрытия из зоны, прилегающей к трещине.
Однако многие организации, занимающиеся ремонтом трещин, не имеют подобных газогенераторных установок и осуществляют просушку и прогрев трещины горелками с открытым пламенем. Это приводит к интенсивному старению и выгоранию вяжущего, в результате – ускоренное разрушение асфальтобетонного покрытия в зоне трещины.
Обычно заливка трещины герметиком осуществляется сверху вниз, так как сопло заливщика невозможно глубоко погрузить в паз трещины или до дна отфрезерованной камеры. При этом, если предварительно не произведен прогрев стенок трещины, происходит быстрое охлаждение герметика в полости трещины, что приводит к образованию пробки, препятствующей проникновению мастики на требуемую глубину и в дальнейшем, в процессе эксплуатации, отрицательно сказывается на работе герметика.
Все упоминавшееся ранее оборудование занимает важное место в реализации технологического процесса ремонта трещин, однако все оно относится к оборудованию для проведения подготовительных работ, основными же являются различные модели заливщиков швов. Современные заливщики в общем виде представляют собой обогреваемый бак, установленный на раме, оснащенной колесным ходом. Обогрев может осуществляться за счет масляного теплоносителя, газом или горелкой с дизельным топливом. Герметизирующий материал загружается в бак, где нагревается до рабочей температуры, а затем с помощью насоса по термостойким шлангам подается в подготовленную трещину. Равномерность нагрева герметика имеет очень важное значение, так как, например, для битумно-полимерной мастики нагрев до 200°С может привести к ее термическому разрушению. В связи с этим лучшие показатели у плавильно-заливочных машин с системой масляного обогрева. Практически все модели заливщиков оснащаются системами контроля температуры герметика и термального масла. Отдельные заливщики оборудуются специальными мешалками, способствующими равномерному нагреву всей массы герметика. Плавильно-заливочные машины выпускаются, как правило, прицепными. Заливщик может транспортироваться на объект в виде прицепа к автомобилю со скоростью до 80 км/час, а затем работать автономно, передвигаясь собственным ходом со скоростью до 5 км/час.
Универсальная самоходная машина для герметизации трещин модели UVM 500 фирмы Breining (Германия)
Рис. 6. Универсальная самоходная машина для герметизации трещин
модели UVM 500 фирмы Breining (Германия)
Заливщики фирмы Вreining моделей МОNО 250 FU, МОNО 500 FU и МОNО 800 FU смонтированы на автомобильном шасси. Та же фирма производит самоходную машину модели UVМ 500 (рис. 6), на раме которой, кроме заливщика МОNО 500 FU, смонтирован также компрессор. Такое сочетание оборудования позволяет прочищать, просушивать и прогревать трещину установкой НОТ-DОG и одновременно заливать ее мастикой. В этом случае одна технологическая операция плавно переходит в другую с минимальным разрывом по времени, что несомненно положительно сказывается на качестве производимых работ. Машина имеет гидропривод на задние колеса и может передвигаться со скоростью до 20 км/час.
Однако подача воздуха к газогенераторной установке может осуществляться и от отдельного компрессора, находящегося, например, в кузове автомобиля, буксирующего заливщик.
Непосредственно герметизация трещин осуществляется через различные сопла, размер которых зависит от ширины заполняемой трещины. При необходимости заливочное сопло может оснащаться башмаками для устройства на поверхности покрытия в зоне трещины мастичного пластыря шириной 6–8 см.
Плавильно-впрыскивающие установки серии Super Shot фирмы Crafco (США)
Рис. 7. Плавильно-впрыскивающие установки серии Super Shot фирмы Crafco (США)
В России заливщик швов ЭД 135 по лицензии фирмы Вreining (Германия) выпускает ОАО «НПО РОСДОРМАШ». Важным параметром заливщиков является время разогрева герметика до рабочей температуры, у лучших моделей это время составляет всего 45–60 минут. Слабым местом заливщиков является остывание мастики в шлангах и образование пробок. Для избавления от этого недостатка практически на всех моделях предусмотрена замкнутая система циркуляции горячей мастики с обратной подачей ее от заливочного сопла в бак, а также электропрогрев шлангов, как, например, на заливщиках серии Super Shot фирмы Сrafco (рис. 7).
Заливщики фирм Вreining, Grun, Schaefer и других имеют встроенный компрессор, с помощью которого осуществляется очистка воздухом трубопроводов и шлангов после работы.
Кроме собственно заливщиков для герметизации трещин могут быть использованы кохеры, имеющие системы подогрева и перемешивания. При этом непосредственно герметизация трещин осуществляется, как правило, малыми заливщиками, в емкость которых горячая мастика заполняется из кохера. Малые заливщики также могут иметь собственную систему подогрева емкости и заливочного сопла от газового баллона.
Малый заливщик трещин Fugenwiesel фирмы Schaefer (Германия)
Рис. 8. Малый заливщик трещин Fugenwiesel фирмы Schaefer (Германия)
Примером такого оборудования может служить заливщик Fugenwiesel фирмы Schaefer (рис. 8). На раме заливщика смонтированы две емкости, одна из которых заполняется герметиком, а вторая песком из отсевов дробления фракции 1–3 мм. Таким образом, данный заливщик не только герметизирует трещину, но и одновременно присыпает ее для исключения прилипания мастики к колесам автомобиля. Достоинством заливщика Fugenwiesel является возможность герметизировать трещины большой ширины, так как мастика из сопла подается струей шириной в несколько сантиметров.
Малый заливщик модели VG 80 фирмы Breining (Германия) имеет собственный подогрев емкости с герметиком, что позволяет ему работать в автономном режиме при выполнении небольшого объема работ.
Для присыпки загерметизированного шва фирмы выпускают специальное оборудование – распределитель. Например, у фирмы Вreining таковым является модель FS-1. Оборудование представляет собой бункер вместимостью 70 литров, установленный на три колеса. Причем, переднее, рояльное колесо позволяет двигаться точно по направлению трещины, а на оси задних внутри бункера смонтирован дозировочный валик. Распределитель перемещается вручную вдоль загерметизированной трещины, сразу же за заливщиком, при этом колеса приводит во вращение валик, дозирующий дробленый песок или мелкий щебень на поверхность мастики, залитой в трещину.
Дорожники знают, что для ремонта трещин обычно применяется медицинский термин «санация» – комплекс лечебно-профилактических мероприятий, направленных на предупреждение и ликвидацию заболеваний зубов. Трещины на покрытии подобны больным зубам, оказывающим вредное влияние на весь организм человека. И чем раньше и надежней их начать «лечить», тем здоровее будет «организм» автомобильной дороги.
ОСОБЕННОСТИ СТРУКТУРЫ И СВОЙСТВ БИТУМОВ, МОДИФИЦИРОВАННЫХ ПОЛИМЕРАМИ
Нефтяные битумы находят широкое применение в дорожном и гражданском строительстве
Нефтяные битумы находят широкое применение в дорожном и гражданском строительстве, благодаря высокой пластичности, способности выдерживать без разрушений воздействие низких температур, температурных перепадов, различных деформационных нагрузок.
Основным потребителем нефтяных битумов является дорожное строительство, в настоящее время до 90% производимого во всем мире объема товарных битумов потребляется дорожной отраслью. Специалисты разных государств сходятся во мнении, что нефтяной битум является самым дешевым и наиболее универсальным материалом для применения в качестве вяжущего при устройстве дорожных покрытий.
Необходимо отметить тот факт, что дорожные битумы российского и зарубежного производства принципиально различаются по качеству, что предопределено различием нормативных требований к этому виду товарной продукции в нашей стране и за рубежом. Практика дорожного строительства в России, состояние дорог даже федерального значения опровергает мнение о безукоризненности существующих требований к дорожным битумам, сформулированных в ГОСТ 22245.
Многолетний опыт устройства и содержания дорожных покрытий с использованием битумов дорожных вязких марки БНД, изготавливаемых российскими НПЗ, свидетельствует о том, что, например, при значении показателя температуры хрупкости битума, равном?27°C (что намного превышает предел, указанный ГОСТ 22245), разрушение покрытия начинается уже в первый год эксплуатации по причине недостаточной способности битумного вяжущего к растяжению (и это при соответствии значения показателя растяжимости битумов при 25 и 0°C нормативным требованиям).
Положительные результаты применения в последние 10 лет при строительстве и ремонте дорожных покрытий в Санкт-Петербурге и Ленинградской области битумов, характеризующихся иными, чем битумы марок БНД, свойствами, например фирм NESTE, NYNAS, БДУ (Ухтинский НПЗ), позволяют сделать вывод о том, что в основе своей для повышения эксплуатационной надежности дорожных покрытий оказывается достаточным изменить качество дорожного битума.
Использование битумов зарубежного производства и битума дорожного улучшенного марки БДУ (ТУ 38.1011356-91) в составе асфальтобетонных смесей взамен битума дорожного вязкого марки БНД (ГОСТ 22245-90) обеспечило возможность заказчику требовать, а подрядным организациям Санкт-Петербурга принимать на себя гарантийные обязательства на устроенные верхние слои дорожных одежд сроком до 5–7 лет.
Более высокая эксплуатационная надежность асфальтобетонов, изготовленных с применением вышеуказанных марок битума, обусловлена оптимальным комплексом реологических свойств последнего. Это достигается регламентацией зарубежными стандартами требований к таким показателям качества битумов, как кинематическая вязкость при 135°C, динамическая вязкость при 60°C, и установлением пределов изменения глубины проникания иглы, растяжимости при 25°C, динамической вязкости при 60°C в процессе испытания битума на термостабильность по методике ASTM D 1754 (или ASTM D 2872), имитирующей условия воздействия на битумную пленку кислорода воздуха при повышенной температуре в асфальтосмесителе при изготовлении горячих асфальтобетонных смесей.
Анализ результатов испытания (в том числе и по методикам ASTM) битумов дорожных российского производства (таблица 1) показывает, что при идентичности значений показателя глубины проникания иглы при 25°C и других битумы, изготовленные из остатков переработки разных по химическому составу нефтей, принципиально различаются по вязкости. При работе в составе дорожного асфальтобетона наиболее устойчивым к воздействию сдвиговых усилий в теплое время года оказывается битум марки БНД 60/90, характеризующийся более высокой динамической вязкостью при 60°C. Однако, трещиностойкость асфальтобетонных покрытий при прочих равных условиях зависит от способности битума выдерживать без разрушения растягивающие усилия.
Наименование показателей БДУ 70/100 ТУ 38.1011356-91
(изм. №2) БДУС 70/100 ТУ 0256-096-00151807-97 БДН 60/90 ГОСТ 22245-90
Глубина проникания иглы
при 25°C, 0,1 мкм 90 89 89
Температура размягчения, °C 47 46 47
Растяжимость при 25°C, см >150 >150 79
Температура вспышки, °C 284 290 247
Температура хрупкости, °C ?20 ?19 ?22
Кинематическая вязкость
при 135°C, сСт 420 239 274
Динамическая вязкость
при 60°, Па с 209 87 375
После испытания по методике ASTM D 1754
Изменение массы после прогрева, % масс 0,09 0,18 0,92
Температура размягчения, °C 49 50 51
Остаточная пенетрация, в % от исходного значения 74 69 64
Растяжимость при 25°C, см >150 125 38
Кинематическая вязкость
при 135°C, сСт 520 320 366
Динамическая вязкость
при 60°C, Па с 436 169 972
Таблица 1.
Физико-механические свойства дорожных битумов, полученных из нефтяного сырья разной химической природы
Битумы дорожные разных марок характеризуются разным уровнем значений показателя растяжимости при 25°C: для битума дорожного вязкого растяжимость при 25°C, как правило, низкая (менее 100 см). В условиях испытания на термостабильность по методике ASTM D1754 резко изменяются значения показателей физико-механических свойств, в том числе и обусловливающих работоспособность нефтяного вяжущего. В результате наименьшей растяжимостью характеризуется битум дорожный вязкий БНД 60/90, что обусловливает и более низкую трещиностойкость асфальтобетона, изготовленного с использованием битума этой марки, особенно при переходах температуры через 0°C.
В химических процессах, протекающих при высокой температуре в присутствии кислорода воздуха, наиболее активно участвуют соединения, входящие в состав битума марки БНД 60/90, о чем свидетельствует значительная потеря массы образца при испытании по методике ASTM D 1754. Известно, что при смешении с минеральным материалом битум переводится в пленочное состояние, причем толщина пленки в зависимости от фракционного состава асфальтобетонной смеси достигает 5–15 мкм.
Изменение индекса старения битума во время смешения с минеральным материалом при изготовлении горячих асфальтобетонных смесей, при хранении и транспортировке, при работе в составе дорожного асфальтобетона.
Рис. 1. Изменение индекса старения битума во время смешения с минеральным материалом при изготовлении горячих асфальтобетонных смесей, при хранении и транспортировке, при работе в составе дорожного асфальтобетона.
а – при изготовлении асфальтобетонной смеси;
b – при хранении, транспортировке и укладке;
с – за 8 лет работы в составе асфальтобетонного покрытия
Фактически 1т битума распределяется по поверхности, равной 10 000 м2. Следовательно, в асфальтосмесителе создаются все условия для окисления битума и удаления летучих компонентов, т. е. для химического старения битума. С повышением температуры скорость реакции окисления соединений, входящих в состав битума, возрастает. По данным фирмы «SHELL» (рис.1), интенсивность процесса старения битума на стадии приготовления асфальтобетонных смесей намного выше, чем при транспортировке и эксплуатации.
На основании вышеизложенного, следует подчеркнуть, что проблема качества дорожных битумов, с точки зрения их эксплуатационной надежности в составе дорожных покрытий, в России реально существует, однако для ее решения недостаточно добиться соответствия показателей товарных свойств битумов дорожных вязких марки БНД требованиям действующего ГОСТ 22245.
Необходимо так же, как и за рубежом, регламентировать изменение таких свойств битума, как глубина проникания иглы, растяжимость и изменение массы в технологических условиях приготовления горячих асфальтобетонных смесей, а также дополнительно ввести в перечень нормируемых показателей качества параметры вязкости.
В условиях постоянного роста интенсивности движения, нагрузок на ось проблема повышения эксплуатационной надежности дорожных битумов в покрытиях в нашей стране приобретает все большую остроту. Следует принимать меры для увеличения срока службы дорожных покрытий на мостах и искусственных сооружениях – объектах, на которых, как показывает зарубежный опыт, потенциальных возможностей нефтяного битума даже оптимизированного качества оказывается недостаточно.
Все это обусловливает необходимость не только корректировки нормативных требований к физико-механическим свойствам товарных дорожных битумов отечественного производства, но и разработки, внедрения в практику дорожного строительства на основе битумов улучшенного качества новых материалов, способных обеспечивать более высокую прочность, долговечность дорожных покрытий, по сравнению с потенциальными возможностями нефтяных битумов.
Изучением вопроса придания битумам специфических свойств ученые всего мира занимаются более 55 лет. За прошедшие годы накоплен богатейший багаж знаний, основывающийся не только на результатах научных исследований, но и на практическом опыте использования модифицированных битумов, в том числе и в дорожном строительстве.
Установлено, что экономически эффективными модификаторами свойств нефтяных битумов являются те, которые доступны и недороги. С технической точки зрения для создания на основе битумов композиционных материалов с заданным комплексом свойств могут применяться только те модификаторы, которые:
Не разрушаются при температуре приготовления асфальтобетонной смеси;
совместимы с битумом при проведении процесса смешения на обычном оборудовании при температурах, традиционных для приготовления асфальтобетонных смесей;
в летнее время повышают сопротивление битумов в составе дорожного покрытия к воздействию сдвиговых напряжений без увеличения их вязкости при температурах смешения и укладки, а также не придают битуму жесткость или ломкость при низких температурах в покрытии;
химически и физически стабильны и сохраняют присущие им свойства при хранении, переработке, а также в реальных условиях работы в составе дорожного покрытия.
В настоящее время в зарубежной практике для устройства и ремонта дорожных покрытий при необходимости используются композиционные материалы на основе битума и модификаторов, таких как сера, каучук (полибутадиеновый, натуральный, бутилкаучук, хлоропрен и др.), органо-марганцевые компаунды, термопластичные полимеры (полиэтилен, полипропилен, полистирол, этилен-винилацетат (EVA), термопластичные каучуки (полиуретан, олефиновые сополимеры, а также блоксополимеры стирол-бутадиен-стирола (СБС).
Целесообразность применения в составе дорожного асфальтобетона битума, модифицированного тем или иным видом модификатора, в каждом конкретном случае обосновывается с технической и экономической точки зрения.
По данным ЕАРА (таблица 2), доля модифицированных битумов от общего объема битумов, используемых для строительства и ремонта дорожных покрытий, в разных странах различна. Следует отметить рост потребления этого вида материалов к 2001 г., по сравнению с 1995 г.
Страна Модифицированные битумы, %
1995 1996 1997 1998 1999 2000 2001
Австрия 8 8 8 8 Нет данных 11 Нет данных
Бельгия 3 7 13 12 16 15 18
Чехия 11 16 15 17 16 13 18
Дания 5 5 5 5 5 5 5
Финляндия 1 1 1 1 1 1 1
Франция 10 10 10 10 10 10 <10
Испания 5 4 8 5 Нет данных Нет данных Нет данных
Голландия ~7 7 6 ~6 7 7 7
Ирландия 3 5 5 7 7 8 10
Германия 7 8 8 9 8 Нет данных 14
Норвегия 2 2 1 2 <1 <1 3
Польша 7 - 6 7 6 6 6
Португалия 1 1 2 1 0 3 11
Словакия Нет данных 13 12 Нет данных Нет данных Нет данных 20
Словения 3 5 6 7 9 8 9
Швейцария 5 5 Нет данных 5 Нет данных Нет данных Нет данных
Швеция 2 2 3 2 3 3 2
Венгрия 4 3 4 4 1 1 10
Великобритания 4 Нет данных 4 4 Нет данных Нет данных 5
Италия 3 4 5 6 7 7 7
Япония 7 7 7 10 10 11 11
США 5 5 4–5 Нет данных Нет данных Нет данных Нет данных
Таблица 2.
Доля модифицированных битумов в общем объеме дорожных битумов, используемых для строительства и ремонта дорожных покрытий в Европе по данным ЕАРА
В среднем в 2001 г. количество модифицированных битумов, использованных в дорожном строительстве в европейских государствах, составило 7% (рис.2). Характер распределения объема потребления модифицированных битумов по видам модификаторов (рис.2) свидетельствует о том, что наибольшее применение находят полимеры: полиолефины (9%), EVA (12%), полибутадиен (14%), типа СБС (41%). Производство битумов, модифицированных полимерами типа СБС, в европейских государствах к 2001 г. возросло в среднем до 50% и составило, например, во Франции 80%, в Германии – 95%, в Испании – 65%, Бельгии – 80%, в Италии – 100% от всего объема изготавливаемых модифицированных битумов (сведения предоставлены фирмой «KRATON POLYMER»).
Доля потребления модифицированных битумов в европейских государствах, в 2001 г. Доля потребления битумов с разными видами модификаторов европейских государствах в 1998 г.
Рис. 2.
Доля потребления модифицированных битумов в европейских государствах, в 2001 г.
Доля потребления битумов с разными видами модификаторов европейских государствах в 1998 г.
Рост объемов потребления дорожной отраслью полимеров типа СБС обусловлен их способностью не только повышать прочность битума, но и придавать полимерно-битумной композиции эластичность – свойство, присущее полимерам, причем при небольшой концентрации (3–5% от массы битума).
Использование в рецептуре асфальтобетонной смеси битума, модифицированного полимером типа СБС, обеспечивает дорожному покрытию способность к быстрому снятию напряжений, возникающих в покрытии под воздействием движущегося транспорта. В настоящее время за рубежом композиции битума с разным содержанием полимера типа СБС находят широкое применение для устройства дорожных одежд на искусственных сооружениях (мостах, дорожных развязках и пр.) и, как показывает опыт, обеспечивают длительные сроки работы покрытий, несмотря на особо сложные условия их эксплуатации.
Кроме того, на основе полимеров типа СБС изготавливаются битумные мастики для разных видов дорожных ремонтных работ (заливки деформационных швов на мостах, трещин на асфальтобетонных покрытиях и др.), а также для герметизации площадок, предназначенных для сбора бытовых и др. отходов. Применению битумов, модифицированных полимером, предшествует в каждом конкретном случае технико-экономическое обоснование, поскольку стоимость модифицированного битума намного превосходит стоимость битума.
Модифицирующий эффект от введения полимера в битум зависит от правильности проведения процесса приготовления полимерно-битумной композиции.
Анализ известных способов приготовления битумов, модифицированных полимерами, показывает, что все они предусматривают, как правило, повышенную температуру процесса (150–200°C) и интенсивное перемешивание компонентов. Температура разложения большинства используемых для модификации битумов полимеров (полиэтилена, полипропилена, этилен-пропиленовых каучуков, термоэластопластов и др.) значительно превышает температуру совмещения их с битумом. Следовательно, реакции термо- и механодеструкции полимеров в массе битума не происходят, а если и имеют место, то протекают в очень незначительной степени.
Битумы при нагревании размягчаются, а термопластичные полимеры, независимо от того, были они кристаллическими или аморфными, переходят в вязко-текучее состояние. Таким образом, смесь полимера и битума при повышенной температуре представляет собой смесь двух жидкостей, различающихся по вязкости, а следовательно, процесс их смешения в основном должен сводиться к диспергированию жидкости в жидкости.
Микроструктура композиций битума с 1% масс СКЭПТ-Э-30 при 200 и 25°С
Рис. 3. Микроструктура композиций битума с 1% масс СКЭПТ-Э-30
при 200 и 25°C
Известно, что степень дисперсности таких систем при прочих равных условиях определяется соотношением вязкости компонентов, а также взаимной растворимостью. В случае термодинамически несовместимых (нерастворимых или частично растворимых) компонентов предельный размер частиц в смеси зависит только от соотношения вязкостей и условий перемешивания, а смесь при повышенной температуре представляет собой эмульсию (рис.3).
При приложении нагрузки к таким системам происходит деформация (вытягивание) капель полимера в массе битума по направлению действия силы, и в зависимости от молекулярной массы, пластичности полимера разрушение, дробление их на капли или вытягивание в нити (рис.4). Низкая вязкость полимера способствует лучшему диспергированию его в битуме. При повышении содержания полимера размер капель в массе битума возрастает, т. к. растет вероятность их коалесценсии (слияния), приводящей к обращению фаз в системе. Так, этилен-пропиленовый каучук СКЭПТ-Э-30 образует непрерывную фазу в битуме при введении в количестве не менее 9% масс (рис.5).
Для взаимно растворимых компонентов степень дисперсности системы дополнительно возрастает за счет взаимодействия компонентов на границе раздела фаз. К таким полимерам относятся блоксополимеры типа СБС: KRATON D, ДСТ-30. Наличие в структуре стирол-бутадиен-стирольного полимера ароматических блоков обусловливает его сродство с нефтяным битумом, содержащим значительное количество ароматических соединений.
Микроструктура композиций битума с 5% масс СКЭПТ-Э-30 при 200 и 25°С
Рис. 4. Микроструктура композиций битума с 5% масс СКЭПТ-Э-30
при 200 и 25°C
В результате структура битумов, модифицированных полимером типа СБС, принципиально отличается от структуры битумных композиций с алифатическими полимерами. При температуре смешения (175–185°C) вследствие растворения полимера в мальтенах образуется гомогенная композиция, и, как показывают оптические исследования, однородная- при увеличении в 600 раз. Концентрационный предел взаимной растворимости компонентов (битума и полимера) снижается с увеличением молекулярной массы полимера.
Так, при технологической температуре битум образует оптически однородные композиции с высокомолекулярным дивинил-стирольным термоэластопластом (М = 150 000) при содержании последнего до 5% масс, в то время как с низкомолекулярным ДСТ-30 (М = 45 000) – до 9% масс. При дальнейшем повышении концентрации ДСТ-30 в битуме происходит выделение в отдельную фазу асфальтосмолистой части битума, не являющейся растворителем для полимера (рис.6).
Таким образом, процесс смешения при высокой температуре битума с полимерами любой химической природы протекает в две стадии: эмульгирование размягченного полимера в жидком битуме и последующее частичное (набухание) или полное растворение. Глубина процесса диспергирования полимера в битуме при прочих равных условиях определяется химической природой и молекулярной массой полимера, химическим составом битума, а также соотношением компонентов в смеси.
Микроструктура композиций битума с 20% масс СКЭПТ-Э-30 при 200 и 25°С
Рис. 5. Микроструктура композиций битума с 20% масс СКЭПТ-Э-30
при 200 и 25°C
На практике для модификации свойств дорожных битумов должны использоваться полимеры, априори способные совмещаться с нефтяным битумом при повышенной температуре за минимальный период времени. Фирма KRATON, например, специализирующаяся на производстве полимеров типа СБС, рекомендует для этих целей несколько марок: KRATON D1101, KRATON D1192, KRATON D1116 и др.
Степень дисперсности полимерно-битумной композиции в значительной степени зависит и от способа смешения компонентов. Наилучшие результаты достигаются при использовании высокопроизводительных аппаратов –коллоидных мельниц, время пребывания компонентов при высокой температуре в которых минимально, что предотвращает старение битума и способствует созданию высокодисперсных систем, характеризующихся наиболее оптимальным комплексом физико-механических свойств.
При проведении процесса приготовления битума, модифицированного полимером, в аппарате с мешалкой длительность процесса перемешивания компонентов достаточно велика и в зависимости от конструкции смесителя и количества вводимого полимера составляет до 5 и более часов, что, безусловно, оказывает негативное влияние на качество конечного продукта вследствие старения битума под воздействием высокой температуры в присутствии кислорода воздуха, а также приводит к образованию более грубых дисперсных систем.
Структура битумов, модифицированных рассмотренными выше видами полимеров, созданная при технологической температуре, как правило, сохраняется и после охлаждения. Это обусловлено резким увеличением вязкости приготовленного полимерно-битумного материала при понижении температуры, препятствующим расслоению дисперсной системы. Следовательно, понятие «совместимость полимеров с битумами» включает две составные части: термодинамическую совместимость компонентов, а также совместимость на уровне двухфазных структур.
Микроструктура композиции битума с 10% масс ДСТ-30 при 25°С
Рис. 6. Микроструктура композиции битума с 10% масс ДСТ-30
при 25°C
При комнатной температуре и в реальных условиях эксплуатации битумы, модифицированные полимерами, представляют собой, как правило, микро- или макро- неоднородные системы, т. е. являются композиционными материалами. Свойства их определяются фазовой структурой смеси, в частности механические – преимущественно, свойствами непрерывной фазы. Именно поэтому способностью придавать битуму эластичность (свойство, присущее в том числе и олефиновым полимерам, например полиэтилену, полипропилену, этилен-пропиленовому каучуку и др.) обладают лишь те полимеры, которые образуют непрерывную фазу в массе композиции. Роль полимера, образующего дисперсную фазу в массе битума, сводится лишь к упрочнению материала за счет наполнения его частицами. Варьируя видом, концентрацией полимера, можно получать композиционные материалы с заданным комплексом физико-механических свойств.
Качество битума не оказывает существенного влияния на характер модифицирующего действия полимеров, который обусловлен, преимущественно, химической природой полимера. Однако химический состав и структура битума влияют на совместимость с полимерами и свойства конечного продукта. С повышением степени окисленности битума совместимость его с полимерами любого химического строения и молекулярной массы ухудшается, что обусловлено увеличением содержания в битуме асфальтенов и высокомолекулярных смол, снижением количества масел и низкомолекулярных смол, которые принимают непосредственное участие в процессе растворения полимеров. Использование в качестве исходного сырья для приготовления полимерно-битумных композиций битумов, обогащенных ароматическими соединениями, благоприятствует совместимости компонентов, что согласуется с известными положениями теории физической химии полимеров и обусловлено лучшей растворимостью полимеров в ароматических соединениях.
Свойства композиций, приготовленных в одинаковых технологических условиях из разных по химической природе битумов (БДУ – из тяжелой ярегской нефти; БДУС – из смеси западно-сибирских нефтей) при использовании полимера KRATON D 1101 (фирмы «SHELL»), различны (таблица 3). Введение полимера приводит к резкому снижению значений показателя растяжимости битума при 25°C. За счет более высокой способности к растяжению битума марки БДУ композиция последнего с KRATON D 1101 характеризуется также более высокими значениями показателя растяжимости, по сравнению с материалом, приготовленным на битуме марки БДУС. Для придания битуму, модифицированному полимером, способности выдерживать без разрушения растягивающие усилия в реальных условиях эксплуатации дорожных покрытий в качестве исходного сырья для приготовления полимерно-битумной композиции следует применять битумы, характеризующиеся высоким уровнем значений показателя растяжимости при 25°C (более 100 см) как до, так и после смешения с минеральным материалом.
Наименование показателя Свойства модифицированных битумов, изготовленных на:
БДУ 70/100 БДУС 70.100
при 25 °C 57 54
Глубина проникания иглы, мм 10-1,
при 0 °C 29 27
Температура размягчения, °C 82 86
Растяжимость при 25 °C, см 94 60
Растяжимость при 0 °C, см 48 28
Эластичность при 25 °C, % ,
через 3 мин. после разрыва 77 60
Эластичность при 25 °C, % ,
по п. 7.2.2 ОСТ 218.010* 89 89
Кинематическая вязкость при 135 °C, Сст 1710 1588
Однородность Однородно Однородно
Температура хрупкости, °C ?27 ?27
Температура вспышки, °C 286 275
Сцепление с гранитом Не удовл. Не удовл.
Сцепление с габбродиабазом Контр. обр. №1-2 Контр. обр. №1-2
Стабильность температуры размягчения, °C 15 29
После испытания по методике ASTM D 2872
Остаточная пенетрация,
% от исходного значения 82 83
Растяжимость при 25 °C, см 84 52
Эластичность при 25 °C, % ,
через 3 мин. после разрыва 67 51
Эластичность при 25 °C0C, % ,
по п. 7.2.2 ОСТ 218.010* 87 83
Таблица 3.
Свойства композиций битумов разной химической природы, приготовленных с использованием полимера KRATON D 1101 (5% масс)
За счет лучшей растворимости в массе битума дорожного улучшенного марки БДУ полимер типа СБС способен в несколько большей степени реализовывать присущую ему эластичность. Этим же объясняется и более высокая вязкость композиции полимера с битумом, полученным из остатков переработки тяжелой ярегской нефти.
Битумы, модифицированные полимерами (в том числе и блоксополимерами), являются дисперсными (неоднородными) системами, а следовательно, термодинамически неустойчивыми, что является причиной их расслоения (разрушения), особенно при повышенной температуре в статических условиях (в отсутствие перемешивания). Чем выше сродство полимера к битуму, чем выше степень дисперсности полимера в массе битума, тем выше устойчивость композиционного материала к расслаиванию. Вследствие худшей совместимости компонентов композиция, приготовленная на битуме марки БДУС с полимером KRATON D 1101, характеризуется наибольшим различием в значениях показателя температуры размягчения верхнего и нижнего слоев массы композиции (таблица 3) после испытания на термостабильность в статических условиях, по сравнению с битумом марки БДУ, модифицированным равным количеством этого же полимера, приготовленным в идентичных условиях.
При использовании высокоэффективных смесителей, позволяющих достичь более высокой степени дисперсности полимера в битуме, устойчивость композиционных материалов к расслаиванию возрастает (температура размягчения массы полимерно-битумного вяжущего в верхнем и нижнем слоях после термостатирования практически одинакова), вот почему за рубежом приготовление полимерно-битумных материалов осуществляется с помощью коллоидных мельниц.
Для обеспечения заданного качества товарной продукции, достижения максимальной эффективности от ее использования в дорожном строительстве нормативные требования к битумам, модифицированным полимерами, обязательно должны предусматривать контроль не только за однородностью свежеприготовленной композиции, но и за устойчивостью к расслаиванию при повышенной температуре. Учитывая тот факт, что полностью предотвратить расслоение композиции битума с полимером типа СБС на стадии хранения при повышенной температуре невозможно, необходимо лимитировать длительность хранения, а также осуществлять механическое перемешивание массы изготовленной товарной продукции на стадии хранения.
В связи с тем, что механизм распределения в битуме полимера заключается в растворении последнего в мальтеновой части битума, на первый взгляд кажется, что для достижения наилучшей совместимости компонентов необходимо увеличить количество масляных компонентов в битуме, например за счет дополнительного введения минеральных масел. Однако следует напомнить, что нефтяные дорожные битумы, как коллоидные системы, также термодинамически неустойчивы во времени. Введение масел приводит к нарушению относительной стабильности структуры битума, сформировавшейся на стадии изготовления последнего. В зависимости от химической природы соединений, входящих в состав минерального масла, последнее может являться хорошим или плохим растворителем по отношению к битуму. Кроме того, уместно напомнить, что процесс совмещения битума с минеральным маслом не так прост, поскольку механизм его также заключается в смешении жидкостей, различающихся по вязкости. Следовательно, получение при повышенной температуре гомогенной массы на основе нефтяного битума и минерального масла само по себе представляет непростую технологическую задачу. Использование полимерно-масляных концентратов в качестве исходного компонента для приготовления модифицированного битума не упрощает процесс получения материала с заданным комплексом физико-механических свойств, в том числе и по причине переменного (от партии к партии) качества исходного битума, поступающего на предприятия дорожной отрасли нашей страны.
Использование пластификаторов (масел) на стадии приготовления битумов, модифицированных полимерами, не только не повышает устойчивость последних к расслаиванию, но и способствует разрушению вяжущего в составе дорожного покрытия, вследствие выпотевания (отторжения) масел, в первую очередь, введенных дополнительно. Для получения полимерно-битумных материалов, характеризующихся более высокой пластичностью, достаточно использовать в качестве исходного сырья битумы с более высокими значениями показателя глубины проникания иглы при 25°C, что имеет место в зарубежной практике.
Таким образом, битумы, модифицированные полимерами, представляют собой композиционные материалы, структура и свойства которых при прочих равных условиях зависят от вида и концентрации полимера, марки битума, а также от технологии смешения компонентов.
Для получения модифицированных битумов с заданным комплексом свойств в каждом конкретном случае необходимо осуществлять правильный выбор полимерного модификатора, битумного сырья, выполнять комплекс лабораторных работ по оптимизации рецептуры композиционного материала. Для обеспечения стабильности структуры и свойств битума, модифицированного полимером, при изготовлении разных партий товарной продукции следует использовать полимер и битум постоянного качества, а также строго соблюдать технологический регламент процессов приготовления и хранения модифицированного битума.
Анализ зарубежного и отечественного опыта применения битумов, модифицированных полимерами, показывает принципиальные отличия в подходах к выбору исходных компонентов, к проектированию составов полимерно-битумных вяжущих, к регламентированию комплекса физико-механических свойств ПБВ, к выбору объектов, на которых наиболее целесообразна замена битума дорожного на новый вид вяжущего.
Для объективной оценки зависимости долговечности дорожных покрытий, работающих в сложных климатических условиях Санкт-Петербурга, от вида нефтяного вяжущего, используемого в составе горячей асфальтобетонной смеси, в 1998 г. было проведено опытное строительство участков дорожного покрытия на особо грузонапряженных трассах: Северном проспекте, Дворцовом проезде, а также на Гакелевской улице, с применением битума дорожного улучшенного марки БДУ 70/100 (производства Ухтинского НПЗ) и полимерно-битумного вяжущего. В качестве производителя полимерно-битумного вяжущего был выбран концерн «КОСМОС» (г. Москва), имеющий опыт по устройству дорожного покрытия с применением полимерно-битумного вяжущего на кольцевой дороге в Москве. ПБВ изготавливалось в соответствии с требованиями ОСТ 218.010-98 на промышленной установке концерна «КОСМОС» и доставлялось в Санкт-Петербург битумовозами. Процесс производства и укладки горячих полимер-асфальтобетонных смесей курировался представителями концерна «КОСМОС» и ФГУП «СоюздорНИИ».
Визуальный осмотр, проведенный в 2002 г., показал, что состояние дорожных покрытий на опытных участках Дворцового проезда и Гакелевской улицы, устроенных с применением ПБВ и битума марки БДУ, удовлетворительное. Независимо от вида использованного нефтяного вяжущего, на дорожном покрытии появились отдельные продольные и поперечные трещины, а также разрушения вокруг колодцев (по сравнению с 2001 годом, количество разрушений увеличилось). На всех остановках общественного транспорта, где под верхний слой асфальтобетона укладывалась армирующая сетка «Хателит», наблюдается незначительная колея по полосам наката, которая, по сравнению с 2001 годом, также несколько увеличилась.
Асфальтобетонное и полимер-асфальтобетонное покрытие на опытных участках, устроенных на Северном проспекте, находится в хорошем состоянии: трещин и разрушений нет, перед перекрестком с ул. Есенина в зоне торможения пластические деформации отсутствуют. Наблюдается равномерный незначительный износ покрытия по полосам наката.
По истечении 4 лет эксплуатации в одинаковых условиях принципиальных различий в состоянии покрытий на основе битума марки БДУ и ПБВ не обнаружено. Обращает на себя внимание тот факт, что ПБВ не повысило устойчивость дорожного покрытия к различного рода пластическим деформациям, не предохранило верхний слой покрытия от образования трещин, как отраженных, так и другого характера появления, причиной которых является состояние инженерных сетей и недостаточная несущая способность конструкции дорожной одежды.
Таким образом, по результатам четырехлетнего наблюдения за состоянием полимер-асфальтобетонных покрытий пока не представляется возможным сделать вывод об эксплуатационных преимуществах полимерно-битумного вяжущего, по сравнению с битумом марки БДУ, а следовательно, и целесообразности замены битума БДУ на полимерно-битумное вяжущее для устройства дорожных покрытий на грузонапряженных трассах г. Санкт-Петербурга.
На сегодняшний день одной из важнейших задач, стоящих перед дорожниками Санкт-Петербурга, является повышение срока службы дорожных покрытий на мостах, приведение в порядок трамвайных путей. Условия работы дорожного покрытия на указанных объектах намного более сложные, чем на обычных адресах, в связи с постоянным пребыванием материала под воздействием вибраций, усилий сдвига, растяжения, сжатия и пр. Как показывает опыт Санкт-Петербурга (Финляндии, Германии и др. государств), в таких случаях технически и экономически оправдано применение битумов, модифицированных полимером типа СБС.
В 1999 г. на ОАО «АБЗ-1» (Санкт-Петербург) была введена в эксплуатацию установка по модификации битума периодического действия, разработанная научно-конструкторским бюро Минэкономики РФ. По технологии ЦНКБ модификация битума полимером осуществляется в двух смесителях объемом 2,5 т каждый. Для гомогенизации смеси конструкцией предусмотрены перемешивающие устройства: рама (48,9 об./мин), шнек (34,5 об./мин), а также циркуляция. Окончание процесса приготовления полимерно-битумного вяжущего определяется визуально путем оценки однородности массы при температуре смешения (175–180°C).
В 1999 г. были выпущены по рецептуре, предложенной ЦНКБ, опытные партии полимерно-битумного вяжущего марки ПБВ-90 на основе битума марки БНД 60/90, полимера ДСТ-30 и индустриального масла, которые уложены на Ждановской набережной напротив Петровского стадиона и повороте на Малый проспект.
Анализ физико-механических характеристик ПБВ в пробах, отобранных из опытных партий товарной продукции, показал нестабильность свойств полученного материала, в ряде случаев даже несоответствие требованиям ОСТ 218.010-98. Из-за различия свойств исходных компонентов, поступающих на асфальтобетонный завод (в частности, разных партий битума и ДСТ-30), возникали сложности при проектировании в лаборатории АБЗ рецептуры полимерно-битумного вяжущего, полимер-асфальтобетонной смеси, а также с распределением полимера в массе битума в промышленном смесителе в течение времени перемешивания компонентов, рекомендованном Технологическим регламентом (3–4 часа).
Для обеспечения стабильности качества товарной продукции возникла необходимость в разработке оптимальной рецептуры битума, модифицированного полимером, и в корректировке технологического режима его приготовления.
Учитывая то, что битум дорожный, изготавливаемый из остатков переработки тяжелой нефти Ярегского месторождения (Республика Коми), характеризуется не только стабильностью значений показателей физико-механических свойств в разных промышленных партиях товарной продукции, но и большей растяжимостью, а также повышенной термостабильностью в условиях изготовления горячих асфальтобетонных смесей (по сравнению с битумом марки БНД 60/90), представлялось целесообразным произвести замену битума марки БНД 60/90 в рекомендованной ранее рецептуре полимерно-битумного вяжущего на битум дорожный улучшенный марки БДУ 70/100. В качестве полимерного модификатора для дальнейших работ по выпуску на установке ОАО «АБЗ-1» битума, модифицированного полимером, был выбран полимер «KRATON D1101», широко использующийся для этих целей за рубежом. Комплекс показателей физико-механических свойств указанного полимера как товарного продукта фирмы «KRATON» определенного назначения обусловливает стабильность качества и предопределяет способность его к образованию с нефтяными битумами при температуре 175–180°C гомогенных композиций.
С целью получения максимальной отдачи от введения в битум дорогостоящего полимера корректировке были подвергнуты и нормативные требования к битуму, модифицированному полимером. В 2000 г. были разработаны, а в 2001 году зарегистрированы в органах Госстандарта ТУ 0256-002-03218295-2001 на битум, модифицированный полимером (марки БМП).
В связи с тем, что полимер СБС способен придавать битуму эластические свойства, представлялось целесообразным ужесточить требования к показателю эластичности, по сравнению с требованиями ОСТ 218.010-98: для БМП эластичность определяется через 10 минут, а не после полного прекращения сокращения образца ПБВ, подвергнутого испытанию на растяжимость на дуктилометре. Повышенная эластичность вяжущего обусловливает практически моментальное эластическое восстановление дорожного покрытия после снятия прилагаемой нагрузки до ее повторного приложения, а следовательно, создает предпосылки для повышения долговечности дорожного покрытия.
Для изготовления битумов, модифицированных полимером, способных работать в условиях воздействия разных по виду и величине прилагаемых нагрузок, в ТУ включены несколько марок БМП, различающихся значениями таких показателей качества, как глубина проникания иглы, температура размягчения и др. За основу взяты нормативные требования к качеству модифицированных битумов зарубежного производства. Для обеспечения практической возможности изготовления в условиях асфальтобетонного завода модифицированных битумов разных марок предусмотрено использование в рецептуре композиционного материала специальной добавки, обладающей химическим сродством к битуму дорожному улучшенному – БДУ.
В августе 2000 г. ОАО «АБЗ-1» выпустило в соответствии с ТУ 0256-002-03218295-2001 первую опытную партию вяжущего марки БМП-65 и на его основе изготовило полимерасфальтобетонную смесь. Для отработки технологии укладки смеси с новым видом нефтяного вяжущего в качестве объекта был выбран участок протяженностью 120 м на ул. Бадаева, интенсивность движения по которой не велика. При осмотре опытного участка в 2002 г. разрушений покрытия не обнаружено.
Основным направлением использования битума, модифицированного полимером типа СБС, отработкой технологий изготовления и применения которого, начиная с 2000 г., занимается ОАО «АБЗ-1», является применение его в составе литого асфальтобетона. В 2000 г. было изготовлено 47,5 т БМП, литым асфальтобетоном отремонтированы трамвайные пути по ул. Расстанной (опытный участок 70 м), ул. Инженерной (от здания цирка до Садовой ул.), Большому Сампсониевскому проспекту, Заневскому проспекту до моста Александра Невского и др. Для оценки работоспособности литого асфальтобетона, приготовленного с использованием битума, модифицированного полимером, в более жестких условиях эксплуатации в 2000 г. отремонтированы трамвайные пути на Сампсониевском мосту. При осмотре указанных выше объектов в 2002 г. разрушений не обнаружено.
В 2001 г. для проведения работ по устройству гидроизоляции и дорожного покрытия по металлической ортотропной плите на разводной части моста Александра Невского в зоне проезжей части трамвайных путей и тротуаров ОАО «АБЗ-1» совместно с финскими специалистами фирмы «Леминкяйнен» были использованы литые асфальтобетонные смеси и мастики, изготовленные на основе битума, модифицированного полимером, отвечающего требованиям ТУ 0256-002-03218295-2001. По результатам лабораторных исследований, проведенных финскими специалистами в Финляндии, битум, модифицированный полимером марки БМП в пробах, отобранных из опытных партий, изготовленных на промышленной установке ОАО «АБЗ-1», и литые асфальтобетонные смеси на его основе, полностью отвечали требованиям финских норм. По мнению финских специалистов, применение полимерно-битумного вяжущего позволяет обеспечить гарантийный срок службы покрытия на мосту в течение 3 лет.
В 2002 г. ОАО «АБЗ-1» совместно с немецкой фирмой «FLH Consult G&R» проводило работы по гидроизоляции Троицкого моста через реку Нева. На разводной части моста дорожная одежда была устроена по ортотропной металлической плите (предварительно обработанной эпоксидным праймером) из 2 слоев литого асфальтобетона, изготовленного на промышленной установке ОАО «АБЗ-1» на битуме, модифицированном полимером марки БМП-85 (ТУ 0256-002-03218295-2001). На стационарных пролетах моста литой асфальтобетон на основе БМП использовался как защитный слой. Гарантийные обязательства ОАО «АБЗ-1» на дорожную одежду разводной части моста составляют 3 года, а на гидроизоляцию – 10 лет.
В 2002 г. литые асфальтобетонные смеси применялись также для ремонта трамвайных путей (по ул. Садовой, ул. Б. Дворянской, Среднему проспекту, Каменноостровскому проспекту, Московскому проспекту (угол Обводного канала), площади Восстания, площади Труда, Сенной площади), для устройства покрытий технологических проходов на Автовском путепроводе. Общий объем выпуска БМП на установке ОАО «АБЗ-1» в 2002 г. составил около 315 т.
Одним из перспективных направлений применения битума, модифицированного полимером (марки БМП), является использование в качестве вяжущего при изготовлении щебнемастичных асфальтобетонных смесей (SMA), дорожное покрытие из которых характеризуется повышенной прочностью. Щебнемастичный асфальтобетон широко применяется в верхних слоях дорожных покрытий в Швеции, Норвегии и других странах.
Возрастающий спрос на битум, модифицированный полимером, марки БМП для устройства и ремонта дорожных покрытий на объектах Санкт-Петербурга, обусловлен положительными результатами опытного использования этого вида нефтяного вяжущего в сложных условиях эксплуатации.
Трехлетний опыт производства БМП на промышленной установке ОАО «АБЗ-1» показал, что работоспособность БМП в составе дорожного покрытия зависит от:
Качества исходных материалов;
соблюдения рецептуры;
квалификации обслуживающего персонала;
соблюдения технологических режимов приготовления и хранения.
Специалисты ОАО «АБЗ-1» отмечают, что установка ЦНКБ по приготовлению битума, модифицированного полимером, далека от идеальной модели устройства по приготовлению такого вида композиционного материала для промышленного использования. При этом указывают, что при хранении БМП в статических условиях (без перемешивания) при температуре 150–200°C (технологических температурах изготовления полимерно-битумного вяжущего и укладки литых асфальтобетонных смесей) наблюдаются необратимые изменения в структуре вяжущего, происходит расслоение («желатинизация») массы вяжущего вблизи нагревательных элементов, приводящие к ухудшению физико-механических свойств (снижению значений показателей глубины проникания иглы, температуры размягчения, растяжимости, эластичности). В течение первых суток изменения незначительны и после интенсивного перемешивания могут быть устранены с малым ущербом для качества. При более длительном хранении процесс разрушения структуры БМП становится необратимым.
Таким образом, выводы, сделанные производителями и потребителями промышленных партий битумов, модифицированных полимером типа СБС, полностью совпадают с заключениями, сформулированными российскими и зарубежными учеными на основании результатов научных исследований структуры и свойств этого вида нефтяного вяжущего. При работе с битумами, модифицированными полимерами, нельзя не учитывать особенности их структуры и свойств. Игнорирование этих знаний приведет к снижению эффективности использования полимеров в качестве модифицирующих добавок к битуму, получению некачественных полимерно-битумных материалов, а следовательно, и к неоправданным затратам вследствие применения дорогостоящих полимеров в такой материалоемкой отрасли, как дорожное строительство. При выборе промышленной установки по производству полимерно-битумных вяжущих следует руководствоваться не только соображениями ценовой политики, но и техническими, технологическими возможностями установки, которые должны обеспечивать минимальное влияние на качество товарной продукции известных факторов риска.
Поверхностная обработка состоит в том, что на укатанное и подготовленное, очищенное от пыли дорожное покрытие разливают тонким слоем горячий битум, по которому распределяют каменную мелочь (или крупный песок).
Толщина одиночной поверхностной обработки 1-1,5 и двойной 2,5-4 см. На поверхности дороги создают ровный водонепроницаемый слой с достаточной сопротивляемостью износу и шероховатой поверхностью, обеспечивающей хороший тормозной эффект. Для поверхностной обработки применяют вязкие битумы БНД 130/200 и БНД 200/300, имеющие рабочую температуру 90-150° С, и жидкие битумы МГ 130/200 и СГ 130/200, разогреваемые до температуры 80-100° С.
Технология производства одиночной поверхностной обработки включает следующие операции: подготовку поверхности покрытия для поверхностной обработки (ремонт, исправление поперечного профиля и очистка поверхности от грязи и пыли); предварительный розлив жидкого вяжущего (0,5 -0,8 л/м 2) на покрытие, устроенное без применения черных вяжущих; основной розлив вяжущего по поверхности покрытия с расходом битума (дегтя) 0,7-2,4 л/м 2 ; россыпь в разлитый слой горячего битума минеральных материалов размером 3-15 мм (мелкий щебень, гравий, крупный песок); укатку слоя поверхностной обработки.
Покрытия, на которых предполагается поверхностная обработка, не должны иметь поперечных уклонов свыше 30‰. При большем уклоне их необходимо смягчить с использованием, например, смеси песка с битумом. Покрытия перед поверхностной обработкой следует очистить механическими щетками, подметально-уборочными или поливочно-моечными машинами (2-3 прохода). Покрытия из укрепленных грунтов очищают от комков и пластов засохшей грязи проходами легких грейдеров, при этом металлические щетки следует применять очень осторожно, чтобы не повредить верхний слой укрепленного грунта.
Особенно тщательной очистки требуют поверхность и швы мостовых. На поверхности покрытий, устроенных без черного вяжущего (в частности, гравийных), почти всегда остается некоторое количество пылеватых частиц, которые могут вызвать отслаивание поверхностной обработки от покрытия. Во избежание этого следует создавать слой контакта в виде предварительного розлива, который по возможности лучше делать за 1-2 сут до основных работ. При этом жидкие битумы в теплую погоду можно применять без подогрева.
Вяжущие обычно разливают автогудронатором. Перед розливом их подогревают до рабочей температуры, указанной выше. Через 20-30 мин после розлива слой жидкого битума или дегтя следует засыпать минеральным материалом, в качестве которого лучше всего применять щебень из твердых пород камня; хуже - гравий и крупный песок.
В условиях лесхозов (леспромхозов) приходится применять любой прочный материал, включая дробленые доменные шлаки. Наибольший размер частиц не должен превышать толщину слоя вяжущего более чем на 5 мм. Если сразу после укатки слоя износа идет дождь или наступает похолодание, участок следует закрыть для движения до полного просыхания и последующей укатки. Для лучшего прилипания битума к минеральному заполнителю следует добавлять 1-3% гашеной извести. Минеральный материал удобно рассыпать с помощью навесных распределителей к самосвалам или имеющихся в совхозах, колхозах и отделениях «Сельхозтехники» распределителей минеральных удобрений.
Автомобиль с минеральным материалом должен двигаться задним ходом, при этом колеса должны находиться на рассыпанном слое каменной мелочи. Сразу после распределения минерального материала (до застывания вяжущего) начинают укатку. Обычно используют достаточно тяжелые катки (5-8 т), однако они не должны раздавливать куски минерального материала; при использовании слабых материалов укатку следует выполнять более легкими катками. Хорошие результаты получают при работе катков на пневматиках (любого веса). Окончательную укатку и формирование слоя поверхностной обработки осуществляют под воздействием движущихся машин примерно в течение месяца. При двойной поверхностной обработке после укатки 1-го слоя все остальные операции повторяют.
Если вы нашли ошибку, пожалуйста, выделите фрагмент текста и нажмите Ctrl+Enter .
Защитные слои можно рассматривать одновременно и как слои износа в этом случае их толщину рассчитывают на срок службы покрытия. Такие слои, имеющие назначение защитных и слоев износа, строят на всех покрытиях облегченного типа. Эти покрытия (см. гл.3) строят преимущественно из щебеночных и гравийных материалов, которые после укладки и уплотнения имеют еще остаточную пористость около 20…25%.
В зимний период замерзание воды в пустотах покрытия и в порах минерального материала вызывает их преждевременное разрушение. Поэтому после окончания работ по строительству покрытия немедленно укладывают защитный слой. Этот слой как защитный и как слой износа, определяющий срок службы покрытия до его возобновления, имеет достаточную толщину на износ, водонепроницаемость и шероховатость.
На покрытиях переходного типа щебеночных, гравийных и особенно цементогрунтовых, не обладающих износоустойчивостью, укладывают защитные слои и слои износа с применением органических вяжущих материалов. Такие слои можно считать самостоятельными тонкослойными покрытиями, так как они будут обладать повышенными технико-эксплуатационными показателями, по сравнению с тем покрытием, на которое он уложен.
Слои защитные и слои износа объединяют общие для них способы производства работ: поверхностная обработка способом поливок, укладка слоя готовой смеси, втапливание щебня.
4.1.Устройство поверхностной обработки способом поливок
Поверхностная обработка может быть одиночной или двойной. Общая толщина конструктивных слоев поверхностной обработки составляет от 1,0 до 4,0 см.
Назначение поверхностной обработки на покрытиях переходного типа:
улучшает санитарно-гигиенические условия;
усиливает конструкцию дорожной одежды.
На облегченных покрытиях:
усиливает конструкцию дорожной одежды;
повышает технико-эксплуатационные качества;
делает покрытие более водонепроницаемым.
На капитальных покрытиях:
повышает шероховатость;
предохраняет покрытие от износа;
создает водонепроницаемый слой.
Поверхностную обработку устраивают из самых прочных, износостойких, слабо шлифующихся, водо- и морозостойких материалов. Требования к щебню для поверхностных обработок (табл.4.1).
Таблица 4.1
Требования к щебню для поверхностных обработок
Климатические условия | |||
по прочности |
по морозостойкости |
||
Умеренные Умеренные Умеренные |
Таблица 4.2
Вяжущие материалы для поверхностных обработок и пропиток
Таблица 4.3
Расход материалов для поверхностных обработок
Вид обработки |
Толщина слоя, см |
Фракции щебня, мм |
Номер розлива |
Расход щебня, м 3 /100 м 2 |
Расход битума, |
Одиночная | |||||
Примечания. 1. Нормы расхода приведены для нефтяных битумов. При применении битумных эмульсий расход в пересчете на битум уменьшается на 30…35%, при использовании для обработок черного щебня, что всегда предпочтительнее, расход битума уменьшается на 30…40%, для получения большей шероховатости при интенсивном движении расход битума уменьшают на 40…50% против норм, приведенных в таблице.
При устройстве поверхностных обработок тщательно очищают обрабатываемую поверхность механическими щетками, выполняют ямочный ремонт и подгрунтовку поверхности. Перечень операций при устройстве поверхностной обработки приведен в табл.4.4.
n1.doc
ГЛАВА 20. Строительство слоев износа, защитных шероховатых слоев
20.1. Назначение слоев износа, защитных и шероховатых слоев
При строительстве или реконструкции дорог во многих случаях возникает необходимость строительства слоев износа, защитных и шероховатых слоев, каждый из которых имеет свое основное назначение. Однако во многих случаях их функции совмещаются.Слои износа строят одновременно с покрытием или укладывают на готовое или заканчивающее срок службы покрытие. После уменьшения толщины покрытия за счет износа на расчетную глубину возобновляют слой износа. Этот слой должен обладать требуемой ровностью и шероховатостью, поэтому его строят из самых прочных, износостойких, слабо шлифующихся, водо- и морозостойких материалов. Толщина слоя износа обычно колеблется от 10 до 35 мм.
Защитные слои толщиной от 0,5-1,0 мм до 10-15 мм устраивают для защиты покрытия от проникания в него поверхностной влаги, то есть для гидроизоляции покрытия. Защитные слои можно рассматривать одновременно и как слои износа и рассчитывать их толщину на срок службы покрытия. Слои, имеющие назначение защитных и слоев износа, устраивают на всех покрытиях облегченного типа, которые строят преимущественно из щебеночных и гравийных материалов, поскольку после укладки и уплотнения они имеют еще остаточную пористость около 20-25 %.
В зимний период замерзание воды в пустотах покрытия и в порах минерального материала вызывает их преждевременное разрушение. Поэтому после окончания работ по строительству покрытия немедленно укладывают защитный слой.
На переходных покрытиях и основаниях типа щебеночных, гравийных и особенно цементогрунтовых, не обладающих износоустойчивостью, укладывают защитные слои и слои износа с применением органических вяжущих. Такие слои можно считать самостоятельными тонкослойными покрытиями, так как они будут обладать повышенными технико-эксплуатационными показателями (ровностью, износоустойчивостью, водонепроницаемостью) по сравнению с тем основанием или покрытием, на которое он уложен.
Шероховатые слои различной толщины устраивают для создания шероховатой поверхности на тех покрытиях, у которых параметры шероховатости не обеспечивают требуемые сцепные качества. Основное назначение шероховатых слоев состоит в повышении сцепных качеств покрытий. Коэффициент сцепления зависит от степени и вида шероховатости покрытия и скорости движения (рис. 20.1).
Рис. 20.1. Различные виды шероховатости слоев и покрытий:
1, 2, 3 - непригодные поверхности, излишне гладкие; 4, 5 - небольшая шероховатость, пригодны в городских условиях, при движении со скоростью до 60-70 км/ч; 6, 7 - с крупной шероховатостью, пригодны для движения со скоростью более 80-100 км/ч
Учитывая условия работы перечисленных слоев, каждый из них должен обладать не только свойствами основного назначения, но в той или иной мере свойствами других слоев. Поэтому обычно функции защитных слоев, слоев износа и шероховатых слоев совмещаются путем соответствующего подбора гранулометрического состава, требований к прочности, износостойкости, морозостойкости и другим свойствам каменных материалов, требований к виду вяжущего, его свойствам, нормам расхода, введением различных добавок, а также выбора технологии работ.
Чаще всего устраивают шероховатые коврики износа, которые одновременно выполняют и функции защитных слоев. При этом к толстым относят слои толщиной более 30-35 мм, к тонким - слои толщиной 20-30 мм, очень тонким - слои толщиной 15-20 мм и супертонким - слои толщиной менее 15 мм.
Слои износа, защитные и шероховатые объединяют общие для них способы производства работ: поверхностная обработка, втапливание щебня и укладка слоя смеси, пасты или мастики.
Приведенные на рис. 20.1 поверхности - гладкая 1, с отдельными углублениями 2 и волнистая 3 - не обеспечивают требуемой шероховатости. Для движения со скоростью до 60-70 км/ч допустимы поверхности с малой шероховатостью 4 и 5 с небольшими выступами шероховатости. Для таких слоев применяют мелкозернистый минеральный материал типа крупного песка или острогранных высевок размером 3-8 и 5-10 мм. Получаемые слои сходны с наждачной бумагой. Поверхности с крупной шероховатостью 6, 7 пригодны для движения со скоростью более 80-100 км/ч.
Однако при большой скорости движения в дождливую погоду на гладких покрытиях наблюдается явление гидропланирования (рис. 20.2), когда передние колеса теряют соприкосновение с покрытием из-за слоя воды, плохо отжимаемой из пространств между выступами щебня. При гидропланировании, возникающем на скорости автомобиля свыше 70-100 км/ч, передние колеса не имеют сцепления с покрытием, теряется управление и возможен съезд автомобиля с дороги.
При крупной и равномерной шероховатости слоя гидропланирования не происходит, так как колеса выдавливают воду из углублений между выступами щебня.
Рис. 20.2. Явление гидропланирования на покрытии с мелкой шероховатостью при повышении скорости:
1 - площадь сцепления; 2 - вода
Обеспечение шероховатости. Шероховатость, соответствующая требованиям безопасности дорожного движения, обеспечивается комплексным подходом к проектированию и строительству дорожного покрытия и слоя износа на его поверхности. Обычно, слой износа устраивается с шероховатой поверхностью. Слой износа может представлять собой часть покрытия, не включаемую в расчет по прочности. Слой износа может устраиваться в виде дополнительного тонкого слоя на поверхности покрытия, как правило, из материала, отличного от материала покрытия. В зависимости от требуемого типа шероховатости дорожного покрытия используют различные методы ее устройства (табл. 20.1).
Тип шероховатой поверхности назначают в зависимости от категории дороги: для дорог I категории - С шер или К шер; II категории - С шер, К шер, М шер; III категории - С шер, К шер, М шер, К шип, С шип; IV и V категорий - К шер, С шер, К шип, М шер, М шип.
При создании шероховатой поверхности на покрытиях из асфальтобетонов типа В, В х, Д х путем строительства поверхностной обработки с применением битума, битумной эмульсии или втапливания щебня в поверхность свежеуложенного асфальтобетона размер щебня, использованного для создания шероховатости, и начальная глубина впадин макрошероховатости должны быть рассчитаны. При этом необходимо учитывать интенсивность и скорость движения автомобилей, состав транспортного потока, характеристики атмосферных осадков, требования безопасности движения, необходимый срок службы шероховатой поверхности, требования охраны природы, облегчение содержания дорог в холодный период года. Необходимо учитывать и требования экономики: стоимость строительства должна быть наименьшей, шероховатость - сохраняться в течение заданного периода времени, сопротивление качению автомобильных шин должно быть минимальным. Расчет макрошероховатости заключается в назначении высоты ее неровностей на последний год службы, определении начальной макрошероховатости и микрошероховатости в конце периода работы покрытия или слоя износа, проверке соответствия назначенных параметров макрошероховатости требованиям дренажа воды и др. .
Размер шероховатости поверхностной обработки регулируют подбором размера щебня, однако крупношероховатые поверхностные обработки, устраиваемые из щебня размером 15-20 и 20-25 мм, не рекомендуется применять на участках дорог в пределах населенных пунктов, поскольку они способствуют повышению уровня шума от проезжающих автомобилей.
В районах с частыми снегопадами, большими снегопереносами и гололедом влажный снег и лед забивают зазоры между выступами и повышают скользкость покрытий. Поэтому устройство крупношероховатых покрытий в районах с длительной зимой нецелесообразно. Не имеет смысла устройство шероховатых покрытий в засушливых районах, где основную часть года стоит сухая, жаркая погода.
В зависимости от типа покрытия устраивают одиночную, двойную, а в некоторых случаях тройную обработку, поскольку шероховатая обработка одновременно служит и слоем износа и защитным слоем покрытия. На асфальтобетонных и усовершенствованных облегченных покрытиях устраивают преимущественно одиночную поверхностную обработку, а при ремонте цементобетонных покрытий часто устраивают двойную обработку. Устройство шероховатых поверхностей с применением горячих асфальтобетонных смесей с повышенным содержанием щебня предусматривают на автомобильных дорогах I-III категорий.
Таблица 20.1
Методы устройства шероховатой поверхности на покрытиях дорог (ВСН 38-90)
Тип шероховатости | Методы устройства на покрытиях |
Асфальтобетонные и другие черные покрытия (при новом строительстве и в период эксплуатации) |
|
Мелкошипованные (М шип) | Устройство верхнего слоя покрытий из а/б типа Б, Б х, Г, Г х, Д х с использованием в смесях щебня и дробленого песка из труднополируемых горных пород или щебня разной прочности; |
Поверхностная обработка битумным щебеночным шламом с содержанием до 40 % щебня размером менее 15 мм; |
|
Втапливание черного щебня в поверхность слоя асфальтобетона типов В, В х, Д х; |
|
Устройство слоя износа из песчано-резино-битумных смесей. |
|
Мелкошероховатые (М шер) | Устройство верхнего слоя покрытия из горячего а/б типа А с содержанием в смеси 50-60 % щебня из труднополируемых горных пород размером до 15 мм; |
Устройство верхнего слоя покрытия из открытых битумоминеральных смесей с содержанием в смеси 55-65 % щебня размером до 15 мм; |
|
|
|
Среднешипованные (С шип) | Втапливание черного щебня в поверхность свежеуложенного а/б типа В, В х, Д х; |
Устройство верхнего слоя из открытых битумоминеральных смесей с использованием щебня размером до 20 мм в количестве 55-65 %; |
|
Поверхностная обработка с применением битума, эмульсий и щебня. |
|
Среднешероховатые (С шер) | Поверхностная обработка с применением битума, эмульсий и щебня; |
Поверхностная обработка битумным шламом с использованием щебня размером до 20 мм в количестве не менее 55 %; |
|
Устройство верхнего слоя из открытых битумоминеральных смесей с использованием щебня размером до 20 мм в количестве 65-85 %; |
|
Втапливание черного щебня в поверхность слоя асфальтобетона типа В, В х, Д х. |
|
Крупношипованные (К шип) | |
Крупношероховатые (К шер) | Поверхностная обработка с применением битума, эмульсии и щебня. |
Цементобетонные покрытия (при новом строительстве и в период эксплуатации) |
|
Мелкошипованные (М шип) | При новом строительстве: обработка поверхности свежеуложенного бетона специальными щетками поперек проезжей части; |
В период эксплуатации: а) обработка поверхности покрытия высокотемпературным пламенем, кислотой или другими химическими веществами; б) поверхностная обработка с применением эпоксидного вяжущего и дробленого песка из труднополируемых горных пород. |
|
Мелкошероховатые (M шер) | Нарезка бороздок в поверхностном слое покрытия алмазными дисковыми нарезчиками. |
Среднешероховатые (С шер) | Устройство верхнего слоя из открытых битумоминеральных смесей с использованием щебня размером до 20 мм в количестве 65-85 % или с использованием щебня размером до 25 мм в количестве 55-65 %. |
Крупношипованные (K шип) | Устройство верхнего слоя из открытых битумоминеральных смесей с использованием щебня размером до 25 мм в количестве 65-85 %. |
Крупношероховатые | Двойная поверхностная обработка с применением резинобитумного вяжущего и черного щебня размером 20-25 мм для нижнего слоя и 15-20 мм для верхнего слоя. |
(К шер) |
Втапливание щебня в свежеуложенный слой покрытия применяют на дорогах I-III категорий. На дорогах III и IV категорий с покрытиями из асфальтобетона или из смесей битума с минеральными материалами, приготовленными смешением на дороге, шероховатую поверхность устраивают путем укладки верхнего слоя из холодного асфальтобетона с применением щебня и дробленого песка из труднополируемых пород, а также втапливанием щебня в малощебенистые или песчаные смеси. Следует особо подчеркнуть, что устройство шероховатой поверхности покрытия любым способом теряет всякий смысл, если одновременно не укрепить обочины, съезды и переезды из-за грязи, заносимой с них на покрытие колесами автомобилей во время дождей и распутицы. Поэтому одновременно с устройством шероховатой поверхности необходимо укрепить обочины, устроить твердые покрытия на въездах и переездах.
Для снижения опасности гидропланирования во время дождя в последние годы все большее распространение получают покрытия из высокопористого и открытого асфальтобетона, для которого характерна пористость порядка 15-20 %. Такое покрытие укладывается на слой плотного асфальтобетона с поперечным уклоном не менее 20 ‰. Оно обеспечивает высокий коэффициент сцепления колес с покрытием, так как во время дождя поглощает выпадающие осадки и вода, постепенно дренируя, стекает к обочинам.
Применение дренирующего асфальтобетона может быть рекомендовано на дорогах I-III категорий в V дорожно-климатической зоне.
20.2. Поверхностная обработка дорожных покрытий
Поверхностная обработка - это способ создания шероховатой поверхности покрытия и устройства слоев износа и защитных слоев путем розлива на основание тонкого слоя органического вяжущего, распределения высокосортного щебня и его уплотнения (рис. 20.3). Во многих странах поверхностную обработку называют Chip Seals - щебеночные защитные (изолирующие) слои.Рис. 20.3. Основные технологические операции по устройству поверхностной обработки:
1 - подготовительные работы; 2 - розлив битума; 3 - распределение щебня; 4 - уплотнение щебня; 5 - сметание лишних щебенок
Перед устройством поверхностной обработки дорожное покрытие предварительно должно быть подготовлено. В состав подготовительных работ при устройстве поверхностной обработки на новом покрытии входит:
Очистка покрытия от пыли и грязи;
Установка знаков для организации движения, ограждение места производства работ.
В случаях, когда покрытие не удается полностью очистить от пыли и грязи, оставшейся в мелких трещинках и впадинах, его рекомендуется подгрунтовать путем розлива жидкого битума по норме 0,3-0,5 л/м 2 или битумной эмульсии с расходом 0,5-0,8 л/м 2 .
В состав основных работ входит розлив битума, распределение и уплотнение щебня. После этого производится сметание отдельных не укрепившихся щебенок и открывается движение транспорта. Процесс окончательного формирования поверхностной обработки продолжается около 10 дней, в течение которых скорость движения автомобилей ограничивается и производится ежедневное сметание не укрепившихся щебенок.
Назначение и виды поверхностных обработок. Поверхностная обработка выполняет следующие функции:
Восстанавливает и повышает сцепные качества дорожного покрытия;
Формирует слой износа и защитный слой от проникания воды в дорожную одежду;
Останавливает разрушение и продлевает срок службы старых покрытий, на которых появились признаки износа в виде трещин, шелушения, выкрашивания и другие;
При устройстве на щебеночных и гравийных покрытиях обеспечивает обеспыливание и значительно более комфортные условия движения автомобилей.
Различают несколько видов поверхностной обработки, которые применяют в различных условиях:
одиночная или простая обработка с однократным розливом вяжущего и распределением щебня. Применяется для создания слоя износа и шероховатого слоя на покрытиях с достаточной прочностью и невысокой интенсивностью движения. Толщина слоя составляет 1,5-2,5 см;
одиночная или простая обработка с двойным распределением щебня . На слой разлитого вяжущего сначала распределяют более крупную фракцию щебня (например, 8/11 или 15-20 мм), прикатывают катком, а затем распределяют более мелкую фракцию щебня (например, 2/5 или 5-10 мм) и уплотняют. Применяется на дорогах с высокой скоростью движения автомобилей. Толщина слоя может составлять 3-4 см;
простая обработка типа сэндвич. На поверхность покрытия распределяют крупную фракцию щебня, затем разливают вяжущее, распределяют мелкую фракцию щебня и уплотняют. Применяется при неоднородном по ровности основании для выравнивания и некоторого усиления;
двойная поверхностная обработка или поверхностная обработка типа двойной «сэндвич». На первый слой разлитого вяжущего распределяют крупную фракцию щебня и уплотняют. Затем разливают второй слой вяжущего, распределяют более мелкую фракцию щебня и окончательно уплотняют. Толщина слоя составляет 3-4 см. Применяется на покрытиях с недостаточной прочностью, при наличии сетки трещин, ямочности, колей, при высокой интенсивности движения, то есть в тех случаях, когда необходимо не только создать шероховатый слой износа и защитный слой, но и улучшить ровность, несколько повысить прочность и сдвигоустойчивость. Применяется также на цементобетонных покрытиях;
двойная поверхностная обработка с прослойкой из щебня. На очищенное и выровненное гравийное или щебеночное покрытие рассыпают прослойку из щебня крупной фракции и уплотняют. Затем разливают первый слой вяжущего, распределяют более мелкую фракцию щебня и уплотняют. После этого разливают второй слой вяжущего, распределяют щебень мелкой фракции и окончательно уплотняют. Толщина слоя может достигать 5 см. Применяется на «белых» гравийно-щебеночных покрытияхдля перевода их в «черное» шоссе.
Требования к каменным материалам для поверхностной обработки. Для поверхностной обработки применяют щебень из высокопрочных изверженных или метаморфических горных пород с прочностью более 100-120 МПа и износом при истирании в барабане Деваля не более 35 %.
Для дорог с малой интенсивностью движения допускается применять щебень из осадочных пород (известняк) прочностью не менее 80 МПа с истиранием не более 40 %. Щебень должен быть мытым: чистым и без пыли. Доля зерен мельче 0,63 мм не должна превышать 0,5 %. Зерна щебня должны быть одномерными узких фракций кубовидной формы.
В целях экономии дорогостоящего высокопрочного щебня на дорогах со средней интенсивностью движения можно устраивать поверхностную обработку из смеси разнопрочных каменных материалов, в которой 50 % и более составляет щебень прочностью 100 МПа и выше и до 50 % щебень прочностью 60-80 МПа. Опыт показывает, что в процессе эксплуатации более слабые щебенки истираются быстрее и уменьшаются по высоте, а более прочные щебенки выступают из покрытия и обеспечивают хорошие сцепные свойства мокрого покрытия.
По европейским стандартам применяют размер фракций щебня, мм - 2/5; 5/8; 8/11; 11/16 . В России допускается более широкий диапазон размера фракций, мм - 5-10; 10-15; 15-20 и 20-25 . Однако в последние годы наметилась тенденция к переходу на более мелкие размеры и более узкие фракции щебня, близкие к европейским стандартам.
Требования к однородности материала по предельным размерам основаны на опыте срока службы поверхностной обработки. Необходимо, чтобы все щебенки прочно прилипли гранями к разлитому вяжущему. При однородном щебне, рассыпаемом в один слой (рис. 20.4, а), этого можно достигнуть. В разнородном материале всегда найдутся мелкие зерна, которые будут лежать сверху и не получат должного сцепления с битумом (рис. 20.4, б). Под воздействием касательных усилий колес автомобилей эти щебенки вырываются и вылетают в стороны, покрытие получается неровным и необходимы дополнительные, проводимые часто вручную работы по заметанию щебенок с обочины на покрытие.
Рис. 20.4. Поверхностная обработка: 1 - вяжущее; 2 - щебень, не удерживаемый вяжущим; 3 - щебень, удерживаемый вяжущим
Вылетающие из-под колес щебенки опасны, травмируют проезжающих и пешеходов, разбивают стекла автомобилей.
Выбор размера фракций зависит от многих факторов, в том числе от того, какие транспортно-эксплуатационные характеристики покрытия необходимо получить, при какой интенсивности, в каком составе движения работает покрытие и в каких климатических условиях, а также от состояния старого покрытия и его твердости. Так, для получения водонепроницаемого защитного слоя небольшой толщины на местных проездах и площадях в населенных пунктах применяют щебень фракций 2/5, который создает мелкую шероховатость типа наждачной бумаги. Фракции 5/8 обеспечивают хорошую шероховатость на прочных и ровных покрытиях при минимальном уровне звуковой эмиссии. Более глубокую шероховатость, больший износ шин и уровень звуковой эмиссии создает поверхностная обработка из щебня фракций 8/11 и 11/16, однако она более долговечна при интенсивном движении и более эффективна на мягких покрытиях. На очень мягких покрытиях в районах с жарким климатом в России применяют щебень фракций 15-20 и даже 20-25 мм.
Для определения жесткости или твердости старого покрытия применяют твердомеры. Чтобы привести результаты измерений, выполненных при разной температуре, к сопоставимому виду, их приводят к расчетной температуре (рис. 20.5).
Для устройства поверхностной обработки применяют щебень, предварительно обработанный небольшим количеством органического вяжущего или чистый щебень. Для обработки щебень разогревают до температуры 170-180°С, загружают в мешалку, куда впрыскивают горячий битум в количестве 1-1,5 % от массы щебня и перемешивают. Получают так называемый черный щебень. Такая обработка часто используется при устройстве шероховатых слоев на дорогах в северных районах.
Считается, что в обработанном щебне битум проникает в микропоры и закрывает их для проникания воды, вследствие чего повышается водостойкость и морозоустойчивость щебня, который применяют на дорогах с высокой интенсивностью движения и в районах с холодным влажным климатом. Необработанный щебень применяют на дорогах с интенсивностью движения до 1000 авт./сут, а также для второй россыпи при устройстве поверхностной обработки с двухкратным распределением щебня.
Рис. 20.5. Оценка твердости покрытия:
Зоны жесткости: 1 - очень мягкое; 2 - мягкое; 3 - нормальное; 4 - твердое; 5 - очень твердое.
Однако можно предположить, что наличие пленки битума в порах обработанного щебня может препятствовать прониканию в них битумной эмульсии или битума, разлитого на покрытии и, наоборот, битумная эмульсия хорошо взаимодействует со свежей чистой поверхностью щебенок, глубоко проникает в микропоры и тем самым обеспечивает более прочные связи минеральных материалов. Поэтому необработанный щебень находит все большее применение для поверхностной обработки.
Требования к вяжущим для поверхностной обработки. В качестве вяжущих для устройства поверхностных обработок применяют в основном битумные эмульсии и, в меньших объемах, битум. В России чаще применяют вязкие битумы БНД 60/90, БНД 90/130, БНД 130/200, МГ 130/200, МГ 70/130.
Благодаря водному характеру битумной эмульсии она обладает высокой смачивающей способностью поверхности щебня. При распаде эмульсии происходит адгезия (сцепление) битума с каменным материалом и одновременным вытеснением воды с поверхности каменного материала.
Обычно применяют катионные битумные эмульсии, в которых капельки битума имеют положительный электрический заряд, а поверхность каменного материала получает отрицательный заряд. Происходит обмен зарядами, что означает начало распада битумной эмульсии, после чего битум входит в жесткое сцепление с поверхностью щебня.
В современной технологии применяют высококонцентрированные битумные эмульсии типа ЭБК-2, в которых содержание битума составляет 65-70 %. Поскольку такие эмульсии имеют сравнительно высокую вязкость, их перед применением подогревают до 50-70°С для удобства обработки.
Для улучшения реологических и других физических свойств битумных эмульсий в настоящее время широко применяют добавки полимеров.
Битумные эмульсии, модифицированные полимерами, должны иметь температуру удара в тепле минимум 60-65°С и температуру удара в холоде минимум минус 5°С. Кроме эмульсий для поверхностной обработки часто применяют модифицированный полимерами горячий битум (табл. 20.2). В России это битум вязкий БНД 130/200 и БНД 90/130.
При использовании в качестве вяжущего битумной эмульсии расход эмульсии и щебня должен соответствовать нормам, приведенным в табл. 20.3.
Во Франции норма расхода битума для поверхностной обработки на старых покрытиях принята равной 10 % от расхода щебня, из них 8 % идет на обеспечение связи щебенок между собой и с основанием и 2 % на герметизацию мелких трещин в старом покрытии (табл. 20.4).
Принципиальный подход к назначению нормы расхода щебня состоит в том, чтобы его было достаточно для создания плотного каменного скелета, а количество вяжущего назначается из условия, что вяжущее должно обеспечить обволакивание всех щебенок на высоту 2/3 от размера щебенок и герметизацию старого покрытия .
Организация работ по устройству поверхностной обработки. Поверхностную обработку устраивают обычно летом в сухую погоду при температуре воздуха не ниже 15°С. Допускается выполнять работы при температуре воздуха 5°С весной и 10°С осенью.
При использовании в качестве вяжущего битумной эмульсии поверхностную обработку можно устраивать на влажном покрытии и при небольшом дожде.
При использовании в качестве вяжущего горячего вязкого битума все работы должны быть выполнены за время, пока температура битума не опустилась ниже допустимой по загустеванию битума. При розливе битума температура должна поддерживаться:
Для вязких битумов марок БНД 60/90, БНД 90/130, БН 60/90 и БН 90/130 в пределах 150-160°С;
Для марок БНД 130/200 и БН 130/200 в пределах 100-130°С;
Для полимербитумных вяжущих в пределах 140-160°С;
Для дегтеполимерного вяжущего в пределах 100-110°С.
Таблица 20.2
Нормы розлива вяжущих и распределения щебня при устройстве поверхностных обработок
Вид поверхностной обработки | Фракция щебня, мм | Расход щебня | Расход вяжущего, л/м 2 |
|
кг/м 2 | м 3 /100 м 2 |
|||
Одиночная на вязком битуме | 5-10 | 11-15 | 0,9-1,1 | 0,7-1,0 |
10-15 | 15-20 | 1,1-1,4 1,2-1,5 | 0,9-1,0 1,0-1,3 |
|
20-25 | 25-30 | 1,4-1,6 | 1,1-1,4 |
|
Одиночная на вязком битуме с двукратной россыпью щебня | Первая россыпь 15-25 | 16-18 | 1,2-1,4 | 1,4-1,5 |
Вторая россыпь 5-10 | 6-8 | 0,6-0,8 | - |
|
Одиночная на 50% битумной эмульсии | 5-10 | 12-15 | 0,9-1,1 | 1,6-1,8 |
10-15 | 15-20 | 1,2-1,4 | 1,8-2,0 |
|
15-20 | 20-25 | 1,3-1,5 | 2,0-2,4 |
|
20-25 | 25-30 | 1,4-1,6 | 2,4-2,6 |
|
Двойная на вязком битуме | Первая россыпь | первый розлив |
||
15-25 или | 20-25 | 1,2-1,5 | 1,1-1,4 |
|
20-25 | 25-303 | 1,4-1,6 | ||
Вторая россыпь | второй розлив |
|||
5-10 или | 15-20 | 1,2-1,3 | 0,6-0,8 |
|
10-15 | 15-20 | 11,2-1,4 |
Примечание. При применении необработанного щебня нормы розлива битума повышают на 20 %. Фракцию щебня для одиночной поверхностной обработки выбирают по расчету и в зависимости от твердости покрытия
Таблица 20.3
Способ обработки | Размер щебня, мм | Расход щебня, м 3 /100 м 2 | Расход эмульсии, л/м 2 , при концентрации битума, % |
|
60 | 50 |
|||
Одиночная | 5-10 | 0,9-1,1 1,2-1,4 | 1,3-1,5 1,7-2,0 | 1,5-1,8 2,0-2,4 |
Двойная | 15-20 | 1,1-1,3 | 1,5-1,8 | 1,8-2,2 |
Первая россыпь | Первый розлив |
|||
5-10 | 0,7-1,0 | 1,3-1,5 | 1,5-1,8 |
|
Вторая россыпь | Второй розлив |
Таблица 20.4
Температуру и концентрацию эмульсии устанавливают в зависимости от погодных условий следующим образом:
При температуре воздуха ниже +20°С эмульсия должна иметь температуру от 40 до 50°С (при концентрации битума в эмульсии 55-60 %). Подогрев эмульсии до такой температуры осуществляется непосредственно автогудронатором;
При температуре воздуха выше +20°С эмульсия (при концентрации битума в эмульсии 50 %) может иметь такую же температуру, но не менее.
Для прочного сцепления битумной эмульсии с обрабатываемым покрытием необходимо обеспечить его чистоту. Очистку покрытия выполняют непосредственно перед началом поверхностной обработки. При сухой жаркой погоде покрытие увлажняют (0,5 л/м 2) непосредственно перед основным розливом эмульсии. Температура и концентрация эмульсии устанавливаются в зависимости от погодных условий: при температуре воздуха ниже 20°С применяют эмульсию с концентрацией битума 55-60 % и температурой 40-50°С; при температуре воздуха выше 20°С подогревать эмульсию не надо и концентрацию битума можно уменьшить до 50 %. Вязкость эмульсии должна быть в пределах 15-30 с.
Распределение эмульсии и щебня может производиться раздельно и синхронно. При раздельном распределении первоначально эмульсию разливают в количестве 30 % нормы и рассыпают 70 % нормы щебня. Сразу после этого разливают остальное количество эмульсии (70 %) и распределяют оставшийся щебень. Щебнераспределитель должен двигаться как можно ближе к автогудронатору и рассыпать щебень перед собой. Уплотнение (самоходные катки на пневмоходу или с обрезиненными вальцами совершают 4-5 проходов со скоростью до 5 км/ч) начинается с момента начала распада эмульсии и заканчивается в момент его окончания. При синхронном распределении эмульсия и щебень попадают на покрытие с интервалом времени не более 1 с. При таких условиях эмульсия успевает до начала распада заполнить поры покрытия и щебня и тем самым создать благоприятные условия для последующего уплотнения поверхностной обработки.
Основной розлив вяжущего производят, как правило, по одной половине проезжей части или на ширину одной полосы движения в один прием без пропусков и разрывов. Если можно организовать движение транспортного потока по объезду, розлив вяжущего и распределение щебня целесообразно выполнять на всю ширину проезжей части одновременно или с небольшим уступом. Это позволит избежать образования продольных шов в поверхностной обработке.
При определении длины сменной захватки и подборе состава машин необходимо исходить из того, что все работы по распределению битумной эмульсии и щебня и по уплотнению должны быть закончены за время распада эмульсии, который легко определить визуально по внешнему виду, когда коричневый цвет эмульсии сменится темным.
Распределение щебня необходимо выполнять как можно быстрее после розлива вяжущего. Поэтому щебнераспределитель должен идти сразу за гудронатором. Распределители щебня бывают самоходными или навесными на автомобилях-самосвалах. В любом случае распределитель щебня работает по схеме «от себя», то есть так, чтобы его колеса двигались по уже распределенному щебню, а не по слою вяжущего. Для этого автомобиль с навесным распределителем движется задним ходом.
Общий состав основного звена машин для поверхностной обработки состоит из машины для очистки покрытия от пыли и грязи, автогудронатора, распределителя щебня (одного или двух), звена катков и машины для подметания лишнего щебня. Уплотнение начинают сразу после распределения щебня сначала средним катком за два-три прохода по одному месту со скоростью 10-15 км/ч, а затем тяжелым катком не менее чем по два-три прохода по одному месту. Лучшие результаты получают, когда для уплотнения применяют самоходные катки на пневматических шинах.
В процессе уплотнения необходимо учитывать особенности устройства различных видов поверхностных обработок. Простые поверхностные обработки с двойным распределением щебня уплотняют только после второго распределения щебня. Оба слоя должны очень быстро укладываться друг за другом, а последующее уплотнение производиться очень интенсивно пятью проходами катка по одному следу. При поверхностных обработках типа сэндвич первый слой щебня также не уплотняется и уплотнение начинается после распределения второго (верхнего) слоя щебня. При двойных обработках уплотнение начинается после первого распределения щебня. Затем немедленно укладывается и уплотняется второй слой.
Уход за поверхностной обработкой. После уплотнения катками и завершения распада эмульсии открывают движение по поверхностной обработке. В течение первого периода, который составляет 3-10 дней, необходимо обеспечить движение автомобилей со скоростью не более 40 км/час, чтобы лишний щебень не вылетал из-под колес и не мог разбить стекла автомобиля. Лишний щебень в первые дни регулярно убирают сметающими или всасывающими машинами. В течение нескольких дней битум под действием тепла и движущегося транспорта поднимется и покроет все щебенки тонким слоем, придав поверхности однородный цвет.
Поверхностная обработка с синхронным распределением вяжущего и щебня. Качество поверхностной обработки во многом зависит от надежности работы системы «вяжущее-щебень» и «щебень-вяжущее-основание».
Опыт эксплуатации поверхностных обработок показал, что наиболее эффективно это взаимодействие, когда вяжущее заполняет зону контакта между смежными щебенками на высоту h, которая должна быть равна 2/3 высоты щебенки, то есть
h = 2/3 D , где
h - высота слоя вяжущего в зоне контакта смежных щебенок, мм;
D - размер щебенки по высоте, мм.
Установлено, что до 80 % дефектов поверхностной обработки составляют отделения и выкрашивания щебенок вследствие недостаточной связи в зоне их контакта.
Надежное сопряжение щебенок друг с другом происходит за счет выдавливания вяжущего в зазоры между щебенками и дальнейшего продвижения вверх по законам капиллярного поднятия. Высота этого поднятия зависит от размеров зазоров между щебенками и вязкости вяжущего (рис. 20.6). Вяжущее с невысокой вязкостью в капиллярах образует глубокий мениск и поднимается на большую высоту, обволакивая щебенку тонким слоем (рис. 20.6, а). Вяжущее с высокой вязкостью не позволяет образоваться мениску, поднимается на небольшую высоту, оставляя значительную часть щебенок без пленки вяжущего (рис. 20.6, б). В процессе эксплуатации связи между такими щебенками ослабляются и они отделяются от покрытия, происходит выкрашивание.
Рис. 20.6. Варианты сопряжения щебня с покрытием:
а - при нормальном поднятии битума с образованием высокого мениска;
б - при недостаточном поднятии битума без образования мениска
Чтобы уменьшить вязкость битума в процессе устройства поверхностной обработки, его подогревают и распределяют при температуре 140-160°С. Однако разлитый по поверхности покрытия горячий битум толщиной пленки 0,5-2,0 мм очень быстро остывает. При этом его вязкость также быстро увеличивается и к моменту распределения щебня может достичь значительной величины.
Высококонцентрированные битумные эмульсии тоже обладают сравнительно высокой вязкостью и поэтому их перед распределением рекомендуется подогревать до 50-70°С. Кроме того в битумной эмульсии после распределения начинается процесс быстрого распада, до окончания которого щебень уже должен быть распределен. Таким образом, на качество поверхностной обработки большое влияние оказывает период времени от розлива вяжущего до распределения щебня t (рис. 20.7).
Рис. 20.7. Интервал времени между распределением вяжущего и щебня
При обычном, асинхронном распределении вяжущего и щебня, когда вяжущее распределяется автогудронатором, а щебень идущим за ним на расстоянии 10-100 м и более щебнераспределителем, промежуток времени t составляет от 5 с при очень четкой работе машин до 10 мин и более при небольших задержках с распределением щебня. Поэтому задача сокращения периода между распределением вяжущего и щебня является задачей повышения качества и долговечности поверхностной обработки.
Эта задача успешно решена в технологии устройства поверхностной обработки с синхронным распределением вяжущего и щебня. Для этого созданы комбинированные машины и оборудование для распределения вяжущего и щебня с интервалом времени всего в 1 с. Для поверхностной обработки с синхронным распределением вяжущего и щебня в России применяют машины БЩР-375 и битумощебнераспределители Саратовского ФГУП Росдортех типа Чипсилер-40 и Рипсилер-26 (рис. 20.8). Производительность указанных машин составляет 3-6 км/ч.
Машина состоит из емкости для вяжущего с подогревом, кузова для щебня, системы распределения вяжущего, щебнераспределителя и специальной консоли (площадки) оператора с пультом автоматизированного управления рабочими органами машины и процессом распределения. Кузов автомобиля разделен поперечными перегородками, позволяющими расходовать щебень частями. Система распределения вяжущего состоит из плоскоструйных форсунок, расположенных на одной поперечной балке на расстоянии 10 см одна от другой с общей шириной распределения до 4 м. Вяжущее из форсунок распределяется под давлением в виде мельчайших частичек и покрывает покрытие тонким равномерным слоем. Каждая форсунка имеет автономное включение и выключение, что обеспечивает возможность гибкого регулирования ширины распределения вяжущего (битума или битумной эмульсии).
Щебнераспределитель оригинальной конструкции позволяет распределять фракции размером 2-20 мм слоем в одну щебенку. Для лучшего формирования рассыпанный щебень необходимо немедленно уплотнить катками на пневматических шинах или катками с обрезиненными вальцами.
Рис. 20.8. Комбинированная машина «Чипсилер» фирмы «СЭКМЭР» для синхронного распределения вяжущего и щебня:
1 - емкость для вяжущего; 2 - кузов для щебня; 3 - распределитель вяжущего; 4 - щебнераспределитель; 5 - рабочая площадка оператора с пультом управления
20.3. Поверхностные обработки с полимерным вяжущим
Полимерные вяжущие позволяют создавать прочный водонепроницаемый шероховатый слой поверхностной обработки и этим увеличивать срок службы ее и покрытия, на которое она уложена. Из-за высокой стоимости полимерные вяжущие пока широко не применяются для строительства покрытий, но нашли применение для защитных слоев и слоев износа по способу поверхностной обработки. В настоящее время многие полимерные материалы применяют для строительства шероховатых слоев износа, что позволяет быстро открыть дорогу для движения.Наиболее экономично и эффективно комплексное вяжущее, составленное путем добавки к битуму или дегтю полимерного материала, например, резиновой крошки или полимерной смолы. При массовой доле в каменноугольном дегте 10 % эпоксидной смолы дорога с такой поверхностной обработкой может быть открыта для движения без ограничения скорости через несколько часов после окончания работ. Работами МАДИ доказана эффективность применения в качестве добавки к битуму резиновой крошки, поливинилхлорида (ПВХ). Добавка 2-7 % ПВХ настолько повышает эффективность сцепления, что уже через 2-3 сут можно не ограничивать движения. ПВХ - белый порошок, добавляемый к битуму в котел; после их смешивания получают комплексное вяжущее.
В Великобритании и других странах применяют способ «шеллгрипп», при котором укладывают преимущественно на цементо- и асфальтобетонных покрытиях слои около 5 мм. Вяжущее состоит из смеси эпоксидной смолы со смолой другого вида на основе битума, перемешиваемых в пропорции 1:1. Полученное вяжущее характеризуется быстрым твердением, придает слою прочность и эластичность. Минеральным материалом служит материал, синтезированный из кальцинированного боксита (обычно используемого как огнеупорный материал), размером 1-3 мм. Он обладает большей износостойкостью и шероховатостью, чем каменные материалы. Расход вяжущего составляет 1,25-1,5 кг/м 2 , минерального материала 5-6 кг/м 2 . В США на основе эпоксидной смолы применяют комплексные вяжущие под фирменными названиями «гуардкот» и «редкот», которые распределяют автогудронаторами.
На основании лабораторных и опытных работ Союздорнии предлагает эпоксидное вяжущее следующего состава: эпоксидной смолы ЭД-5 или ЭД-6 - 100 частей по массе; пластификатор дибутилфталат - 20-25 частей, отвердитель полиэтиленполиамин - 8-10 частей. Расход вяжущего 100 г/м 2 . В качестве минерального материала применяют промытый, высушенный песок или высевки твердых горных пород. Минеральный материал в количестве 0,8-1 кг/м 2 рассыпают через 5-10 мин после распределения вяжущего, вдавливают в вяжущее катком, прокатываемым вручную. Так как перемешивание и распределение эпоксидного вяжущего затруднительны ввиду его вязкости и токсичности, во Франции выпускаются передвижные смесители, подающие и распределяющие вяжущее через шланг под высоким давлением. В США предложена машина (рис. 20.9) в виде прицепа к тягачу, которая имеет хранилища для компонентов эпоксидного вяжущего, дозатор для выделения порции каждого из них в мешалку, периодически выдающую небольшие порции вяжущего.
Рис. 20.9. Машина для приготовления вяжущего на основе эпоксидной смолы:
1 - жаровая труба; 2 - кран; 3 - общая труба; 4 - смесительная колонка; 5 - мешалка со шнеком; 6 - насос; 7 - бензиновый двигатель; 8 - двигатель для привода лопастей мешалки; 9 - насос для нагнетания отвердителя
20.4. Устройство шероховатого слоя износа методом втапливания щебня
Одним из высокоэффективных и экономичных способов создания прочного, шероховатого и износостойкого слоя, особенно на дорогах с интенсивным движением грузовых автомобилей и автомобилей с шипами, является способ втапливания щебня.Втапливание щебня - это способ устройства шероховатого слоя износа путем укладки тонким слоем песчаной или мелкозернистой малощебенистой асфальтобетонной смеси типа В или Д, ее предварительного уплотнения, немедленного распределения прочного щебня слоем в одну щебенку и вдавливания (втапливания) его катками в слой свежеуложенного асфальтобетона. Толщина слоя асфальтобетона должна быть не менее 3 см (рис. 20.10).
Рис. 20.10. Схема втапливания щебня в слой уложенной асфальтобетонной смеси:
1 - нижний слой асфальтобетонного покрытия; 2 - разлитое вяжущее; 3 - асфальтобетонная смесь для верхнего слоя; 4 - рассыпанный одномерный щебень; 5 - щебень после уплотнения, втопленный в асфальтобетонную смесь
Щебень, который втапливают в асфальтобетонную смесь, должен быть приготовлен из прочных, I-II класса прочности износостойких и малошлифующихся изверженных и метаморфических горных пород или аналогичных им по качеству шлаков. Используется одномерный щебень размерами 10-15, 15-20 или 20-25 мм, обработанный битумом с расходом 1-1,3 % от массы щебня.
Обработка щебня вяжущим осуществляется в асфальтобетонном смесителе при температурах 140-170°С при использовании битумов БНД 60/90 и БНД 90/130; при температурах 110-160°С при использовании битумов СГ 130/200, МГ 130/200; при температурах 80-120°С при использовании битумов СГ 70/130, МГ 70/130. Вяжущее должно полностью обволакивать щебень и не стекать с него. Целесообразно осуществлять обработку щебня вспененным битумом. Для повышения сцепления вяжущего с щебнем используются ПАВ.
Температура нагрева щебня и вяжущего при смешении зависит от марки последнего, температуры и влажности воздуха (табл. 20.5). При большей влажности и холодной погоде необходимо придерживаться верхних пределов температуры вяжущих.
Лучшие результаты по качеству шероховатого слоя достигаются при втапливании горячего черного щебня в горячий асфальтобетон. Такая технология возможна при наличии одного смесителя для синхронного приготовления черного щебня и другого смесителя для приготовления асфальтобетона. Возможно втапливание холодного черного щебня в горячий асфальтобетон, при этом щебень должен обрабатываться вяжущим заблаговременно (например, в зимний период).
Таблица 20.5
Марка вяжущего | Температура нагрева, °С |
|
вяжущего | щебня |
|
БНД 60/90, 90/130 | 140-160 | 150-170 |
БНД 130/200, 200/300 | 110-130 | 120-160 |
СГ 130/200 | 90-120 | 110-130 |
СГ 70/130 | 80-100 | 100-120 |
Щебень и вяжущее тщательно дозируют. Щебень, обработанный вяжущим, при применении его горячим сразу после приготовления доставляют к месту строительства и укладывают на покрытие. Холодный щебень можно хранить до 4-8 месяцев на складе. Применение горячего щебня повышает качество шероховатого покрытия, но требует более высокой культуры труда.
Слои износа по способу втапливания щебня применяют при строительстве новых покрытий, при реконструкции, усилении и ремонте, любых типов капитальных и переходных покрытий.
При строительстве асфальтобетонного покрытия немедленно после распределения смеси асфальтоукладчиком рассыпают одномерный щебень с последующим уплотнением смеси и одновременным втапливанием щебня. Щебень распределяют самоходным распределителем или распределителем, работающим на прицепе к асфальтоукладчику (рис. 20.11). Для погрузки в бункер распределителя щебня, доставляемого автомобилями-самосвалами, применяют ковшовые погрузчики.
Рис. 20.11. Технологическая последовательность строительства покрытия с втапливанием в него щебня распределителем на прицепе к асфальтоукладчику:
1 - автомобиль-самосвал; 2 - асфальтоукладчик; 3 - щебнераспределитель; 4 - каток
При реконструкции, усилении или ремонте покрытий для применения способа втапливания предварительно подготавливают старое покрытие как для поверхностной обработки.
Технология работ включает следующие операции (рис. 20.12):
Очистка покрытия от пыли и грязи, ямочный ремонт, заливка трещин, устранение неровностей;
Подгрунтовка, то есть розлив жидкого битума или битумной эмульсии с расходом соответственно 0,3-0,5 л/м 2 или 0,5-0,8 л/м 2 ;
Укладка малощебенистой или песчаной асфальтобетонной смеси слоем 2-4 см и предварительное уплотнение трамбующим брусом асфальтоукладчика. Эта операция производится, когда подгрунтовка впитается или загустеет;
Немедленное распределение щебня слоем в одну щебенку при помощи щебнераспределителя с боковой загрузкой или с загрузкой его грейферным погрузчиком из самосвала, идущего сбоку от щебнераспределителя. Расход щебня зависит от размера фракции:
Щебень фракции (5-10) мм - (03-1,1) м 3 /100 м 2 ;
Щебень фракции (10-15) мм - (1,1-1,2) м 3 /100 м 2 ;
Щебень фракции (15-20) мм - (1,2-1,4) м 3 /100 м 2 .
Во время распределения щебня температура уложенной смеси на покрытии должна быть не менее 90-110°С для горячих смесей и 60-80°С для теплых;
Втапливание щебня за один-два прохода легких катков и немедленная укатка средними и тяжелыми катками на пневматическом ходу при постепенном повышении скорости их движения от 2 до 15 км/ч.
Число проходов катков и продолжительность укатки устанавливают в зависимости от толщины уложенного слоя, типа смеси и ее температуры и температуры окружающего воздуха. Так, при толщине слоя 4 см и температуре воздуха 20°С число проходов средних катков составляет 4-5, а тяжелых 8-10.
Рис. 20.12. Основные технологические операции по устройству шероховатого слоя износа методом втапливания:
1 - подготовительные работы; 2 - подгрунтовка; 3 - укладка и предварительное уплотнение смеси; 4 - распределение щебня; 5 - втапливание щебня и укатка
В результате уплотнения щебенки втапливаются в слой асфальтобетона на 0,8-0,9 своей высоты и образуют вместе с асфальтобетонной смесью монолитный слой с шероховатой поверхностью. Такая конструкция слоя называется «щебень в обойме».
Срок службы слоя износа из втопленного щебня 6-10 лет при интенсивном и тяжелом движении.
В Австрии, Венгрии и ряде других стран применяется другая технология устройства шероховатого слоя износа методом втапливания. Отличие состоит в составе асфальтобетонной смеси, степени ее предварительного уплотнения. В такую смесь входит 35-40 % щебня, полученного путем дробления мелкого гравия с размером щебенок до 15 мм (максимум до 20 мм), около 55 % песка, 8 % минерального порошка и около 8 % модифицированного битума с пенетрацией 50.
Горячую асфальтобетонную смесь укладывают толщиной 3,5-4 см и сразу уплотняют вибробрусом асфальтоукладчика до степени уплотнения 0,85. Немедленно на горячий слой распределяют слоем в одну щебенку черный щебень фракций 12-20 мм с расходом 10-12 кг/м 2 и втапливают гладковальцовыми вибрационными катками.
Щебень для втапливания получают дроблением прочных гранитных пород и обрабатывают его в установке модифицированным вязким битумом с пенетрацией 30-40 и расходом 1 % от массы щебня. При этом щебень нагревают до 220°С, а битум до 180°С.
После перемешивания обработанный щебень охлаждают водой и используют для втапливания. В результате получают плотный, очень прочный и шероховатый слой износа с высокими сцепными качествами. Эти слои отличаются большей шероховатостью и значительно большим сроком службы, чем слои износа, построенные по способу поверхностной обработки с применением тех же вяжущих и минеральных материалов.
20.5. Слои износа и защитные слои с применением эмульсионно-минеральных смесей
Для строительства слоев износа и защитных слоев дорожных покрытий широкое применение получили холодные эмульсионно-минеральные смеси различного состава. В зависимости от конкретного состава, технологии применения в различных странах эти смеси называют литыми эмульсионно-минеральными смесями (ЛЭМС), «Сларри Сил», литой холодный микроасфальт, рапид-асфальт и др. Достоинство этих слоев в сравнительно простой технологии устройства, малого расхода материалов, высокой производительности при укладке, небольших помехах для движения транспорта по участку, где ведутся работы.Литые эмульсионно-минеральные смеси (ЛЭМС) состоят из минеральных материалов (щебня, песка, минерального порошка), водного раствора ПАВ и катионной битумной эмульсии. В зависимости от гранулометрического состава ЛЭМС подразделяются на щебеночные и песчаные. Щебеночные рекомендуется устраивать на участках с затрудненными и опасными условиями движения дорог I и II категорий. Песчаные - на участках с легкими и затрудненными условиями движения дорог III-IV категорий. Минеральная часть ЛЭМС подбирается по принципу плотных смесей. Щебеночная фракция 5-10 мм и 5-15 мм должна быть из камня изверженных и метаморфических пород по прочности не ниже 1200. Песчаная фракция 5-0,1 (0,071) мм должна состоять из дробленого песка или смеси природного и дробленого песка в соотношении 50/50 %. Минеральный порошок из карбонатных пород (лучше активированный) должен содержаться в смеси в таком объеме, чтобы общее количество частиц мельче 0,071 мм в смеси составляло 5-15 %. В качестве вяжущего используются катионоактивные битумные эмульсии класса ЭБК-2 и ЭБК-3, содержащие 50-55 % битума (табл. 20.6).
Смеси | компоненты, % по массе |
|||||||
щебень гранит- ный (фракция) | песок | минераль- ный порошок | портланд- цемент | вода для предварительного смачивания | битумная эмульсия (в пересчете на битум) |
|||
5-15 мм | 5-10 мм | дробленый компонент | природ- ный |
|||||
Щебеночная | 50 | - | - | 38 | 12 | - | 6-8 | 8-9 |
Щебеночная | 60 | - | 20 | 17 | 3 | - | 6-8 | 7,5-8,5 |
Щебеночная | 60 | - | 20 | 17 | - | 1-3 | 5-7 | 8-9 |
Щебеночная | - | 50 | - | 38 | 12 | - | 6-8 | 8-9 |
Щебеночная | - | 50 | 18 | 20 | 12 | - | 6-8 | 8-9 |
Щебеночная | - | 60 | 20 | 17 | 3 | - | 6-8 | 7,5-8,5 |
Щебеночная | - | 50 | 27 | 20 | - | 1-3 | 5-7 | 8-9 |
Песчаная | - | - | 60 | 37 | 3 | - | 8-12 | 7-9 |
Песчаная | - | - | 55 | 40 | 5 | - | 8-12 | 7-9 |
Песчаная | - | - | 50 | 45 | 5 | - | 8-12 | 7-9 |
Песчаная | - | - | 60 | 37 | - | 1-3 | 8-10 | 7-9 |
Расход битумной эмульсии в пересчете на битум 7-9 %. Количество ПАВ в водном растворе зависит от его вида (четвертичные соли аммония 0,1-0,6 %, адгезионная битумная присадка БП-3 0,5-1,0 % к массе воды). Расход воды для предварительного смачивания ориентировочно 5-12 % массы минеральных материалов. Его уточняют в лаборатории и корректируют на месте приготовления ЛЭМС с учетом влажности минеральных материалов и их температуры. Время распада эмульсии в ЛЭМС должно составлять 40-120 с. Распад эмульсии должен произойти немедленно после распределения смеси на поверхности покрытия. Приготовление и распределение ЛЭМС осуществляется специальной однопроходной машиной (рис. 20.13).
Рис. 20.13. Передвижная установка для приготовления и распределения литой эмульсионно-минеральной смеси:
1 - резервуар для воды; 2 - бункеры для песка; 3 - бункер для минерального порошка; 4 - объемная дозировка присадки; 5 - подана воды и присадки; 6 - подача эмульсии; 7 - смеситель; 8 - распределитель; 9 - конвейер; 10 - резервуар для присадки; 11 - резервуар для эмульсии
Толщина укладываемого слоя: для песчаной ЛЭМС - 5-10 мм с расходом 20-25 кг/м 2 , для щебеночной 10-15 мм с расходом 25-30 кг/м 2 . По предварительно очищенному и обработанному водой покрытию распределяют ЛЭМС при непрерывном движении машины. Уплотнение ЛЭМС не требуется. Движение транспорта можно открывать через 2-4 ч после окончания работ с ограничением скорости до 40 км/ч в течение 1-2 сут.
Ширина укладываемого слоя зависит от ширины распределительного бункера и обычно составляет 2,5-3,75 м. Скорость распределения регулируется в зависимости от температуры воздуха и свойств исходных материалов, при этом должна быть такой, чтобы распределение смеси (при выходе из распределительного короба) совпадало с началом распада битумной эмульсии, что предотвращает расплывание смеси по поверхности покрытия.
Свойства готового слоя из ЛЭМС приведены в табл. 20.7.
Таблица 20.7
Показатели свойств эмульсионно-минеральных смесей
Показатели | Значение показателя | Метод испытания |
Водонасыщение, % от объема для слоев из смесей | ||
щебеночных | 3,5-4,5 | ГОСТ 12801-98 |
песчаных | 1,5-3,0 | Тоже |
Набухание (% от объема), не более | 7,0 | Тоже |
Коэффициент водостойкости при длительном водонасыщении, не менее для смесей | ||
щебеночных | 0,75 | Тоже |
песчаных | 0,80 | Тоже |
Скорость распада эмульсий, с не менее | 120 | Пособие по устройству поверхностных обработок на автомобильных дорогах (к СНиП 3.06.03-85 ) |
Рабочий цикл укладки защитного слоя включает следующие технологические операции (рис. 20.14): загрузка бункеров и емкостей машины компонентами ЛЭМС на притрассовом складе; переезд машины к месту производства работ; укладка защитного слоя на огражденном участке; переезд машины для загрузки на притрассовом складе.
Рис. 20.14. Циклограмма выполнения производственного процесса по укладке защитного слоя из литой эмульсионно-минеральной смеси на сменной захватке 1000 м шириной 3,75 м (3750 м 2)
Поверхностная обработка с использованием битумных шламов. Битумные шламы являются разновидностью эмульсионно-минеральных смесей литой консистенции и состоят из минеральных материалов (щебня, песка, минерального порошка), битумной пасты и воды. Так как битумные пасты распадаются и твердеют по мере испарения из них воды, применение битумных шламов возможно только в сухую погоду. В зависимости от зернового состава битумные шламы подразделяются на песчаные (п) и щебеночные (щ) - А - крупно - (размером щебня до 25 мм более 40 %), Б - средне - (размером щебня до 25 мм от 20 до 40 %) и В - мелкозернистые (размером щебня до 15 мм менее 20 %) I и II марок. Тот или иной вид шлама рекомендуется использовать на дорогах разных категорий в зависимости от условий движения транспорта .
Время высыхания смесей должно быть не более 2 ч. Перед укладкой битумного шлама покрытие очищают от пыли и грязи, при значительном количестве трещин их прочищают. В зависимости от состояния покрытия его предварительную обработку проводят по-разному: плотные покрытия увлажняют (1-2 л/м 2); пористые покрытия и все виды покрытий при производстве работ в осеннее время подгрунтовывают битумной пастой или эмульсией (не менее 60 % воды из расчета 0,2 л битума на 1 м 2); покрытия с недостатком органического вяжущего и на основе минеральных вяжущих обрабатывают путем распределения слоя пасты исходя из нормы расхода битума 0,4-0,8 л/м 2 . Ориентировочный расход песчаных шламов составляет 5-15 кг/м 2 , щебеночных 10-30 кг/м 2 . Меньшие значения относятся к смесям с меньшими размерами зерен минерального материала. Уложенную полосу ограждают от наезда транспортных средств. При достижении влажности смеси 6-8 % по слою допускается движение транспортных средств или его уплотняют самоходными катками на пневмошинах массой 8-10 т (3 прохода по одному следу). Скорость движения транспорта ограничивают: в течение первых суток до 30 км/ч, затем - до 40 км/ч до тех пор, пока слой не сформируется настолько, чтобы зерна минерального материала не вырывались из слоя. Для полного уплотнения слоя требуется 20-30 сут.
Строительство тонкослойных слоев износа и защитных слоев из литых эмульсионно-минеральных смесей по способу типа «Сларри Сил», который представляет собой уложенную и сформировавшуюся литую эмульсионно-минеральную смесь, состоящую из катионоактивной битумной эмульсии, минерального материала, воды и специальных добавок. Толщина слоя износа в уплотненном состоянии 5-15 мм.
Слой типа «Сларри Сил» устраивается с целью предотвращения отрицательного воздействия природно-климатических факторов на дорожную конструкцию, восстановления слоев износа, обеспечения необходимых сцепных свойств дорожного покрытия.
В зависимости от гранулометрического состава используемых материалов слой износа «Сларри Сил» подразделяют на два типа в соответствии с требованиями, изложенными в табл. 20.8 [58 ].
Таблица 20.8
Гранулометрический состав минеральной части литых эмульсионно-минеральных смесей
Размер отверстий, мм | Содержание частиц мельче данного размера, % по массе | Точность дозирования, % по массе |
|
тип I | тип II |
||
10 | 100 | 100 | ±5 |
5 | 90-100 | 70-90 | ±5 |
2,5 | 65-90 | 45-70 | ±5 |
1,25 | 45-70 | 28-50 | ±5 |
0,63 | 30-50 | 19-34 | ±5 |
0,315 | 18-30 | 12-25 | ±4 |
0,14 | 10-21 | 7-18 | +3 |
0,071 | 5-15 | 5-15 | ±2 |
Для приготовления литых эмульсионно-минеральных смесей должен использоваться щебень из плотных горных пород по ГОСТ 8267-93 после отгрохачивания частиц крупнее 10 мм.
Гранулометрический состав минеральной части литых эмульсионно-минеральных смесей должен соответствовать табл. 20.8. Для обеспечения требований к гранулометрическому составу смесей в минеральную часть могут быть введены минеральный порошок по ГОСТ Р 52129-2003 и цемент по ГОСТ 10178-85 .
Минеральная часть ЛЭМС для устройства тонкослойных холодных покрытий подбирается по типу плотных и может состоять из смесей фракций 0-3 мм, 0-5 мм, 0-8 мм, 0-11 мм, с использованием щебеночных отсевов из трудношлифуемых горных пород марки не ниже 1000. Крупные фракции должны быть преимущественно кубовидной формы. Содержание фракции менее 0,071 мм должно быть 5-15 %. Для регулирования времени распада эмульсии применяют цемент марки не ниже 400. Содержание свободной извести в цементе не ограничивается, а его расход составляет до 2 % от массы каменных материалов.
Песок, щебень и в случае необходимости минеральный порошок перед использованием должны быть смешаны в определенных пропорциях с помощью специальных машин типа «REVSON 73830».
В качестве вяжущего в ЛЭМС применяют катионные эмульсии прямого типа классов ЭБК-2 и ЭБК-3 с содержанием битума 60-65 %. Марка битума в битумной эмульсии должна соответствовать рекомендуемой ГОСТ 9128-97 для конкретной дорожно-климатической зоны.
В условиях I и II дорожно-климатических зон, а также при интенсивности движения более 10000 авт./сут целесообразно использовать полимермодифицированные битумные эмульсии. Получение полимермодифицированной битумной эмульсии осуществляется как путем введения катионоактивных латексов «Бутонал SL 170К», «Родкем 600», «Интерлатекс АФ» и других, совместимых с эмульсией, в процессе приготовления, так и с использованием битумов, модифицированных другими добавками. Содержание модификатора в остаточном битуме модифицированной эмульсии должно быть в пределах 2-4 % по массе. Скорость распада эмульсии регулируют с помощью аддитивных добавок, вид подбирается в лаборатории. В качестве замедлителя скорости распада смеси используются сульфат алюминия, соли моноаминов, полиаминов, амидоаминов по техническим условиям заводов-изготовителей.
В качестве ускорителя времени твердения добавки, улучшающей консистенцию смеси, может использоваться цемент марок 500 или 400, для обеспечения лучшего сцепления вяжущего с каменными материалами и снижения расхода аддитивных добавок, %, от массы каменных материалов. Техническая вода должна иметь жесткость не менее 6 мг-экв/л.
Время распада при смешивании смесей типа «Сларри Сил» должно составлять не менее 180 с. Время распада зависит от целого ряда факторов: минерального состава и зернового состава минеральной части, состава эмульсии, природы эмульгатора, соотношения компонентов в смеси, температуры окружающего воздуха. Поэтому подбор составов смесей должен происходить с учетом вышеперечисленных факторов.
При слишком медленном распаде эмульсии возникает опасность стекания жидкой смеси с поверхности или ее расслоения. Во избежание этих явлений при подборе составов эмульсионно-минеральных смесей контролируют момент отвердения поверхности смеси. Тест для установления времени отвердевания определяется как промежуток времени с момента укладки до момента, когда «Сларри-система» не может быть перемешана в однородную смесь, а при сжатии образца невозможно горизонтальное смещение; когда промокательная салфетка не пачкается при легком соприкосновении с поверхностью образца; когда эмульсия не может быть разбавлена или вымыта из образца.
Более точно момент отвердения смеси находят с помощью специального прибора - модифицированного определителя силы сцепления. При помощи этого прибора определяют и время открытия движения. Время открытия характеризуется тем, что слой износа сформировался до такой степени, что можно открыть движение автомобилей с ограниченной скоростью.
Время отвердения эмульсионно-минеральных смесей должно составлять не более 30 мин, а время открытия движения в зависимости от погодных условий - не более 4 ч.
Не допускается производить работы по укладке эмульсионно-минеральной смеси:
При температуре окружающего воздуха ниже 10°С;
В условиях дождя;
При прогнозе снижения температуры воздуха в месте производства работ до 0°С в течение ближайших 24 ч после укладки.
Для приготовления и укладки литых эмульсионно-минеральных смесей применяются специальные машины типа «Macropaver» и «Minimac» (США), AZ Ко Nobel (Швеция), «Wiero» (Германия), «Elma» (Италия) и др.
Процесс строительства включает очистку и подготовку покрытия; устройство тонкослойного покрытия из ЛЭМС (включая загрузку укладывающих машин); уход и регулирование движения по свежеуложенному слою. Подготовка покрытия заключается в проведении подгрунтовки эмульсией с расходом 0,4-0,6 л/м 2 в зависимости от степени изношенности покрытия. К устройству покрытия необходимо приступать непосредственно после полного распада эмульсии, нанесенной на покрытие при подгрунтовке. Минимальный срок ожидания после подгрунтовки 30 мин. В процессе укладки смеси необходимо контролировать процесс распада эмульсии и консистенцию смеси путем изменения количества воды и раствора аддитивной добавки. Расход других компонентов не меняется. Необходимо следить и за точностью дозировки минеральных компонентов. Расход эмульсии устанавливается строго по расчету. Количество воды зависит от погоды: в холодную погоду ее меньше, в жаркую - больше. Расход воды при введении непосредственно в смесь составляет в среднем 12 % от массы каменных материалов. Непосредственно перед укладкой смеси производится увлажнение покрытия дороги. Увеличение температуры смеси ускоряет процесс распада эмульсии. Поэтому температура воздуха должна измеряться ежечасно (особенно в жаркие дни), чтобы уточнять величину аддитивной добавки. Слой покрытия сразу после укладки должен иметь темно-коричневый цвет. Через 30-60 мин покрытие становится черного цвета. Открытие движения по свежеуложенному покрытию излитой эмульсионно-минеральной смеси разрешается не менее чем через 1 ч после укладки, когда автомобили не оставляют на нем следов. В холодную погоду этот срок увеличивается. В дождь движение автомобилей не разрешается. После открытия движения скорость автомобилей ограничивается до 40 км/ч на период 2-8 ч. В случае дождя движение по участку дороги с ограниченной скоростью продлевается как минимум на 2 ч после окончания дождя.
Опыт показывает, что жидкая холодная эмульсионно-минеральная смесь «Сларри Сил» легко распределяется и разравнивается. В результате образуется защитный слой, не пропускающий воду в нижележащие слои дорожной одежды, устраняются мелкие неровности, покрытие приобретает однообразный цвет и фактуру, похожие на асфальтобетонное покрытие.
Применение прочного щебня и дробленого песка позволяет обеспечить достаточно высокие сцепные качества и хорошую сопротивляемость износу, а также низкий уровень шума. Поскольку износ таких слоев происходит в основном за счет истирания, срок их службы достигает 8-10 лет на дорогах с интенсивностью движения, приведенной к легковому автомобилю, до 7000 авт./сут. Возможны иные способы устройства поверхностной обработки, например, из песчано-битумных смесей и смесей с применением комплексных вяжущих. Кафедрой строительства и эксплуатации дорог МАДИ разработаны песчано-резинобитумные смеси с резиновой крошкой размером 0-(1,5-2) мм (8-10 % по массе), при распределении которых слоем 1,5-2 см получают слой износа, обеспечивающий хорошее сцепление, бесшумное движение и легкое удаление с поверхности воды и ледяной пленки. Хороший результат получен при строительстве мастичного слоя износа толщиной 2-3 см с содержанием щебня 70-75 %.
Поверхностная обработка – технологический процесс устройства на дорожных покрытиях тонких слоев с целью обеспечить шероховатость, водонепроницаемость, износостойкость и плотность покрытий. Слой, устраиваемый этим способом, также называют поверхностной обработкой
Поверхностные обработки используются:
- либо как профилактический слой, который закрывает и предохраняет в плохую погоду основные конструктивные слои дорожных покрытий от преждевременного разрушения;
- либо как слой износа, подверженный стиранию в процессе движения, предохраняя наилучшим образом структуру дороги. Такому слою требуется только периодическое обновление для придания структуре дороги ее первоначальных качеств;
- либо как верхний слой дорожного покрытия с характеристиками шероховатости, обеспечивающими сцепление и хорошее дренирование поверхностных вод, приводящими к значительному понижению порога аквапланирования и создающими, благодаря повышенному удельному давлению, хорошее сопротивление формированию гололеда.
Кроме технических преимуществ, поверхностные обработки имеют достаточно конкурентоспособную стоимость по сравнению с комплексом верхних слоев дорожных одежд, используемых в этих случаях.
Существует много различных способов устройства поверхностных обработок, из которых в настоящей статье рассматривается лишь один – использование для этой цели фракционного щебня и различных органических вяжущих, в том числе эмульгированных.
Чтобы создать поверхностную обработку, соответствующую представленным требованиям, необходимо при ее устройстве соблюдать несколько принципиальных положений:
- использовать вяжущее, которое прочно и надолго соединяется с поверхностью покрытия или основания. Это соединение называется парой «вяжущее – основа»;
- каменный материал должен быть прикреплен к покрытию или основанию, а каждая щебенка должна быть прочно соединена с соседними. Это взаимодействие называют парой «вяжущее – щебень»;
- количество вяжущего должно быть достаточным, чтобы покрыть пленкой каждую щебенку на необходимую высоту и заполнить все микротрещины покрытия, но не быть избыточным, чтобы не выступать на поверхность щебеночного слоя. Это основной принцип дозировки и распределения вяжущего;
- каменный материал должен быть чистым, обладать высокими физико-механическими свойствами (прочностью, морозостойкостью, сопротивлением истиранию и др.), иметь определенные формы и размеры. Это основные требования к каменным материалам;
- количество каменного материала должно быть достаточным, чтобы создать нужную структуру поверхности, но не быть излишним, чтобы избежать необходимости удаления его. Это принцип дозировки и распределения каменного материала;
- каждая щебенка должна занять наиболее стабильное положение, а все вместе должны создавать сплошной монолитный слой с шероховатой поверхностью. Это основной принцип уплотнения.
Таковы основные принципы обеспечения высокого качества поверхностной обработки. Кроме того, есть ряд дополнительных условий:
- все работы по устройству поверхностной обработки должны быть выполнены в наиболее благоприятных условиях погоды. Это принцип назначения сроков выполнения работ;
- до начала работ должны быть решены все организационные вопросы, касающиеся поставки материалов, подготовки машин и оборудования. Это принцип организации работ;
- в процессе работ должны строго выполняться требования к технологии производства работ и качеству применяемых материалов. Это принцип организации контроля качества.
Поверхностные обработки с использованием фракционированного щебня устраивают преимущественно на участках дорог с опасными и затрудненными условиями движения на дорогах I – III категорий.
В зависимости от типа и состояния покрытия поверхностные обработки могут быть одиночными и двойными; на цементобетонных покрытиях – только двойными.
Требования к материалам
Щебень
Щебень поверхностной обработки воспринимает и передает на нижележащие слои нагрузку от автомобилей, служит слоем износа и обеспечивает сцепление между дорогой и колесами автомобилей.
Каменный материал, применяемый для устройства поверхностной обработки, должен обладать высокими физико-механическими свойствами, такими как прочность, морозоустойчивость, сопротивление удару и износу (истиранию), хорошей прочностью сцепления с вяжущим и т.д. Соответствие горной породы вяжущему определяют путем испытания в лабораторных условиях на прочность сцепления.
Рис. 1. Влияние формы щебенок на стабильность их положения
Форма щебенок должна быть как можно ближе к кубической, чтобы обеспечить устойчивое положение на поверхности покрытия. Яйцевидная форма щебенок, так называемая форма «колумбового яйца», не имеет стабильного положения. Плоские плитки и щебенки в виде вытянутой иглы хрупки и плохо укладываются в покрытие (рис. 1).
Щебень поверхностной обработки должен быть очень чистым, что обуславливает его тщательную мойку во время производства. Наличие глины, даже в очень слабых пропорциях, весьма нежелательно: глина крайне гидрофильна, и сильное разбухание, которое происходит при наличии воды, приводит к тенденции разрыва связки «вяжущее – щебень».
Правильно выбранная форма и размер щебенок формируют шероховатость поверхностной обработки, обеспечивают снижение шума в салоне автомобиля при движении.
Прицепной битумощебнераспределитель БЩР-375 совместного производства ОАО «Строммашина» и фирмы Breining (Fayat Group), Германия
Важное значение имеет выбор размера щебня. Установлено, что размеры щебня порядка 10–15 и 15–20 мм вызывают довольно высокий уровень шума в салоне автомобиля и мешают прослушиванию музыки при скорости движения более 130 км/ч. Исходя из этого, отдают предпочтение поверхностной обработке из щебня фракций 5–10 мм.
Еще один фактор, который необходимо учитывать при назначении требований к размеру щебня, состоит в исключении возможности разбития лобовых стекол автомобилей щебенками, вылетающими из-под колес автомобилей при движении с высокой скоростью. Использование мелкозернистого щебня позволяет почти полностью решить эту проблему.
Для устройства поверхностных обработок применяют щебень марки не ниже 1200 по ГОСТ 8267-82 из трудношлифуемых изверженных и метаморфических горных пород для автомобильных дорог I и II категорий, марки 1000 – для дорог III категории и марки не ниже 800 – для дорог IV категории, фракций 5–10, 10–15, 15–20 мм (допускается применение щебня фракций 5–15 и 10–20 мм при условии обеспечения коэффициента сцепления) преимущественно кубовидной формы зерен (зерна пластинчатой формы составляют не более 15%); содержание пылеватых, глинистых и илистых частиц в щебне не должно превышать 1% массы. Выбор фракции щебня производят в зависимости от твердости дорожного покрытия.
Вяжущее
При устройстве поверхностной обработки в качестве вяжущих используют вязкие битумы, битумы с добавками дегтей, битумы и дегти с добавками полимеров, битумные эмульсии.
Вяжущее обеспечивает гидроизоляцию покрытия, приклеивание каменного материала к покрытию или основанию и соединение щебенок в единый слой.
Марку битума выбирают по ГОСТ 22245-90 с учетом дорожно-климатической зоны: для I – БНД 90/130 и БНД 130/200, для II и III – БНД 60/90, БНД 90/130, БНД 130/200, БН 60/90, БН 90/130 и БН 130/200, для IV и V – БНД 60/90, БНД 90/130, БН 60/90 и БН 90/130 .
Битум должен выдерживать испытание на сцепление со щебнем, используемым для устройства поверхностной обработки. При неудовлетворительном сцеплении битума со щебнем следует использовать добавки соответствующих ПАВ или производить предварительную обработку щебня дегтем или смесью битума с дегтем.
Применяемые каменноугольные дегти должны иметь марку Д-5, Д-6 или Д-7 по ГОСТ 4641-80 и использоваться на автомобильных дорогах не выше III категории. На участках дорог, проходящих по населенным пунктам, применение каменноугольных дегтей не разрешается.
При устройстве поверхностной обработки с использованием эмульсий применяют преимущественно катионные битумные эмульсии класса ЭБК-1, ЭБК-2, отвечающие требованиям ГОСТ 52128. В условиях III – IV дорожно-климатических зон и при благоприятных погодных условиях во II зоне допускается применение анионных эмульсий класса ЭБА-1, ЭБА-2. Эмульсии должны выдерживать испытание на сцепление пленки вяжущего со щебнем.
При устройстве поверхностной обработки на катионных битумных эмульсиях используют необработанный органическим вяжущим щебень, на анионных эмульсиях – преимущественно черный щебень.
При устройстве поверхностной обработки на дорогах с интенсивностью движения свыше 3000 авт/сут., с движением преимущественно грузовых автомобилей, также в районах с резко континентальным климатом применяют битум и деготь с добавками полимеров. Дегтеполимерное вяжущее используют на дорогах не выше II категории.
Различают несколько видов поверхностных обработок, каждая из которых имеет свою сферу наиболее эффективного применения (рис. 2).
Рис. 2. Виды поверхностных обработок
- Однослойная поверхностная обработка с однократным распределением вяжущего и щебня . Применяется для создания шероховатой поверхности и слоя износа дорожной одежды с достаточной прочностью. Это самый распространенный вид шероховатой поверхностной обработки, наиболее подходящий для всех видов движения. Чаще всего она устраивается из щебня фракций 5–10 мм.
- Однослойная поверхностная обработка с двойным распределением щебня . На слой нанесенного вяжущего сначала рассыпают крупную фракцию щебня (например, 10–15 или 15–20 мм), прикатывают катком, а затем рассыпают более мелкую фракцию щебня (например, 5–10 мм) и уплотняют. Применяется на дорогах с интенсивным движением и высокой скоростью движения. Такая поверхностная обработка способствует улучшенной герметичности покрытия, устранению мелких неровностей и деформаций, лучше распределяет усилия от колес автомобилей. Особенно эффективно такая обработка работает на хорошем жестком основании.
- Двухслойная поверхностная обработка . На первый слой разлитого вяжущего рассыпают крупную фракцию щебня и уплотняют. Затем разливают второй слой вяжущего, рассыпают более мелкую фракцию щебня и окончательно уплотняют. Применяется на покрытиях с недостаточной прочностью, при наличии сетки трещин, ямочности, колей, при высокой интенсивности движения, т.е. в тех случаях, когда необходимо не только создать шероховатый слой износа и защитный слой, но и улучшить ровность, несколько повысить прочность и сдвигоустойчивость. Применяется также на цементобетонных покрытиях.
- Поверхностная обработка типа «сэндвич» . На покрытие рассыпают щебень более крупной фракции, затем распределяют вяжущее, рассыпают щебень мелкой фракции и уплотняют. Структура получаемого слоя поверхностной обработки сравнима с однослойной поверхностной обработкой, устроенной путем розлива вяжущего и двойной россыпью щебня. Такая поверхностная обработка рекомендуется при неоднородном по ровности покрытии для его выравнивания и некоторого усиления. Применяется на дорогах второстепенного, местного значения.
При выборе способа устройства поверхностной обработки покрытий необходимо учитывать ее назначение, условия движения на дороге, климатические условия района строительства, показатель твердости дорожного покрытия, наличие материалов и средств механизации.
Технология производства работ
Существует два способа устройства поверхностных обработок:
- традиционный – с раздельным распределением материалов;
- способ с синхронным распределением вяжущего и щебня.
Традиционный способ
Работы по устройству одиночной поверхностной обработки традиционным способом с использованием битумов, дегтебитумов, битумо- и дегтеполимерных вяжущих производят в следующем порядке:
- розлив вяжущего;
- распределение щебня;
- укатка;
- уход в период формирования.
Работы по устройству двойной поверхностной обработки производят в такой последовательности:
- подготовка поверхности (очистка от пыли и грязи) и ремонтные работы;
- первый розлив вяжущего;
- первая россыпь щебня;
- укатка;
- второй розлив вяжущего;
- вторая россыпь щебня (между первой и второй россыпью щебня допускается перерыв не более 3–5 суток);
- укатка;
- уход в период формирования.
Очистку покрытия от пыли и грязи выполняют механическими щетками, наиболее загрязненные участки промывают с помощью поливомоечной машины.
Струны щеток, какова бы ни была их природа (нейлон, сталь), должны быть в хорошем состоянии и достаточно жесткими, чтобы обеспечить эффективное соскабливание.
В случаях, когда старое покрытие не удается полностью очистить от пыли и грязи, оставшихся в мелких трещинах и впадинах, его необходимо подгрунтовать путем розлива жидкого битума по норме 0,3–0,5 л/м 2 или битумной эмульсией с расходом 0,5–0,8 л/м 2 .
Розлив вяжущего производят автогудронатором. Для равномерного розлива вяжущего необходимо обеспечить бесперебойность действия сопел, равномерность работы насоса и требуемую скорость перемещения гудронатора.
Сопла должны быть теплоизолированы и оснащены устройством обогрева, позволяющим поддерживать или обеспечивать определенную температуру вяжущего.
В зависимости от выбранного вяжущего и от ширины обрабатываемой поверхности водитель определяет, с помощью элементов регулировки гудронатора (номограмма, вычислительный диск, программирование), необходимое соотношение между скоростью передвижения и количеством оборотов насоса, который определяет дозирование вяжущего на покрытии. Во время осуществления распределения соотношение между скоростью автомобиля и количеством оборотов насоса поддерживается постоянным, путем, либо автоматического слежения, либо непосредственного считывания шофером показаний тахометра и счетчика оборотов.
Во время розлива температура битума марок БНД 60/90, БНД 90/130, БН 60/90 и БН 90/130 должна составлять 150–160° C; марок БНД 130/200 и БН 130/200 – 100–130° C; температура полимерно-битумного вяжущего – 140–160° C; дегтеполимерного вяжущего – 100–110° C.
Распределение щебня производят самоходным щебнераспределителем, автомобилем-самосвалом с навесным приспособлением или другим механизмом, обеспечивающим быстрое и равномерное распределение щебня. Кузов всех этих механизмов должен быть плоским и без локальных деформаций. Высота сброса щебня должна быть небольшой, чтобы обеспечить более однородное распределение заполнителя на покрытии. Автощебнераспределители могут быть оснащены системой гидравлического расширения, позволяющей изменять без остановки рабочую ширину от 2,50 до 4 м.
Щебень распределяют непосредственно после розлива вяжущего слоем в одну щебенку и укатывают катком 6–8 т за 4–5 проходов по одному следу.
Уплотнение поверхностной обработки покрытий обеспечивает укладку щебня и его закрепление на покрытии. Пневматические шинные уплотнители великолепно обеспечивают эти функции. Они приспосабливаются к неровностям дороги и не дробят щебень.
В течение первых дней эксплуатации необходимо осуществлять уход за формирующимися слоями. Незакрепившийся щебень должен быть удален с покрытия не позднее чем через 1 сутки после открытия движения. Скорость движения автомобилей ограничивают 40 км/ч и регулируют по ширине проезжей части.
Выброшенный лишний щебень подбирается очистительными машинами-сборщиками, очистительными машинами и втягивающими машинами. Оснащенные различными щетками и всасывающими соплами, они оборудованы сборными емкостями для мелкозернистого материала, который они поднимают. Эти всасывающие механизмы представляют большой прогресс в технологии поверхностных покрытий, поскольку они позволяют значительно снизить самый большой вред от загрязнения: битье ветровых стекол автомобилей после возобновления движения.
Поверхностную обработку с использованием битумных эмульсий выполняют в следующем порядке:
- подготовка поверхности (очистка от пыли и грязи) и выполнение в случае необходимости ремонтных работ;
- смачивание поверхности водой (в жаркую сухую погоду);
- розлив эмульсии по покрытию в количестве 30% нормы;
- распределение щебня в количестве 70% нормы;
- розлив оставшейся эмульсии (70%);
- распределение оставшегося щебня (30%);
- укатка;
- уход в период формирования.
Температуру и концентрацию эмульсии устанавливают в зависимости от погодных условий. При температуре воздуха ниже 20° C рекомендуется применять эмульсию с температурой 40–50° C и концентрацией битума 55–60%. Подогрев эмульсии до указанной температуры следует производить непосредственно в автогудронаторе в процессе транспортирования к месту работ. При температуре воздуха выше 20° C эмульсию применяют в холодном состоянии, а концентрацию битума можно снизить до 50%.
Распределение щебня осуществляют таким образом, чтобы щебень распределялся не далее 20 м от автогудронатора, разливающего эмульсию.
Уход за поверхностной обработкой с применением битумных эмульсий выполняется так же, как и при использовании битума. При использовании анионных эмульсий движение автомобилей открывается не ранее чем через 1 сутки после окончания работ.
Технология поверхностной обработки с синхронным распределением вяжущего и щебня
Основным отличием новой технологии устройства поверхностной обработки является синхронное, практически одновременное распределение вяжущего и россыпь щебня (рис. 3).
Рис. 3. Поверхностная обработка с синхронным распределением материалов
При устройстве поверхностной обработки традиционными методами разрыв во времени между распределением вяжущего и россыпью щебня лимитируется временем остывания горячего битума и может достигать 1 часа.
При синхронном распределении вяжущего и щебня разрыв между этими операциями не превышает 1 сек, что существенно сказывается на повышении качества поверхностной обработки, как при использовании в качестве вяжущего горячего битума, так и битумной эмульсии.
Повышение качества при использовании в роли вяжущего горячего битума объясняется тем, что за столь короткий промежуток времени битум не успевает остыть и сохраняет жидкую консистенцию и высокую клеящую способность. В результате битум хорошо проникает в микропоры щебня и покрытия, обволакивает каждую щебенку и прочно приклеивает их к покрытию и одну к другой.
Уплотнение уложенного слоя также происходит при горячем состоянии битума, что обеспечивает максимальный эффект уплотнения.
При использовании в роли вяжущего битумной эмульсии высокое качество поверхностной обработки с синхронным распределением вяжущего и щебня объясняется тем, что за столь короткий промежуток времени распад эмульсии только начнется, и эмульсия в жидком состоянии заполнит все микропоры щебня и покрытия, покроет каждую щебенку тонким слоем вяжущего и обеспечит возможность хорошего уплотнения слоя поверхностной обработки.
Синхронное распределение решает все проблемы организации и координации работ, возникающие при асинхронном распределении, поскольку при каждой остановке в распределении щебня автоматически прекращается и распределение вяжущего. Существенно сокращаются простои из-за климатических условий и повышается производительность работ. Это важно при использовании вяжущих высокой вязкости, но особенно важно при работе в неблагоприятных погодных условиях.
Синхронное распределение вяжущего и щебня благоприятно сказывается на формировании сопряжения между вяжущим и щебнем, что гарантирует высокие эксплуатационные характеристики поверхностной обработки, уменьшает риск неудачи работ из-за разницы температур основания и вяжущего, а также из-за наличия сухих тонкодисперсных фракций при устройстве поверхностных обработок с использованием эмульсий.
Опыт показывает, что высокий уровень качества поверхностной обработки с синхронным распределением вяжущего и щебня позволяет добиться поразительных результатов, когда тонкий слой щебня и вяжущего выдерживает интенсивное воздействие колес автомобилей в течение 10–15 лет.
Таким образом, синхронное распределение вяжущего и щебня с временем задержки в 1 секунду является самым важным нововведением в практике поверхностной обработки за последние 20 лет.
Для реализации идеи поверхностной обработки с синхронным распределением вяжущего и щебня фирма SECMAIR разработала и выпускает широкую номенклатуру битумощебнераспределителей различной производительности, а также других машин для содержания и ремонта дорожных покрытий с использованием щебня, обработанного битумом или битумной эмульсией.
Выпускаемые машины могут работать при движении передним ходом или при движении задним ходом (рис. 4).
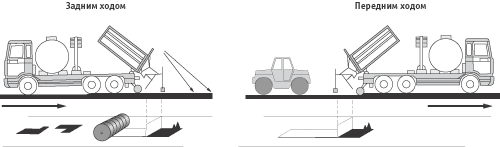
Рис. 4. Принципы работы машин для поверхностной обработки
Учитывая значительный интерес российских дорожников к внедрению технологии поверхностной обработки с синхронным распределением вяжущего и битума, французская фирма SECMAIR и ГУП Саратовский научно-производственный центр «Росдортех» создали в г. Саратове совместное производство машин типа Chipsealer.
В 1999 г. начат выпуск следующих машин:
- Chipsealer-40 . Это высокопроизводительное оборудование, предназначенное для устройства шероховатых поверхностных обработок в больших объемах. Оборудование Chipsealer-40 монтируется на базе полуприцепа Caizer и обладает полностью автономной системой энергообеспечения. За один цикл загрузки кузова щебнем позволяет выполнять поверхностную обработку на полосе шириной 3,75 м длиной до 800 м за 10 минут.
- Chipsealer-26 выполнен на базе российского полуприцепа СЗАП – 9905. В качестве автомобиля-тягача могут использоваться седельные тягачи МАЗ и КамАЗ. Имеет такие же характеристики, как и Chipsealer-40, но меньшие габариты кузова для щебня и резервуара для вяжущего.
- Chipsealer-19 – предназначен для выполнения ремонта дорожных покрытий и устройства шероховатых поверхностных обработок в небольших объемах.
Машины типа «Стоппер»
Применяются для сдерживания эрозии покрытия на ранней стадии путем устройства местной поверхностной обработки на участках шелушения и выкрашивания покрытия, появления мелких трещин, сетки трещин, мелких выбоин и колей. Машина имеет на одном шасси емкость для вяжущего, кузов для щебня, грейферный ковш для загрузки щебня в кузов и распределительные устройства для нанесения битума и щебня (рис. 5).
Еще одним отличием является наличие у «Стоппера» уплотняющего блока из 8 пневматических гладких колес, которые при помощи 4 гидравлических домкратов опускаются на поверхность в рабочее положение и поднимаются вверх в транспортное положение. Это особенно важно для ускоренного формирования ремонтного слоя в холодном и влажном климате. В сухом и жарком климате указанное формирование происходит под действием движущегося транспорта, и необходимость в уплотняющем блоке отпадает. Кроме того, «Стопперы» приспособлены для проведения локального ремонта с применением поверхностной обработки.
Машины для устройства поверхностной обработки
Для устройства поверхностной обработки традиционным способом, т.е. с раздельным распределением вяжущего и щебня, используют автогудронаторы и распределители щебня.
Автогудронаторы различают и выбирают по:
- вместимости цистерны (грузоподъемности);
- ширине распределения вяжущего; при этом, как правило, выбирают ширину распределения равной ширине полосы движения дороги или на 5–10 см меньшую.
Распределители щебня различают по:
- вместимости (емкости) бункера для щебня;
- ширине распределения щебня; при этом, как правило, ширину распределения щебня принимают равной ширине распределения вяжущего;
- типу хода (движения): прицепные и навесные базовые машины. Как правило, в качестве базовых машин для прицепных и навесных распределителей щебня используют автомобили-самосвалы.
Для устройства поверхностной обработки методом синхронного (одновременного последовательного) распределения вяжущего и щебня используют битумо-(эмульсие)-щебнераспределители.
Битумощебнераспределители различают по:
- ширине обработки, т.е. по соответствию (кратности) этого параметра ширине проезжей части автомобильной дороги;
- емкости (вместимости) бака для вяжущего и бункера для щебня;
- методу загрузки щебнем, т.е. использованию специальных загрузочных машин для загрузки щебня в бункер или специального самозагрузочного оборудования.
На рис. 6 представлены графики выработки (в тыс. м 2) всех трех типов машин: автогудронаторов, распределителей щебня и битумо-(эмульсие)-щебнераспределителей при норме розлива битумной эмульсии в 1,4 и 2,1 л/м 2 и норме распределения щебня в 10,0 и 15,0 кг/м 2 . В зависимости от ширины розлива вяжущего и распределения щебня на рис. 6 представлены также выработка в пог. м полосы обработки.
Представленные графики с учетом величин вместимости бака для вяжущего и бункера для щебня и битумощебнераспределителей показывают, что вместимость бака для вяжущего обеспечивает значительно большую выработку, чем вместимость бункера для щебня. Таким образом, бункер для щебня должен быть заполнен несколько раз для обеспечения выработки вяжущего. Соотношение выработок по вяжущему и щебню для различных битумощебнераспределителей колеблется от 2,0 до 9,5 . Поэтому значительное влияние на сменную выработку (производительность) оказывает метод загрузки щебня.
Совместная работа автогудронатора и прицепного щебнераспределителя ЗАО «Бецема», загружаемого из самосвала
При загрузке щебня в бункер щебнераспределителя (без самозагрузки) на базе с использованием одноковшового фронтального погрузчика или крана с грейфером (челюстным ковшом), т.е. с двойным пробегом от места работы до базы и обратно, затраты времени на одну загрузку составляют от 40 минут до 1 часа 20 минут.
При загрузке щебня в бункер битумощебнераспределителя на месте работ с использованием самозагрузки или с использованием автомобиля-самосвала с краном-манипулятором, оснащенным грейфером, затраты времени на одну загрузку составляют от 10 до 15 минут.
При загрузке щебня в бункер битумощебнераспределителя с самозагрузкой из приемного бункера, расположенного сзади машины и загружаемого из автомобиля-самосвала, даже при остановке битумощебнераспределителя, затраты времени на одну загрузку составляют от 2 до 6 минут.
При расчете загрузка вяжущего совмещена с загрузкой щебня, т.е. производится через две–девять загрузок щебня, скорость движения битумощебнераспределителя принята равной 4 км/ч = 1,1 м/сек = 66 м/мин., ширина распределения принята равной 3 м, коэффициент использования по времени принят равным 0,8 (при загрузке на базе) и 0,6 (при загрузке на дороге), что связано с необходимостью и большой сложностью ритмичной подачи материалов, применением дополнительных машин (автомобилей-самосвалов, автобитумовозов).